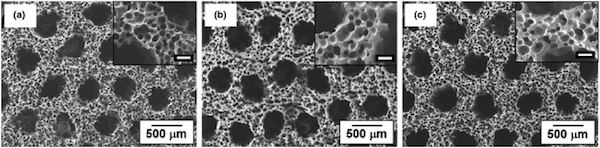
SEM images of samples with various initial alumina contents of (a) 15 vol%, (b) 20 vol%, and (c) 25 vol%, showing the porous structures developed normal to the macrochannel direction. Insets show a highly porous structure of alumina walls (scale = 100 μm). Credit: Moon, et al, JACerS, Wiley.
Corning International’s technology director, Willard Cutler, gave an interesting plenary talk last week at ICACC on porous materials. Much of ceramic science involves densification. However, some applications call for careful engineering of what is not there, namely, the porosity.
Cutler mentioned a number of applications for porous materials, such as catalytic converters, reverse osmosis, diesel particulate filters, ion exchange, sensors, enzyme immobilization, refractories, absorbents, metal filters, bioceramics, and more. Features such as directionality and interconnectedness are tailored depending on the application. For example, both catalytic converter substrates and diesel particulate filters have cellular structures, but gasses must be able to pass through the cell walls of filters in order to trap particulates, while gasses can pass straight through converters. Likewise, mean pore size varies according to application. The mean pore size for a diesel particulate filter is in the range of 10 μm, while that of an ion exchanger is in the range of only 10 nm.
Biomedical materials are an interesting class because nature itself is an excellent engineer and builder of porous materials, and any effort to replicate or create substitutes must adapt to nature, not the other way around. Bone, for example, has highly-aligned unidirectional macrochannel porosity. The channeled unidirectional morphology arrests crack growth and probably offers other protections, too.
Bone tissue researchers have struggled to find a process that duplicates cancellous bone structure. Cancellous bone, sometimes called trabecular bone, is the porous, spongy, interior part of the bone. The ends of long bones, for example, are cancellous. The porosity of these bones varies from 50–90% and is challenging to make independent of the body.
A group out of South Korea reports on a new approach in a Rapid Communication in the January 2014 issue of the Journal of The American Ceramic Society. The method, which the authors call “3D-CoEx,” combines coextrusion with layer-by-layer buildup to create a composite structure with macrochannels and interconnected porosity between them.
The group mixed an alumina and camphene (C10H16) slurry that they coextruded into tubes with camphene cores surrounded by the composite slurry. These tubes were gently stacked and lightly pressed together to make an arrayed structure (see featured image above). Besides providing a support structure for the green bodies, camphene crystallizes into a dendritic structure under low-temperature heat treatment (43°C for 6 h). The camphene was removed by freeze-drying and a structure of alumina with interconnected porosity surrounding macrochannels was left. This delicate green body was sintered at 1600°C for 3 h to densify the alumina walls without losing porosity. As the micrographs show, the resulting structure bears a remarkable resemblance to cancellous bone structure.
The group investigated three levels of alumina content (by volume)—15, 20, and 25%. The corresponding overall porosities ranged from 84 vol% to 68 vol% and alumina wall porosities varied from 76–57 vol%–both within the range of typical cancellous bone porosity.
But there was a striking difference between the compressive strengths of the structures. The 15 and 20 vol% structures had compressive strengths of 2.3 and 6.3 MPa, respectively. However, the compressive strength of the 25 vol% alumina structures climbed to 28.3 MPa, although perpendicular strength was only 5.2 MPa.
The group notes that using camphene to create three-dimensional interconnected porosity “can be tailored simply by adjusting initial alumina content in alumina/camphene slurries.” While they are most interested in making bone scaffolds, they say the technique “can be applied to a variety of materials, including ceramics and metals, which thereby would fit numerous useful applications in diverse fields.”
The paper is “Three-dimensional Ceramic/Camphene-based Coextrusion for Unidirectionally Macrochanneled Alumina Ceramics with Controlled Porous Walls,” by Y-W Moon, et al. (DOI: 10.111/jace.12634).
The paper is one of JACerS editor David Green’s “featured articles” and is open access.
Author
Eileen De Guire
CTT Categories
- Basic Science
- Biomaterials & Medical