[Image above] Researchers at Forschungszentrum Jülich found potassium bromide keeps nonoxide ceramics from oxidizing when synthesized in normal air. They synthesized multiple nonoxide ceramics and also dense (left) and porous (center) titanium. Credit: Hiltrud Moitroux, Forschungszentrum Jülich
There are two main categories when it comes to ceramics: oxides, and nonoxides. Between the two, nonoxide ceramics hold quite a few advantages, including increased refractoriness, higher strength and stiffness, and (often) improved thermal shock resistance at elevated temperatures. These characteristics are why nonoxide ceramics—particularly silicon carbide—are used so extensively in the development of next-generation aircraft.
Yet there is a major drawback to nonoxide ceramics—they are prone to oxidation during synthesis.
Because nonoxide ceramics have the characteristics of increased refractoriness and improved thermal shock resistance, they require high temperatures (above 1,000°C) for their synthesis. But at these high temperatures, spontaneous oxidation is likely to occur when nonoxide ceramics react with atmospheric oxygen.
To prevent oxidation, nonoxide ceramics are typically synthesized in a vacuum or argon atmosphere to ensure no oxygen disrupts the synthesis. But this synthesis method leads to a new problem—the resulting ceramic is a dense or porous block, which must then be ground and milled into a fine powder for further processing. And because nonoxide ceramics have high strength and stiffness, grinding these ceramics into powder leads to high wear and operating costs.
In short, all the nonoxide ceramic characteristics that make for great advantages in application make for great disadvantages during processing.
Finding ways to lower energy demand and production costs associated with nonoxide ceramic processing is of critical importance. Global air traffic passenger demand continues to increase year after year, meaning the need to develop more efficient aircraft increases as well. Using nonoxide ceramics in aircraft—particularly in gas turbines—is a significant way to minimize fuel consumption and emission by allowing lighter engines to operate at higher temperatures.
So, if aircraft are to incorporate nonoxide ceramic components regularly, we need an energy- and cost-effective method by which to process them.
According to researchers at Forschungszentrum Jülich in Germany, such a method may now be possible—with a slight tweak to a known method (and a little bit of luck).
Molten salt synthesis is a method to produce ceramic powders. In this method, adding a salt (commonly a chloride or sulfate) to reactants acts as a separating agent—the components no longer bond together, and they form a powder rather than a compact solid (thus avoiding the need for energy-intensive milling). Additionally, the salt bath lowers the temperature needed for synthesis, which further cuts energy and production costs.
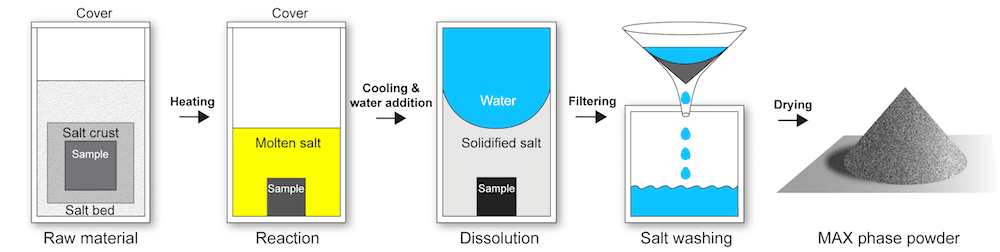
In the molten salt synthesis process developed by Jülich researchers, potassium bromide protects nonoxide ceramics from oxidation during synthesis. The salt is then washed away to reveal ceramic powder. The salt can be recovered and reused. Credit: Apurv Dash, Forschungszentrum Jülich
However, conventional molten salt methods for synthesizing nonoxide ceramics require a protective argon atmosphere to prevent oxidation, increasing both complexity and production costs. What the Jülich researchers discovered, though, was that a particular bromide salt encapsulates materials so well, it can prevent oxidation from taking place!
