[Image above] Glazed stoneware mugs fired using a microwave furnace instead of a traditional gas-fired tunnel kiln. Credit: Santos et al., International Journal of Applied Ceramic Technology
Another Earth Day has come and gone. There are good reasons for both pessimism and optimism on whether and how we can slow or reverse the changes to Earth’s climate and the environment. The problems seem insurmountable, yet attitudes are changing and actions are following. A key component to accelerating actions that benefit the environment is demonstration of economic benefits.
Academic and industrial ceramic researchers alike recognize these realities, as evidenced by the many articles published in International Journal of Applied Ceramic Technology, notably in the two issues and collections highlighting the circular economy, found here and here. These articles describe efforts to minimize the amounts of virgin raw materials and natural gas in the manufacturing process. Researchers are exploring the use of recycled and waste materials as input streams, along with reducing firing temperatures and employing alternate technologies to natural gas kilns.
In this post, I wish to walk you through the activities on these topics and the resulting ecological and economic benefits through a series of recently published articles. This journey should give you insight into the magnitude of the problems, some proposed solutions, and the potential cost savings that go along with reduced use of raw materials and greenhouse gas production.
Let’s start with the article “Phase composition, microstructure, and properties of ceramic tile prepared using ceramic polishing waste as raw material,” written by several researchers at the Jingdezhen Ceramic Institute in China. The authors indicate ceramic polishing in China creates 70 million tons of waste materials. The ceramics in the waste stream, particularly those from colorfully glazed products, often contain heavy metals that are, of course, bad for the environment. The authors contend that if all porcelain manufacturing in China used the polishing waste as an input stream, none of those 70 million tons would go to landfills.
The polishing waste also contains silicon carbide, which is used as the polishing abrasive compound. As discussed in a previous CTT, silicon carbide reacts with oxygen at high temperatures. The resulting carbon dioxide gas creates porosity, which could be beneficial (e.g., for foamed filters) or detrimental, as is the case for the porcelains targeted in this article. An interesting outcome of the research is materials that can be formed over the wide range of compositions and processing conditions tested.
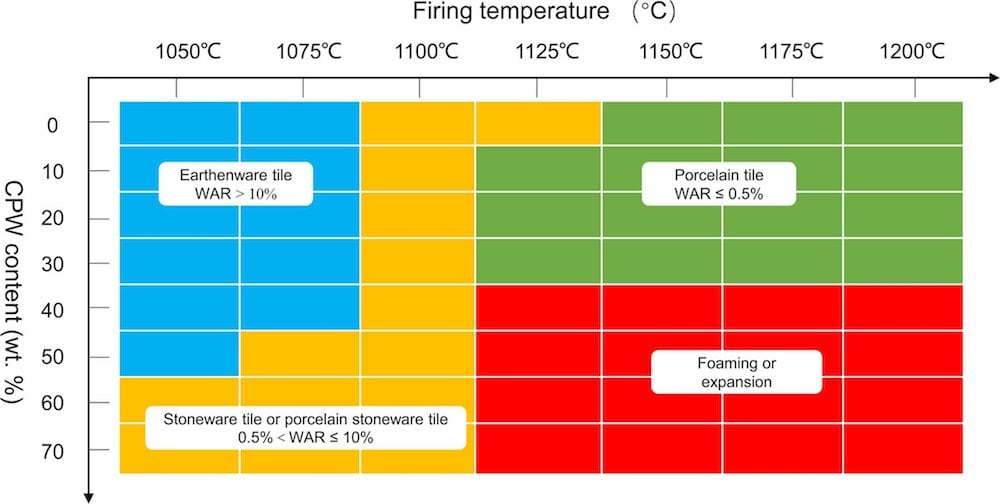
Possible products prepared with different ceramic polishing waste (CPW) contents. WAR = water absorption rate. Credit: Wang et al., International Journal of Applied Ceramic Technology
While this first article demonstrates potential ecological benefits, the article “Economy analysis of the implementation of extruded tiles fabrication in a ceramic industry containing ornamental rock waste,” led by researchers at the State University of the Northern Rio de Janeiro in Brazil, also demonstrates economic motivation for and feasibility of green production methods.
The authors of this study sought to develop a high-value product using the materials available in Brazil. Usually, the country’s raw clays are used to fabricate bricks and blocks, which are low-value commodity items. If the clays were used to fabricate decorative tiles instead, this product offers potential to increase profitability compared to other high-value clay-based products because tiles can be manufactured using the existing local infrastructure.
The quality of the local clays, with high plasticity, hindered the extrusion process. The authors used ornamental rock waste as additives that enabled extrusion. Ornamental rock waste has minimal commercial value, though it is promoted as a potential soil mineralizer.
