[Image above] Example of a silicon block being cut with a diamond wire. Though diamond wires cut more precisely than conventional multiwire slurry saws, the cutting process still leads to nearly 35–40% of the silicon being thrown away. Credit: Stefano Bernieri – Diamond Pauber, YouTube
When I think of electronics waste, I often consider the topic as relating to end-of-life use and what to do with the decommissioned parts. However, there is also waste generated during fabrication of electronic devices, for example, wastewaters during semiconductor production.
Silicon waste is a major byproduct from solar cell production. To create solar cells, silicon is doped, melted, and extracted into a round block (ingot). The ingot is cut into thin square wafers using, conventionally, multiwire slurry saws but more recently diamond wires.
Though diamond wires cut more precisely than the slurry method, the cutting process still leads to nearly 35–40% of the silicon being thrown away because the diameter of the diamond wires is close to the thickness of the silicon wafers.
The ultrafine silicon waste particles can cause secondary pollution to soil, air, and water resources, resulting in safety and environmental concerns. So, finding ways to recycle or reuse this silicon is a benefit to manufacturers and the environment.
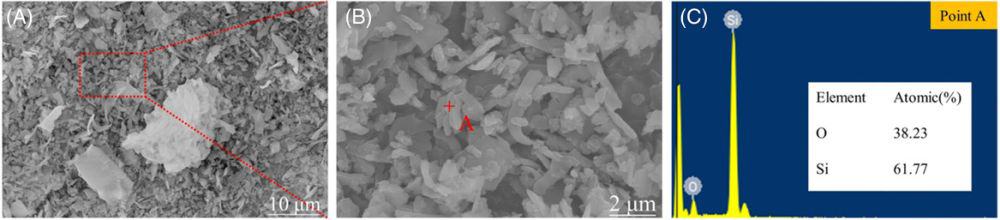
Scanning electron microscopy-energy-dispersive spectrometry analysis (A), (B and C) of diamond wire silicon cutting waste. Credit: Wang et al., International Journal of Applied Ceramic Technology
Several studies determined that silicon nitride (Si3N4) created out of diamond wire silicon cutting waste is a promising reuse method. Silicon nitride is an important high-temperature structural ceramic used in a wide variety of fields, including as engine core components, cutting tools, ball bearings, and gas turbines. It is typically prepared through direct nitridation of silicon powder, i.e., a heat-treating process that diffuses nitrogen into the surface of a material.
The fine particle size of diamond wire silicon cutting waste makes it favorable to nitridation. However, this waste powder has a different phase composition and microstructure than pure silicon powder. So, while the nitridation process of pure silicon powder is regarded as a simple gas-solid reaction, the kinetics and phase evolution are more complex when nitriding silicon waste powder from diamond wire cutting.
In recent years, a group of researchers from Northeastern University (Shenyang, China) have published several papers on this topic (such as the two 2020 papers here and here). This October, they published two more papers revealing further insights into the nitridation of diamond wire silicon cutting waste.
The first paper, which published October 15, looked to clarify the complex nitridation mechanism of the silicon waste powder.
The researchers used X-ray diffraction to detect phase compositions in the processed materials. They used field-emission scanning electron microscopy equipped with energy dispersive spectrometry and transmission electron microscope with selected area electron diffraction analysis to characterize the microstructures and morphologies.
Analysis revealed that out of three reaction models often used to describe the dynamics of gas-solid reactions, the grain model—which regards each silicon waste particle as a compact grain—did a good job explaining the results.
Essentially, the nitrogen would first react with the external grains in the accumulated silicon waste powder, then diffuse through the pores and react with the internal grains, and finally diffuse through the product layer and react with the remaining unreacted grains. The morphology and composition of the resulting silicon nitride were primarily influenced by the nitriding temperature and holding time.
Pure silicon nitride powders were obtained by nitriding at 1,550°C for 10 hours. However, particles with Si3N4@Si2N2O core-shell structure were obtained by nitriding at 1,450°C for 10 hours, “which would be a good raw material for preparing the Si3N4–Si2N2O composite ceramics with special performances,” the researchers write.
The second paper, which published October 18, explored how the common sintering aid yttrium oxide (Y2O3) affected nitridation.
Sintering aids are materials that, when added to a reaction, can aid in densification by allowing the process to take place at a lower temperature or occur more quickly, for example. Yttrium oxide is a common sintering additive used in production of silicon nitride.
Using a variety of characterization tools, including scanning electron microscope-energy-dispersive spectrometry, thermogravimetry analysis, and differential thermal analysis, the researchers found yttrium oxide does aid nitridation of diamond wire silicon cutting waste. Specifically, it can disrupt the native silica film, which causes many cracks to appear on the surface of the cutting waste particles.
“Thus, the good channel is provided for the diffusion of SiO and N2, the resistance of gas phase diffusion is reduced, and the overall conversion of cutting waste is improved,” they write.
To illustrate this point, consider that it required nitriding at 1,550°C for 10 hours to obtain pure silicon nitride powders in the previous paper. In this case, complete nitridation of the powders containing 8 wt.% yttrium oxide was achieved at 1,350°C in 2 hours.
The October 15 paper, published in Journal of Cleaner Production, is “Recycling the diamond-wire saw silicon powder for preparing the regulable Si3N4 materials by non-catalytic nitridation” (DOI: 10.1016/j.jclepro.2022.133656).
The October 18 paper, published in International Journal of Applied Ceramic Technology, is “Effect of Y2O3 additive on nitridation of diamond wire silicon cutting waste” (DOI: 10.1111/ijac.14242).
Author
Lisa McDonald
CTT Categories
- Environment
- Manufacturing