Credit: yat fai ooi; Flickr CC BY-NC 2.0
Battery research is rich. Every day it seems there is a new material that promises to extend battery life and performance.
Many of these studies zero in on graphene or silicon as the go-to materials to make high-capacity electrodes for rechargeable batteries. But so many of these advances never make it beyond the lab—why?
“A large majority of these results come from experiments performed on small geometry or thin electrodes prepared under special conditions with low mass loading of silicon,” explains Gurpreet Singh, associate professor of mechanical and nuclear engineering at Kansas State University (Manhattan, Kansas). “Not surprisingly, efforts to incorporate these materials into practical batteries that require large-area electrodes have been unsuccessful because of challenges that arise at high mass loadings—namely low capacity per volume, poor cycling efficiency, and chemical–mechanical instability.”
Singh and his research team are exploring new material combinations and electrode designs that will afford batteries with high capacity, efficiency, and stability as well as high mass loading. The researchers report their latest findings in a new article in Nature Communications.
“We have manufactured a ‘self-supporting’ and ‘ready-to-go’ electrode that consists of a glassy ceramic—silicon oxycarbide sandwiched between large platelets of chemically modified graphene,” Singh says. “The electrode has high capacity—about 600 mA–h/g or 400 mA–h/cm3. Silicon oxycarbide particles give the electrode its capacity, and ~20% chemically modified graphene platelet content gives the electrode a paper-like design.”
Because most current battery electrodes incorporate a metal foil support and polymeric glue—which do not contribute to battery capacity—eliminating those components with the new paper-like electrode saves ~10% of the battery cell’s weight, Singh says.
“The result is a lightweight electrode capable of storing lithium-ions and electrons with near-100% cycling efficiency for more than 1,000 charge–discharge cycles. But the most important aspect is that the material is able to demonstrate such performance at practical mass loadings.”
An added bonus to the new paper-like battery electrode is that it affords batteries with superior performance even at low temperatures. According to Singh, the team’s cell has a capacity of 200 mA–h/g even after storage at −15°C for more than a month, “which is quite remarkable considering that most batteries fail to perform at such low temperatures,” he says.
The material the researchers used for these novel electrodes is quite special itself. Silicon oxycarbide is prepared from a liquid resin that is a byproduct of the silicone industry, so the raw materials are low-cost. Plus, silicon oxycarbide is somewhat established as a material—it has been previously studied for its high-temperature oxidation resistance and applications in thermal and environmental barrier coatings and ceramic matrix composites.
To make the silicon oxycarbide electrodes, the researchers heat the liquid resin until it decomposes and transforms into sharp glass-like particles. “The constituent silicon, carbon, and oxygen atoms get rearranged into a random 3-D structure, and any excess carbon precipitates out into cellular regions,” Singh says. “Such an open 3-D structure renders large sites for reversible lithium storage and smooth channels for lithium-ion transportation.”
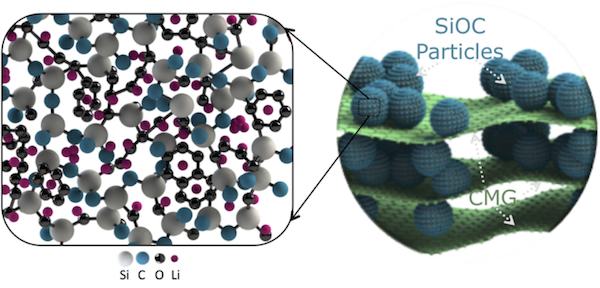
Structure of the composite paper electrode, with silicon oxycarbide (SiOC) embedded in chemical modified graphene (CMG) sheets. Zoomed-in schematic (left) shows amorphous nanodomain structure of SiOC. Microvoids, silicon and carbon dangling bonds, and disordered carbon phase are preferred sites for reversible Li+ adsorption. Credit: Gurpreet Singh, Kansas State University
In comparison, crystalline silicon electrodes in other lithium batteries are fabricated via an alloying reaction with lithium that can result in a 300%–400% volume change within the material.
The team thinks that its novel paperlike electrodes—with their optimal operation at low temperatures, light weight, and superb performance—might eventually be used to power drones flying at high altitudes and potentially even in space applications.
But akin to previous studies of new battery materials, “there are challenges that must be addressed from a practicality point of view,” Singh says. “We need to produce this electrode material at even larger dimensions—present day pencil cell batteries uses graphite-coated copper foil electrodes, which are more than one foot in length.”
“In addition, we would like to perform mechanical bending tests to see how bending affects performance parameters,” Singh continues. “Ultimately, we aim to work with industry to explore production of full-cell Li-ion batteries. Silicon oxycarbide can also be prepared by 3-D printing, so that’s another potential future direction.”
The open-access paper, published in Nature Communications, is “Silicon oxycarbide glass-graphene composite paper electrode for long-cycle lithium-ion batteries” (DOI: 10.1038/ncomms10998).
The National Science Foundation funded this research— NSF-CBET supported the project on polymer-derived ceramics and a NSF-CMMI-CAREER grant supported the project on graphene electrodes.
Author
April Gocha
CTT Categories
- Electronics
- Energy
- Glass
- Manufacturing
- Material Innovations