[Image above] A freestanding spiral structure made from GE214 quartz tubing printed by previous Missouri S&T student Joseph Drallmeier (currently a Ph.D. student at the University of Michigan). Quinine in tonic water flowing through the open tube fluoresces under UV illumination. Credit: Edward Kinzel, Joseph Drallmeier
Unlike polymer and metal additive manufacturing (AM), there has been significantly less research on glass AM, and current glass AM techniques are far from achieving industrial capacity. However, recent years have seen increasing studies in this field.
In March, I wrote an article reviewing advances in glass AM since 2015, and I followed that article with one in May on two recent glass AM techniques. In today’s third installment, we will discuss another technique for creating 3D-printed glass: fiber-fed laser-heated AM.
Fiber-fed AM: A new type of FFF
Fused filament fabrication (FFF; trademarked term is fused deposition modeling) is an AM technique in which a feedstock filament is fed through a heated extrusion nozzle that melts the filament so it can be deposited in thin layers; as the filaments cool, the next layer is deposited on top.
Two of the big glass AM players in 2015—Israeli startup Micron3DP and the Massachusetts Institute of Technology’s Mediated Matter group/MIT Glass Lab—used FFF methods. Researchers from the Centre d’Optique, Photonique et Laser in Canada also used an FFF technique, and their choice of chalcogenide glass filaments allowed them to print at lower temperatures than other glass FFF methods.
Compared to other AM methods (such as selective laser melting), FFF methods have been more successful in depositing transparent glass. Transparency is a key quality for glass used in optical applications, for example, gradient-index optics and integrated optics. As such, FFF methods appear to be a promising AM method for creating glass for optical applications.
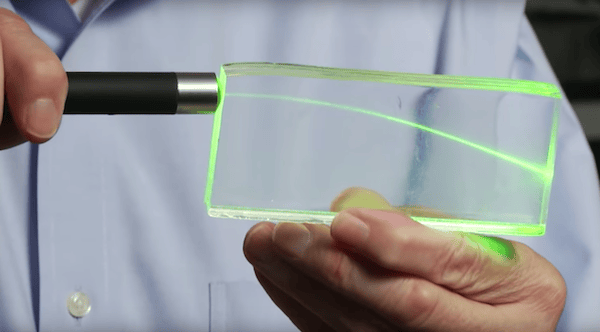
Gradient-index (GRIN) lenses reduce aberrations in imaging applications. Could these lenses one day be created through 3D printing? Credit: University of Rochester, YouTube
Current glass FFF methods, though, face some limitations that hinder their ability to create glass for optical applications. For example, the process described by Luo et al. in Journal of Manufacturing Science and Engineering deposits void-free (bubble-free) transparent glass, but intermittent reloading of the feedstock filament disrupts continuous deposition.
Could an FFF method be developed that allows for continuous deposition of void-free, transparent glass? A couple of recent papers by ACerS member Edward Kinzel and his colleagues explore a new method that could achieve such a feat—fiber-fed laser-heated AM, an FFF method that uses optical fibers as feedstock filament.
Road to fiber-fed AM
Kinzel, associate professor of aerospace and mechanical engineering at the University of Notre Dame, became interested in glass AM in 2012 when he began working at Missouri University of Science and Technology (Missouri S&T). He wanted to print gradient-index optics, and he and his previous Ph.D. student Junjie Luo (now project development engineer at Lancer Corporation) initially experimented with powders and frits but had issues with bubble entrapment.
Kinzel and Luo saw the use of lampwork “stringers” at the Missouri S&T hot-glass shop and began to experiment with hand feeding these thin glass fibers into a laser generated melt pool. “This allowed us to print fully dense transparent glass forms by avoiding the consolidation issues with the powder-bed direct laser melting approach,” Kinzel explains in an email.
