[Image above] Thermal energy storage tower inaugurated in 2017 in Bozen-Bolzano, South Tyrol, Italy. Designing materials that can contain the high-temperature and corrosive materials integral to thermal energy storage is an ongoing area of research. Credit: Bartleby08, Wikimedia (CC BY-SA 4.0)
This past summer was yet again among the hottest on record. As I write this, millions of acres of the Pacific coast of the United States are burning, as has happened for the last few years. It is clear we must reduce the rate we are emitting carbon dioxide into the atmosphere.
Two substantial answers to reducing emissions—energy harvesting from solar and wind—are maturing nicely, with over 627 gigawatts (GW) of installed solar photovoltaic and 650 GW of installed wind electricity generation capacity. Led by hydroelectric generation, renewable energy harvesting accounts for about 33% of global capacity (ability to generate) and 25% of energy actually generated.
You’ll note the difference between capacity and amount generated. This difference arises because the sun does not shine at night and the wind does not always move fast enough. To overcome periods of low generation, energy storage technologies are critical to meeting electricity needs during these times.
Perhaps the oldest storage technology is elevating water with reversible pump/generator systems (pumped hydro). But this method is limited to locations with large amounts of available water and land for building substantial reservoirs. As such, the world needs more and better energy storage technologies.
For an excellent overview of current energy storage technologies, see this fact sheet by the nonprofit Environmental and Energy Study Institute. One key factor to all these technologies is energy density, or the amount of energy stored in a given volume. Pumped hydro, for example, has very low energy density. Lithium-ion batteries are up to 2,000 times more energy dense than pumped hydro. We have reported on ceramics for battery applications many times, including here and here.
Another technology with similar characteristics to Li-ion batteries is molten salt for thermal energy storage. The challenges with molten salts—and other closely related materials—for thermal storage include the highly corrosive nature of the liquid materials, moderately high operating temperatures, and substantial expansion during the transition from solid to liquid.
Producing container materials that can withstand the high temperatures, thermal expansion stresses, and corrosive materials for decades of operation are key to adoption of large-scale thermal energy storage. And in the recent September/October 2020 issue of the International Journal of Applied Ceramic Technology, two articles from different research groups in Germany explore creating carbon/carbon-silicon carbide (C/C-SiC) ceramic matrix composites (CMCs) for use as container materials. (These CMCs are known for being inert and easily fabricated.)
In the open-access article “C/C-SiC component for metallic phase change materials,” researchers from the German Aerospace Research Center (DLR) and the University of Augsburg in Germany describe the design, fabrication, and characterization of a C/C-SiC container for an aluminum-silicon phase change alloy.
The first stages of their study focused on fabrication and compatibility testing of C/C-SiC test bars. They found the bars withstood the liquid aluminum-silicon alloy and maintained their physical properties with no discernable interactions, such as penetration of the alloy into the test bars. Though there are potential chemical reactions between the alloy and the CMC, the authors found no evidence of substantial reactions, which echoes the findings of other researchers.
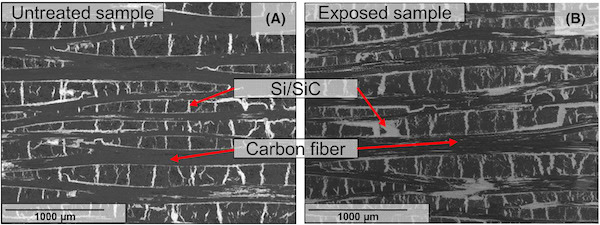
SEM images of C/C-SiC samples. (A) Without exposure, and (B) after exposure. Credit: Stahl et al., International Journal of Applied Ceramic Technology
Following the test bars, the authors continued with the design and fabrication of the container. They decided on low-cost, scalable techniques for fabricating the four main components of their annular container and then used these techniques as boundary conditions for finite element analysis. They used finite element analysis to determine container wall thickness by balancing the strength needed to withstand stresses that arise during phase changes against heat conduction requirements to allow efficient energy transfer.