In addition to the applied science for developing the tiles, the authors provide a thorough analysis of the product cost, sales, and profits over the product lifecycle. The most pertinent item for this post is the relative costs of the raw materials and the fuel used (wood in this case) to manufacture the tiles. For every Real (the currency of Brazil) spent on raw materials, 0.73 Real is spent on fuel. This ratio may not hold true for every location or fuel type, but it does provide a snapshot of the economic impact of fuel in ceramics manufacturing.
Reducing fuel costs through reducing firing temperature or applying advanced techniques is a very hot topic in ceramics research. In the article “Global insight into microwave stoneware firing: Macro and microstructural changes,” researchers led by the University of Aveiro in Portugal compare drinking mugs produced in electric and microwave furnaces to those manufactured using a gas-fired tunnel kiln.
Electric energy has the potential to become carbon-free when produced by energy harvesting (solar, wind, hydroelectric) or nuclear reaction. The authors demonstrate the ability to use microwave furnaces to produce stoneware products with quality (e.g., strength, color) similar to the gas-fired products at temperatures at least 50°C lower than those used in the gas kiln.
“Environmental impact estimation of ceramic lightweight aggregates production starting from residues” is possibly the most earth-friendly paper in this grouping. The authors, who come from the University of Modena and Reggio Emilia (Italy) and the University of Jaen (Spain), describe their efforts to reuse industrial waste to create ceramic products destined for environmentally friendly urban development—a win-win-win.
Lightweight aggregates are expanded (highly porous) clay-based products. Referring to the products chart given earlier, these products fall in the lower right-hand quadrant. In this study, the authors used clays from different regions. The authors compared raw clays to clays with brewery sludge added, along with clays with sludge and bone meal ash (meat processing waste) in raw or vitrified forms. Besides the key performance metrics, the authors estimated the total carbon footprint for the different recipes.
All the samples were fired at 1,000°C, which quite favorably compares to 1,300°C firing temperature of similar commercially prepared materials. The brewery sludge improves the carbon footprint because its heating value replaces some of the natural gas. The energy needed to vitrify the bone ash has a substantial negative effect. The optimal recipe results in a 20% reduction in carbon footprint compared to the clays alone.
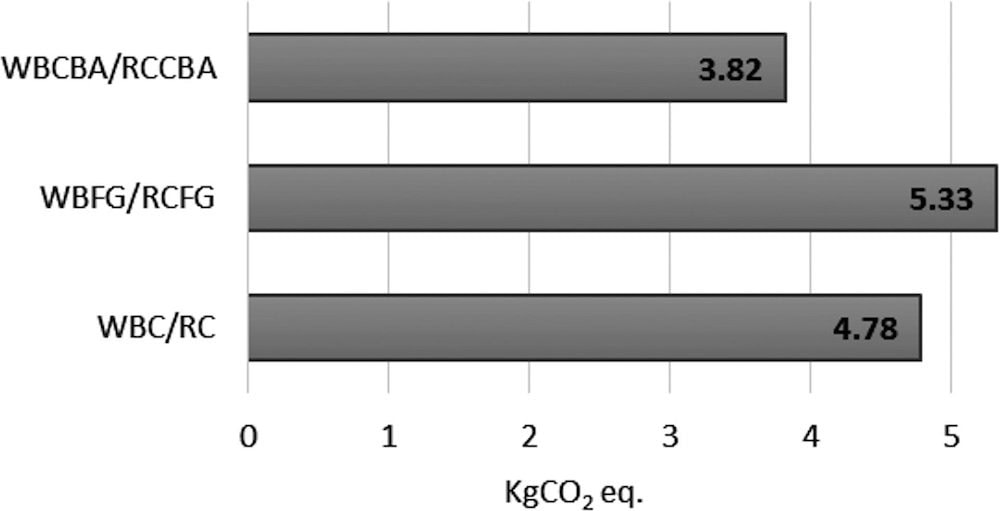
Carbon footprint estimations for lightweight aggregates (using IPCC 2013 GWP 20y methodology). WBC/RC are the base clays, WBCFG/RCFG have sludge and vitrified bone ash, and WBCCBA/RCCBA contain sludge and raw bone ash. Credit: Barbieri et al., International Journal of Applied Ceramic Technology
The article “An environmentally friendly process for preparing commercial ceramic foam composites based on frit/glass wastes” by two researchers at the Seranit Granite Ceramic Factory in Turkey wraps up our series by providing the linkage of the environmental benefits and the financial benefits. Their goal was the preparation of lightweight glass-ceramic building materials that are lighter than natural stone or concrete, which has a very high carbon footprint, yet retain mechanical and chemical stabilities necessary for flooring applications. The high costs of virgin raw materials along with high transportation costs led the authors to research using locally supplied waste materials.
Along with the materials cost savings, the authors found that the optimal combination of materials could reduce the product’s firing temperature by 250°C. They estimated reducing the monthly natural gas expense for their production processes by 37%, which amounts to 235,000 euros per month.
These articles demonstrate that being green is not only good for the environment but also for the bottom line.
Author
Jonathon Foreman
CTT Categories
- Environment