[Image above] Mixing units run in the Rare Earth Extraction Facility at the WVU Energy Institute/National Research Center for Coal and Energy. Credit: West Virginia University
Coal might play a part in lessening our dependence on rare earth elements (REEs).
While coal gets a bad rap because it’s not a clean energy source like solar or wind, there has been some progress toward finding other uses for it.
In fact, last year the U.S. Department of Energy’s National Energy Technology Lab (NETL) found high concentrations of rare earth elements in coal basins in various parts of the United States. And the DOE is also funding a project to convert coal fly ash into rare-earth oxides.
Now, researchers at West Virginia University, with the help of a $3.38 million two-phase project from NETL, have opened the Rare Earth Extraction Facility to extract rare earth materials from acid mine drainage. Acid mine drainage is the water pollution that results from coal mining activities. And it can be highly toxic to the environment.
The new facility is the second phase of the NETL-funded project to develop a process to separate REEs from coal mining by-products. “Acid mine drainage from abandoned mines is the biggest industrial pollution source in Appalachian streams, and it turns out that these huge volumes of waste are essentially pre-processed and serve as good rare earth feedstock,” director of the West Virginia Water Research Institute Paul Ziemkiewicz says in a WVU news release. “Coal contains all of the rare earth elements, but it has a substantial amount of the heavy rare earths that are particularly valuable.”
The extraction method involves acid leaching and solvent extraction, which involves dissolving drainage sludge in acid and then emulsifying it to pull rare earths from the water. Then the emulsion goes through a mixing process that “strips the rare earths out as a concentrated solution and precipitates the rare earths as a solid,” that can be further refined to usable rare earth metal, according to the release.
Anything left over that is unusable, which would be minimal, ends up in the acid mine drainage treatment plant’s disposal system.
Director of the WVU Energy Institute Brian Anderson uses the example of scandium to illustrate the amount of money the extracted rare earths could generate. “…Scandium, one of these rare earths, is worth about $4,500 per kilogram as an oxide, the form that it will leave this facility,” he states. “After refining, it would be worth $15,000 per kilogram.”
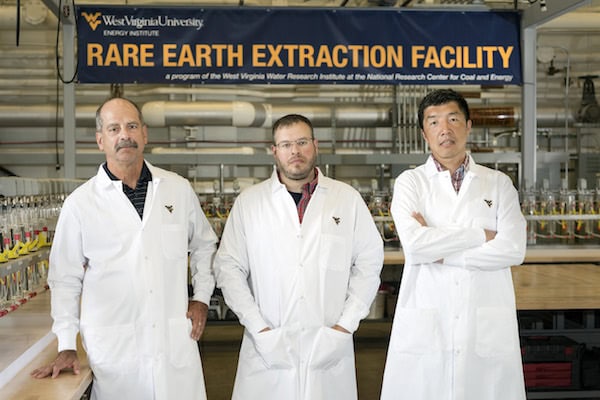
Members of the WVU rare-earth research team from L to R: Paul Ziemkiewicz, director of the West Virginia Water Research Institute; Chris Vass, facility operator; and Xingbo Liu, professor and associate chair of research, Statler College of Engineering and Mineral Resources, in the new Rare Earth Extraction Facility at the WVU Energy Institute/National Research Center for Coal and Energy. Credit: West Virginia University
Two years ago, West Virginia was the largest coal producer east of the Mississippi River, according to the U.S. Energy Information Administration. But demand for coal has decreased, and coal production has declined considerably in the past decade. The Rare Earth Extraction Facility could boost the state’s economy, creating jobs and generating revenue.
“Currently, acid-mine-drainage treatment is a liability, an environmental obligation,” Ziemkiewicz adds. “But it could turn into a revenue stream, incentivizing treatment and creating economic opportunity for the region.” According to the press release, the economic potential is large: The Appalachian region could produce 800 tons of rare earths annually—enough to supply the defense industry for a year.
One man’s trash is another man’s treasure, the saying goes. Or in this case, one coal mine’s waste is a researcher’s rare-earth mineral mine.
For more information about the new Rare Earth Extraction Facility visit the DOE’s website at this link or the NETL’s website at this link.
Did you find this article interesting? Subscribe to the Ceramic Tech Today newsletter to continue to read more articles about the latest news in the ceramic and glass industry! Visit this link to get started.
Author
Faye Oney
CTT Categories
- Basic Science
- Environment
- Market Insights
- Material Innovations
- Weekly Column: “Other materials”