[Image above] Current common thermal insulation materials, such as the fiberglass being installed above, have relatively high thermal conductivities and so require thick layers to achieve effective insulation. Next-generation insulation systems based on hollow silica particles could lower material costs and space requirements. Credit: Erik Mclean, Unsplash
With extreme cold expected to become more likely during winter in the Northern hemisphere, improved insulation is a must for buildings in these areas.
Current common thermal insulation materials, such as fiberglass, mineral wool, and polystyrene, have relatively high thermal conductivities (0.030–0.040 W m−1 K−1) and so require thick layers to achieve effective insulation. Such layering results in high material, transportation, and disposal costs as well as takes up significant space within building equipment and envelopes.
Aerogels are state-of-the-art insulation materials with very low thermal conductivities (0.012–0.020 W m−1 K−1). They limit heat conduction by confining air in voids created by the highly porous nanostructure. However, their high cost, fragility, and lack of scalability hinder commercial use.
In the past decade, hollow silica particles started garnering attention as a new type of insulation material. Like aerogels, the voids in hollow silica interrupt heat transport pathways in both the solid and gas phases, giving these materials fairly low thermal conductivities (0.02–0.03 W m−1 K−1). However, unlike aerogels, hollow silica particles can be easily synthesized by several low-cost strategies.
Hollow silica particles alone can be a health hazard, so researchers are pursuing the combination of these particles with other materials to mitigate the risk of exposure as well as make it easier to transport.
Numerous studies explored mixing hollow silica particles with polymers. However, because matrix polymers have high thermal conductivities (∼0.15–0.30 W m−1 K−1), the insulating ability of the composite was compromised.
Instead, researchers now are exploring the combination of hollow silica particles with other insulating materials. Two recent studies illustrate work in this area.
The first open-access study, by researchers at Oak Ridge National Laboratory, freeze-dried a mixture of hollow silica particles with cellulose fibers and carbon black to create a highly hydrophobic but structurally stable composite.
The thermal conductivity of the composite was ∼0.025 ± 0.003 W m−1 K−1, which was lower than both the cellulose fibers (0.05 W m−1 K−1) and hollow silica particles (0.028 ± 0.002 W m−1 K−1) alone.
This finding was surprising because “In all other composites reported to date, the thermal conductivity of the composite is always higher than the thermal conductivity of [hollow silica particles],” the researchers write.
They suggest that the heterogenous interfaces within the composite—i.e., interfaces between the hollow silica particles, cellulose fibers, and carbon black—play a role in lowering the heat transfer.
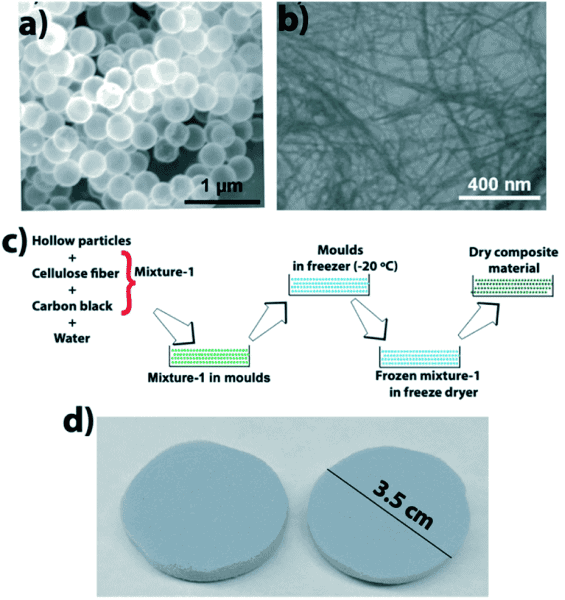
(a) SEM image of hollow silica particles, (b) SEM image of cellulose fibers, (c) schematic showing the composite fabrication, and (d) photo of the composite material. Credit: Sharma et al., RSC Advances (CC BY 3.0)
The open-access paper, published in RSC Advances, is “A lightweight thermally insulating and moisture-stable composite made of hollow silica particles” (DOI: 10.1039/D2RA01561G).
The second study, by researchers at University at Buffalo and Lawrence Berkeley National Laboratory, employed high-shear mechanical mixing to fabricate hollow silica–fiberglass composites.
The hollow silica particles were created via two low-cost synthesis routes. The gas-phase synthesis method generated hollow shells by a droplet surface precipitation mechanism in a flame aerosol reactor. The liquid-phase synthesis method formed hollow shells by removal of a carbon template, which was produced by hydrothermal reaction of glucose.
The composite with the lowest thermal conductivity (0.023 W m-1 K-1) contained 60 wt.% of gas-phase SiO2. Composites containing liquid-phase SiO2 obtained their lowest thermal conductivity (0.026 W m-1 K-1) at 50 wt.%. Both gas-phase and liquid-phase SiO2 composites provided better thermal insulation performance than composites created using commercial silica gel (0.033 W m-1 K-1).
In addition to low thermal conductivity, the hollow silica–fiberglass composites demonstrated robust mechanical flexibility. Specifically, the Young’s moduli of the gas-phase SiO2, liquid-phase SiO2, and commercial-SiO2 composites were 35 kPa, 30 kPa, and 15 kPa, respectively.
These findings “suggest that the approach described here is a promising method for scalable and low-cost production of high-performance thermal insulation materials,” the researchers conclude.
The paper, published in Chemical Engineering Journal, is “Creation of hollow silica–fiberglass soft ceramics for thermal insulation” (DOI: 10.1016/j.cej.2022.140134).
Author
Lisa McDonald
CTT Categories
- Construction
- Material Innovations
- Thermal management