Their work with stringers led to further investigation of FFF techniques, which in turn led to numerous collaborations with partners from industry (Clara Rivero-Baleine and Jeff Ruckman, Lockheed Martin; Stephan Belhe and Keith Rosenberg, Schott Glass), government (Jonathon Goldstein and Augustine Urbas, Air Force Research Laboratory; Alex Marchi and John Bernardin, Los Alamos National Laboratory), and academia (Doug Bristow, Robert Landers, and Richard Brow, Missouri S&T).
The ins and outs of fiber-fed AM
During their investigation of FFF techniques, Kinzel and his colleagues were interested in “pushing down the resolution” of their optics (increasing the optics’ ability to image objects on smaller scales). Additionally, Urbas and Goldstein at AFRL expressed an interest in creating optics with light guiding capabilities. These interests led them to develop fiber-fed AM.
Fiber-fed laser-heated AM uses optical fiber as a feedstock in FFF. Optical fibers are widely available, relatively cheap sources of high-quality, low-loss glass that comes in spools kilometers long, allowing continuous, uninterrupted deposition. Additionally, optical fiber’s inherent core-cladding design allows light to be guided down the length of the material, which is the basis for many communication and sensing technologies.
John Hostetler, Kinzel’s previous master’s student and now project engineer at Johnson Space Center, did a lot of experiments to determine appropriate process parameters for 3D printing optical fibers. The results of these experiments are published in conference proceedings from the 2018 Annual International Solid Freeform Fabrication (SFF) Symposium.
While the SFF Symposium conference proceedings focused on demonstrating the ability to use a fiber-fed AM technique, conference proceedings from this year’s Society of Photo-Optical Instrumentation Engineers (SPIE) Photonics West conference dug deeper into exploring whether core-cladding integrity is preserved during the process. The researchers concluded that the laser-heating process does not significantly affect the core-cladding boundary, due in large part to the fact that heating of the optical fiber can take place in free-space (without supports).
Depositing freestanding fiber. Credit: Video by John Hostetler, courtesy of Edward Kinzel
Kinzel sees the fact that fiber-fed AM can take place in free-space as an improvement to the MIT and Micron3DP methods from 2015. “The approaches that MIT (gravity fed orifice) or Micron3DP (fused filament fabrication) developed both require physically contacting the glass when it’s very hot. This limits the ability to use higher working temperature glasses such as fused silica. This also significantly complicates printing fully dense forms out of glass,” Kinzel explains. “In the filament [fiber] fed process we can still push the molten region with the filament as well as heating the glass locally to the point that it can reflow and form solid forms without seams.”
However, Kinzel does not see fiber-fed AM as the only promising method for 3D printing glass for optical applications. He points to work by Rebecca Dylla-Spears’ team at Lawrence Livermore National Laboratory on direct ink writing and by Bastian Rapp and colleagues at the University of Freiburg on stereolithography as examples. However, “I think for larger light guiding structures, the filament fed technique has some significant advantages. This extends to repairing optics.”
The future of fiber-fed AM
Kinzel recently moved to the University of Notre Dame, but is continuing the collaboration with materials partner Richard Brow and controls partners Doug Bristow and Robert Landers (all from Missouri S&T) to improve the fiber-fed technique. Specifically, they are improving the accuracy for functional optical forms through force and optical feedback control and developing glasses for printing.
Additionally, Kinzel and colleagues are also printing full 3D integrated optoelectrofluidic devices, planning to add more subtractive glass processing into the new setup, and improving their ability to locally dope glass during processing. Also, “We’d like to expand some initial work we did a couple years ago with Dr. Brow on printing bio-glass structures,” Kinzel adds.
St. Louis Gateway Arch. Credit: Video by John Hostetler, courtesy of Edward Kinzel
The conference proceedings from the 2018 Annual International SFF Symposium are “Fiber-fed printing of free-form free-standing glass structures.”
The conference proceedings from 2019 SPIE Photonics West are “Direct write of photonics using a filament-fed laser-heated process” (DOI: 10.1117/12.2510345).
Update 06/11/2019 – Video captions updated to state John Hostetler recorded the videos
Author
Lisa McDonald
CTT Categories
- Glass
- Material Innovations
- Optics