[Image above] Fraunhofer researchers have developed a new laser arc application method for coating engine parts with hydrogen-free ta-C. Credit: Fraunhofer; YouTube
Germany has a deadline when it comes to reducing emissions. Specifically, the country’s target is to slash emissions by 40% from their 1990 levels by 2020.
That’s an ambitious goal, and the country’s clean energy policy is the driving force behind its commitment to establishing more energy-efficient practices.
And Germany’s not alone in the pursuit for lower emissions. The U.S. Environmental Protection Agency is working to develop new, stringent standards to reduce emissions, too.
With fuel saving and lower emissions in mind, Andreas Leson and his research team at Fraunhofer Institute for Material and Beam Technology in Dresden, Germany, are looking for ways to cut fuel consumption and CO2 emissions without sacrificing vehicle performance.
And they have zeroed in on an application method for applying diamond-like coatings to reduce friction on vehicle components—such as engine parts—that they say can be scaled up and easily integrated with existing coating machines.
The concept of coating components with diamond-like carbon to reduce friction may be old news, but Leson and his team have “succeeded in producing hydrogen-free ta-C coatings on an industrial scale at a consistent level of quality. These tetrahedral amorphous carbon [ta-C] coatings are significantly harder and thus more resistant to wear than conventional diamond-like coatings,” according to a Fraunhofer news release about the technology.
Friction plays a big part in an engine’s efficiency, so it’s crucial to keep it to a minimum. The ta-C coating reduces friction generated by operation of engine parts to almost zero.
“Carbon is a very special material. As well as being an abundant element in nature, it’s also biocompatible and contains no toxic agents. In the form of diamond, it’s the hardest material in the world. It’s low friction and high resistance to wear are the key qualities we exploit in practical applications,” Leson says in a related video from Fraunhofer.
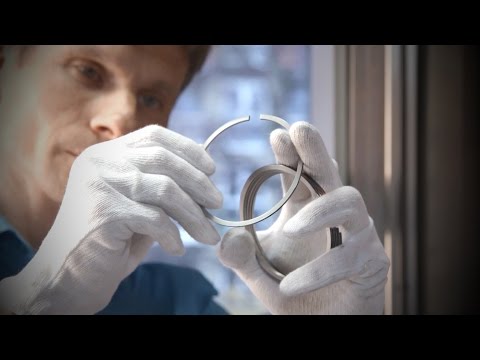
Credit: Fraunhofer; YouTube
The new application technique involves a cutting-edge “laser arc method with which layers of carbon almost as hard as diamond can be applied on an industrial scale at high coating rates and with high thicknesses,” according to the video.
The laser arc method generates plasma that primarily consists of carbon ions. These are deposited as a ta-C coating. To achieve a high-quality coating, a magnetic field is used to remove particles of dirt from the ion beam.
“Nobody had yet managed to produce ta-C on an industrial scale. But now, for the first time, our team at Fraunhofer has succeeded in using a laser arc method to produce good-quality ta-C coatings in a high-volume production environment,” Volker Weihnacht, a researcher at Fraunhofer, says in the video.
The super-hard coating is already being mass-produced under the brand name Nesmuk Diamor to coat professional-quality cutlery, but it offers significant benefits to many industries—specifically, to the automotive industry.
“The customer knows the influence on fuel consumption and the improvement of vehicle performance acceleration on the road… that can mean a double-digit percent reduction in fuel consumption. The coming decade will see the EU introduce even stricter regulations on CO2 emissions, so friction reduction will obviously be one of the methods we’ll use to meet the new targets,” Franz-Josef Wetzel from BMW Group, says in the Fraunhofer video.
Author
Stephanie Liverani
CTT Categories
- Energy
- Environment