Unfortunately, pressure testing of the container revealed cracks at the interface of two of the parts, which most likely occurred during fabrication. Though the flaw prevented the full regimen of performance testing, and several issues require further experimentation, the researchers believe the container shows promise for thermal energy storage application.
The second article in this same issue of ACT, “Properties of C/C-SiC composites produced via transfer moulding and inner siliconization,” describes a different path to low-cost fabrication of C/C-SiC composites.
The authors, from Chemnitz University of Technology in Germany, prepared C/C-SiC using carbon fiber reinforced polymers as the starting material. The moldable precursor polymers are shaped and cross-linked, then pyrolyzed to C/C composites under argon atmosphere. Conversion to C/C-SiC is achieved by either liquid silicon infiltration or internal siliconization, the latter of which is accomplished by mixing silicon powder into the original polymer.
The authors explore the effects of carbon fiber fraction (weight %), silicon fraction, and silicon loading method. They measured processing parameters of mass loss, shrinkage, and porosity, and performance parameters of strength and elongation. The results are complex, and I would not do them justice by attempting to summarize them here. However, in short, the researchers concluded that the best mechanical properties were found to be at a fiber mass content of 40%, and a silicon amount higher than 14 wt% negatively influences the whole process.
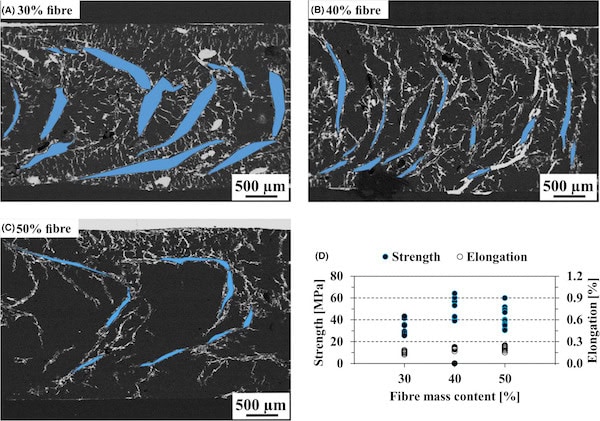
(A‐C) SEM from the longitudinal sections of C/C-SiC showing the defects and the infiltration structure as a function of the fiber mass content. (D) Mechanical properties of C/C‐SiC composites (blue: delamination at the flow lines; white: infiltrated silicon; black: carbon matrix + fiber). Credit: Ahmad et al., International Journal of Applied Ceramic Technology
Of all the performance parameters they analyzed, the one that intrigued me most was the trade-offs between using either internal siliconization or liquid silicon infiltration to achieve SiC conversion.
On first take, internal siliconization should be substantially less complicated (and less expensive) than liquid silicon infiltration because it only requires mixing silicon powder into the original polymer. But adding silicon powder to the uncured polymer raises the viscosity, which can negatively affect the molding process.
Internal siliconization appears to result in samples of similar strength to infiltrated samples. However, open porosity is higher with internal siliconization that with infiltrated samples. (Higher porosity leads to reduced mechanical properties, with a potential for leakage of liquid contents should pores lead to holes through the thickness of container walls.) It was interesting that post processing of internal siliconized sample by infiltration did not improve porosity.
Their results show that molding C/C-SiC composites from preceramic polymer-based mixtures has the potential to be a cost-effective method for fabrication of complex structures. Further research to optimize properties and processing parameters should improve the end-product performance and allow this method to compete with the more conventional fabrication methods, such as those employed by Stahl et al. in the first open-access paper.
The first open-access paper, published in International Journal of Applied Ceramic Technology, is “C/C-SiC component for metallic phase change materials” (DOI: 10.1111/ijac.13570).
The second paper, published in International Journal of Applied Ceramic Technology, is “Properties of C/C-SiC composites produced via transfer moulding and inner siliconization” (DOI: 10.1111/ijac.13548).
Author
Jonathon Foreman
CTT Categories
- Energy
- Thermal management