[Image above] A chunk of white phosphorus in water. White phosphorus is very reactive and will spontaneously combust if stored in air. Credit: W. Oelen, Wikimedia (CC BY-SA 3.0)
From fertilizers and flame retardants to food additives and electronics, many of today’s commodity chemicals trace their existence back to white phosphorus.
White phosphorus, or tetraphosphorus, is a synthetic form of phosphorus consisting of four phosphorus atoms. It is produced by breaking phosphate-containing rocks down into the elementary form, which is then converted into phosphoric acid or other phosphorus compounds (a small amount is used directly as a reactant).
This roundabout reduction–reoxidation sequence to create phosphorus-based products is necessary to overcome the incredible stability of the phosphorus–oxygen bond in natural phosphate. This strong bond hinders the direct conversion of phosphate-containing rocks into valuable phosphites or phosphonates.
However, the conventional carbothermal reduction process for producing white phosphorus has a high carbon footprint. This process involves heating carbon coke and phosphate up to 1,500°C in an arc furnace to break the strong phosphorus–oxygen bonds. The reaction generates carbon dioxide as a major byproduct. It also produces a calcium metasilicate slag because the coke does not completely oxidize, which wastes about 30% of the energy input.
With the recent focus on reducing industrial carbon emissions, researchers are investigating new ways to make white phosphorus.
Molten salt electrochemical synthesis is one option being explored to lower carbon emissions. In this relatively low-temperature process, molten salts serve as the solvent and facilitate an enhanced reaction rate by increasing the mobility of reactants and the contact area between them.
Molten salt synthesis is already being explored as a way to improve the sustainability and cost effectiveness of nanomaterial production, including by recycling carbon dioxide into new products.
Regarding its use for phosphorus production, molten salt synthesis addresses several obstacles in the phosphate reduction reaction. Specifically, conducting the reaction in molten salts prevents parasitic hydrogen evolution, as well as inhibits the formation of electrically insulating red phosphorus deposits.
This February, researchers at the Massachusetts Institute of Technology published an open-access paper detailing their development of a molten salt synthesis process for white phosphorus production.
Their process uses a dehydrated form of phosphoric acid, which contains long chains of phosphate salts held together by bonds called phosphoryl anhydrides. The phosphoryl anhydride bonds dramatically lower the fusion temperature of the salt melts, from 1,583°C for sodium orthophosphate (Na3PO4) to only 628°C for sodium metaphosphate, ([NaPO3]n).
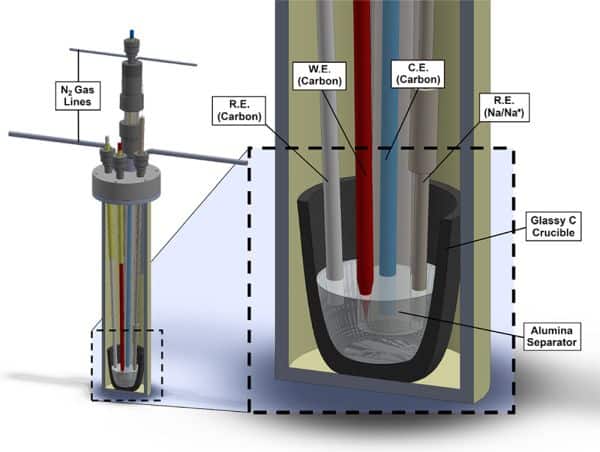
Cutaway schematic of the MIT researchers’ molten salt electrochemical cell. The system features separated anodic and cathodic chambers with independent nitrogen flow streams, a Na/Na+ electrode for use as a fixed-potential reference, and a cold trap for product characterization and quantification. W.E. = working electrode; R.E. = reference electrode; C.E. = counter electrode. Graphite rods are used for all electrodes. Credit: Melville et al., ACS Central Science (CC BY 4.0)
Experiments on this molten salt system demonstrated its ability to achieve highly efficient and sustained production of white phosphorus. Specifically, they recorded a 95% Faradaic efficiency, which indicates the amount of collected product relative to the amount produced from the total charge transferred.
Other advantages of the system include
- Reduction in carbon emissions. The system reduced the overall carbon footprint of the synthesis process by about 50% compared to the conventional approach. The researchers hope to bring carbon emissions down to almost zero in the future by using renewable energy to provide the required electricity.
- Potential for on-site production. The researchers predict that if they can scale up the process, it would allow industrial users to generate white phosphorus on site instead of having it shipped to them, which would cut down on the risks of transporting this explosive material.
To do this study, the researchers had to develop new tools for controlling and measuring the electrolytes in the system. They plan to use these new tools to develop lower-carbon processes for isolating other industrially important elements, such as silicon and iron.
“This work falls within our broader interests in decarbonizing these legacy industrial processes that have a huge carbon footprint,” says senior author Yogesh Surendranath, associate professor of chemistry and chemical engineering at MIT, in an MIT press release. “The basic science that leads us there is understanding how you can tailor the electrolytes to foster these processes.”
The open-access paper, published in ACS Central Science, is “Electrolytic synthesis of white phosphorus is promoted in oxide-deficient molten salts” (DOI: 10.1021/acscentsci.2c01336).
Author
Laurel Sheppard
CTT Categories
- Environment