[Image above] Plastic straws cannot be recycled to make new straws—but there are other ways to reuse them. Credit: Chemist 4 U, Flickr (CC BY 2.0)
When it comes to plastic waste, drinking straws often are used as a prime example. They account for only a tiny fraction of the waste in oceans—less than 1% by weight—but they are essentially unnecessary disposable goods for the majority of people, which makes them an easy target for plastic bans.
Unfortunately, unlike glass, plastic straws cannot be recycled to make the same product because of the method used to create them—extrusion molding.
Extrusion molding is a widely used manufacturing process for polymeric materials. In this method, molten plastic is forced through a shaped orifice to form a tube-like or rod-like continuous piece.
Though this method works well for creating new objects, it can be hard on the plastic.
“The exposure of polymers to an oxidative atmosphere at high temperature and shear rate levels introduces chemically aggressive species (such as free-radicals and carboxylic side groups) that reduces their average molecular length and mass,” researchers write in a recent paper.
After a polymer goes through the process two or three times, recycled polymers start exhibiting loss of many key properties, including rigidity, tensile and impact strength, and transparency. The loss of performance is especially apparent for plastic drinking straws, which typically are made of isotactic polypropylene (PP) or high-density polyethylene (HDPE).
“The polymer grades used to produce [straws] have a narrow distribution of molecular mass so they can present high elasticity in the molten state,” the researchers write. “When these straws are recycled, the high average molecular mass is reduced, and the polymers are no longer suitable for blow extrusion of thin films.”
However, just because used straws cannot be recycled to make new ones does not mean they are nonrecyclable—it just means they need to be reused in a different way. An alternative use for recycled straws is exactly what the researchers in the recent paper propose.
Rafael Salomão (lecturer and researcher, University of São Paulo) and Victor Pandolfelli (professor, Federal University of São Carlos) looked at turning straws into anti-spalling fibers for refractory castables.
Like high-quality concrete, refractory castables are susceptible to spalling, a physical process in which surface layers of materials crumble into small pebble-like pieces in response to high temperatures and/or mechanical pressures. The pressure typically comes from water vapor trapped in the highly packed and low porosity structure of the material. When the material is heated, the water vapor cannot escape, so mechanical pressure builds and ultimately causes the material to spall.
To reduce the likelihood of explosive spalling, a common practice in industry is adding fibers to refractory castables. This method works because the fibers dissolve or melt during initial heating of the cast part, increasing the castable’s permeability and thus making it easier for water vapor to escape.
The most common fibers used in this technique are thermoplastic polymer-based fibers, such as PP. Ideally, polymeric fibers that are easily degradable with low melting points suit this purpose best because the sooner the fibers melt, the sooner water vapor pressure is released.
Which brings us back to straws. As mentioned before, remelting straws significantly reduces the mechanical properties of the polymers. This loss of mechanical stability makes them unsuitable for use in new straws—but makes them perfect for use in refractory castables.
In an email, Salomão says he has studied polymeric fibers for refractory materials with Pandolfelli since the early 2000s, when he was a Ph.D. student in Pandolfelli’s lab. But the idea to use polymeric fibers from recycled straws came in 2017 when he watched a video that showed a team of researchers helping a marine turtle who was choking on a plastic straw.
“It was really disturbing for me and gave me the idea of using such plastic waste to produce fibers for refractory castables,” he says.
For the recent study, Salomão and Pandolfelli collected two types of drinking straws from their university’s cafeterias—thinner ones made of HDPE and larger ones made of PP—and created several dense plastic rods by stuffing four folded straws into a single straw. They then put the rods into a hot-melt glue-gun and collected the melted plastic on a rotating barrel to create thin continuous fibers, which were chopped into 3–4-mm-long sections.
(For more details on their melt-spinning process, check out their article in the February 2008 issue of the Bulletin.)
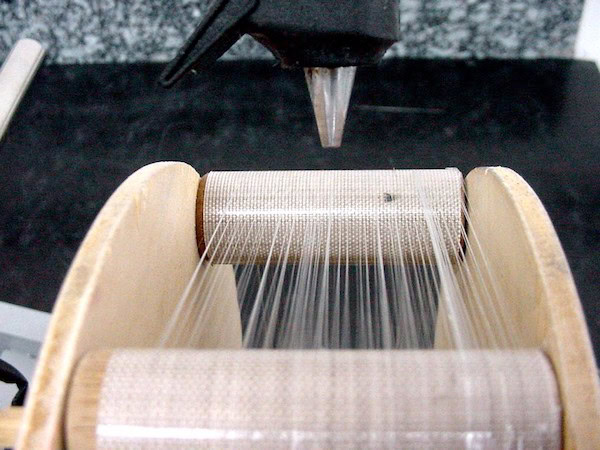
Salomão and Pandolfelli used a hot-melt glue-gun and rotating barrel to create thin continuous fibers from dense polymeric rods. Credit: Salomão and Pandolfelli
Salomão and Pandolfelli mixed the straw fibers with a high-alumina refractory castable; they also mixed a sample with unprocessed PP fibers for comparison.
Compared to unprocessed PP fibers, the straw fibers “presented a small but significant reduction in melting and decomposition temperature ranges.” In particular, while the unprocessed PP fibers melted around 168°C, the straw-PP melted around 161°C and the straw-HDPE at about 141°C.
Not only did this lower melting temperature mean the castables experienced earlier permeability and shorter drying times, but “the most significant technological impacts of such benefits are the reduction of energy and time consumption during the installation of refractory castables and the possibility of finding a better way of disposing of plastic waste,” Salomão and Pandolfelli write.
However, they point out that refractory castables alone cannot deal with the entire straw production each year. “…Even if the estimated entire world annual production of pre-shaped and monolithic refractories were considered (approximately 8–10 × 106 tons), it would require almost 20 years of refractory consumption to use the straws produced in a single year,” they write.
Fortunately, they note that the results suggest these fibers can be used in civil construction concretes to prevent explosive spalling as well. And based on annual yearly production of civil concrete over the past decade, “it would require 5–30 × 5.106 tons of recycled fibers, which is roughly 30–160 times greater than the annual production of straws,” they conclude.
Salomão says they plan to test the fibers in construction concrete under firing conditions. They also intend to optimize the melt-spinning process to produce thinner fibers in a more reliable and reproducible way.
The paper, published in Ceramics International, is “Anti-spalling fibers for refractory castables: A potential application for recycling drinking straws” (DOI: 10.1016/j.ceramint.2020.02.122).
Author
Lisa McDonald
CTT Categories
- Environment
- Refractories