“Potassium bromide, the salt we use, is special because when pressurized, it becomes completely impermeable at room temperature,” explains Apurv Dash, lead author of the study and doctoral researcher at Forschungszentrum Jülich, in a Jülich press release. “We have now demonstrated that it is sufficient to encapsulate the raw materials tightly enough in a salt pellet to prevent contact with oxygen—even before the melting point of the salt is reached at 735ºC. A protective atmosphere is thus no longer necessary.”
With funding from the German Federal Ministry of Education and Research, the researchers, led by Jesus Gonzalez-Julian, ACerS member and head of the young investigator group “Ceramic Matrix Composites,” tested their method on various nonoxide ceramics and titanium, but they were particularly interested in testing the method on MAX phases.
MAX phases are a large class of layered ternary carbides or nitrides with the formula (Mn+1AXn), where M, A, and X stand for early transition metals, group 13/14 elements, and carbon or nitrogen atoms, respectively. They act as the basis for MXenes, a family of 2D materials we have talked about regularly on CTT.
MAX phases have the positive properties of both ceramics and metals—they are heat-resistant and lightweight, yet less brittle than ceramics, and can be plastically deformed like metals. However, until this point, there have been no suitable methods for producing MAX phases with high purity, which has limited their use in industrial applications.
The researchers found their molten salt process (known as MS3 for “molten salt shielded synthesis/sintering”) lowered synthesis temperature by about 100°C for MAX phases. Additionally, the resulting powders were more pure than powders produced through conventional processing methods.
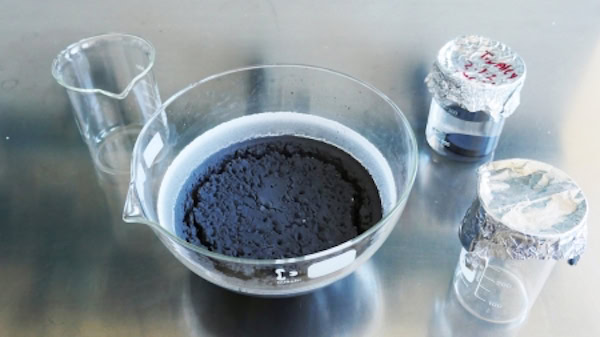
Solidified salt crust after cooling. Credit: Tobias Schlößer, Forschungszentrum Jülich
A bit of luck played into the Jülich researchers discovering the efficacy of potassium bromide in molten salt synthesis. In an email, ACerS member and director of the Institute of Energy and Climate Research–Materials Synthesis and Processing, Olivier Guillon, explains what happened.
“Our furnace with protective atmosphere is typically busy, so instead of waiting for days, [doctoral researcher] Apurv Dash used a normal furnace to save time and to look for alternatives,” Guillon says. “We tried basically two salt systems, NaCl [sodium chloride] and KBr [potassium bromide], because they are cheap and commonly used for molten salt. [Dash] obtained the best results with KBr so all the further experiments were carried out using this system.”
Guillon continues, “It is difficult to eliminate completely the oxidation, because of for example oxygen present at the surface of the raw powders (like titanium particles). We have to learn how to deal with it, for example which amount of oxygen can be tolerated while guaranteeing the targeted properties of the material? The answer of course depends on the material chosen.”
In the future, the Jülich researchers hope to better understand the synthesis mechanisms, in part by trying different salt systems to optimize the process and also synthesizing other nonoxide materials. Additionally, they are aiming to scale up the process and bridge the gap toward commercialization and industry.
The paper, published in Nature Materials, is “Molten salt shielded synthesis of oxidation prone materials in air” (DOI: 10.1038/s41563-019-0328-1)
Of additional interest
Doctoral researcher Apurv Dash presented the Jülich molten salt method at Falling Walls Lab 2018, an international forum that aims to promote exceptional ideas and to connect promising scientists and entrepreneurs from all fields on a global level. See his presentation below!

Credit: Falling Walls Foundation, YouTube
Author
Lisa McDonald
CTT Categories
- Aeronautics & Space
- Manufacturing