[Image above] Laser welded ceramic assembly consisting of a transparent cylindrical cap joined to a ceramic tube. Credit: Garay lab, UC San Diego
The high-temperature resistance of engineered ceramics makes them invaluable to many applications, including airplanes and refractories. Yet that same high-temperature resistance makes it extremely difficult to join ceramics together, hindering creation of complex device geometries.
Currently, ceramics are joined used high-temperature diffusion bonding, which operates on the principle of solid-state diffusion. Instead of melting and resolidifying the materials to be joined, “flat interfaces can be joined at an elevated temperature (about 50%–90% of the absolute melting point of the parent material) using an applied pressure for a time ranging from a few minutes to a few hours,” according to a University of Cambridge webpage explaining the technique.
However, diffusion bonding can be used only in limited situations. “Diffusion bonding requires long-term exposure of entire assemblies to high temperature and often requires precise modeling of shrinkage dynamics to achieve tight tolerances,” researchers explain in a recent paper.
The researchers, from the University of California, San Diego, and the University of California, Riverside, go on to say that lasers, a key to certain additive manufacturing techniques, could be instrumental in welding ceramics. Unfortunately, attempts to weld ceramics using powerful continuous-wave (CW) lasers without high-temperature preheating have been unsuccessful because of macroscopic cracking attributed to thermal shock.
But CW is not the only way to operate lasers. “Successful demonstrations of joining glasses were accomplished with ultrafast pulsed (UF) lasers,” the researchers write in the paper.
Unlike CW lasers, which strike a material continuously with a laser beam, UF lasers strike the material in short pulses. This technique allows the laser to be focused into the material, “stimulating nonlinear and multiphoton absorption processes that lead to localized absorption and melting” in the case of glass, the researchers explain.
In their study, the researchers hypothesized that tuning optical transparency (absorption plus scattering) would allow them to focus laser light into ceramics—placing energy where it can cause localized melting at the interfaces, thus effectively welding ceramic components.
To highlight the versatility of a UF laser welding approach, the researchers demonstrated the technique on both transparent ceramics (with varying absorption properties) and conventionally sintered ceramics (with limited light transparency). They used these ceramics to present two different concepts.
- Transparent ceramics for hermetic (airtight) encapsulation
- Diffuse ceramics for joining simple geometries
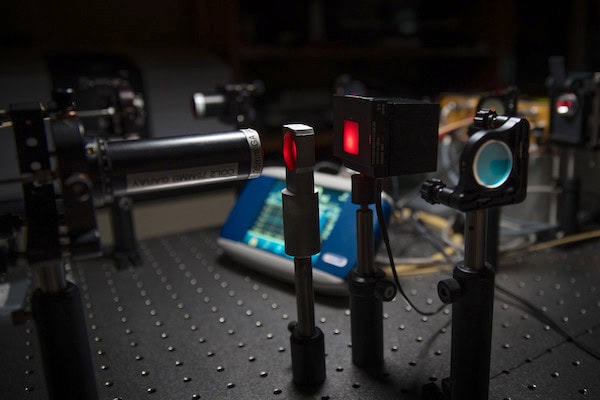
Laser setup used to test and measure the transparency of ceramic materials. Yttria-stabilized zirconia (YSZ) was used to test concept 1; YSZ and polycrystalline alumina (Al2O3) were used to test concept 2. Credit: David Baillot, UC San Diego Jacobs School of Engineering (CC BY 2.0)
The researchers highlight several key parameters necessary to a successful ceramic weld, including
- Dynamic rotation of the ceramics through the beam focus, to ensure not only melting at a point but also continuous melting along the joint interface, and
- Low number of pulses and pulse lengths in the picosecond regime, to induce good energy coupling at a 1-MHz repetition rate.
“The sweet spot of ultrafast pulses was two picoseconds at the high repetition rate of one megahertz, along with a moderate total number of pulses. This maximized the melt diameter, minimized material ablation, and timed cooling just right for the best weld possible,” Guillermo Aguilar, professor and chair of mechanical engineering at UC Riverside, says in a UC San Diego press release.
When compared to metal-to-ceramic assemblies created through diffusion bonding, the UF laser-welded ceramics demonstrated comparable shear strengths—and required less than 50 watts of laser power to create.
The researchers foresee many applications of their UF laser welding technique, especially in terms of electronic assemblies. “Right now there is no way to encase or seal electronic components inside ceramics because you would have to put the entire assembly in a furnace, which would end up burning the electronics,” Javier Garay, professor of mechanical engineering and materials science and engineering at UC San Diego, says in the press release. The UF laser welding technique would allow creation of such assemblies.
Additionally, “The visible-RF light access allowed by ceramic packaging is important for developing optoelectronic devices, facilitating optical communication as well as wireless electronic charging,” the researchers write in the conclusion.
Interested in UF laser welding? Earlier this year we covered a UF laser microwelding technique that successfully joined two very dissimilar materials—metal and glass!
The paper, published in Science, is “Ultrafast laser welding of ceramics” (DOI: 10.1126/science.aaw6699).
Author
Lisa McDonald
CTT Categories
- Manufacturing
- Material Innovations