[Image above] Workers install new refractory bricks in a cement rotary kiln. Credit: Engineering Dots, YouTube
Since development of successful designs in the late 1800s, rotary kilns are now an essential tool in cement production.
Rotary kilns are pyroprocessing devices used to cause physical changes or chemical reactions in various materials through heat. These kilns consist of a slowly rotating heated tube positioned at a slight slope. Material is placed into the upper end of the kiln and then gradually moves downhill through the heated area as the kiln rotates.
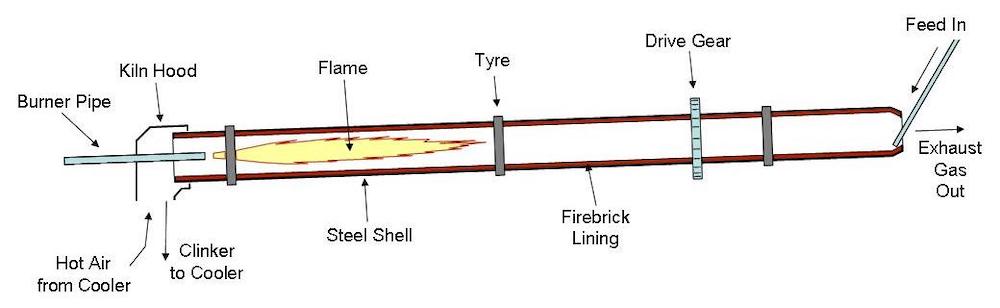
General layout of a direct fired countercurrent rotary kiln used in cement manufacturing. Credit: LinguisticDemographer, Wikimedia (Public domain)
The tube in a rotary kiln is typically made from steel plates lined with refractory ceramics. Steel is used for several advantageous reasons, particularly the fact that it will react with components in the refractory to form low fusibility minerals, which serve to essentially turn the assembled bricks into a single unitary construction.
There can be challenges with using steel plates, however. Despite the refractory lining, the steel plates can sometimes become too hot and begin melting, causing partial voids in the joints. These voids can lead to stress concentrations and cracks in the kiln, resulting in catastrophic wear.
Thus, “although the steel plate is a very effective joint material, it is important to select an appropriate joint material according to the usage environment,” researchers write in a recent Taikabutsu Overseas paper.
Taikabutsu Overseas is the English translation for the journal Taikabutsu (耐火物), or Journal of the Technical Association of Refractories, Japan. Charles Semler, an ACerS Fellow and founder of refractories consultant company Semler Materials Services, is the international adviser for the journal, which features translations of articles previously published in Taikabutsu.
The recent translated paper appears in Volume 41, Issue 2 of Taikabutsu Overseas (pages 64–69). It is translated from a paper published in the November 2019 issue of Taikabutsu on page 481.
In the paper, researchers from AGC Ceramics Co., Ltd. in Takasago, Japan, explored whether a basic mortar could be used instead of steel plates to join refractory bricks in rotary kilns. They chose mortar because “basic mortar does not form gaps on the hot face side or a penetration layer into bricks because of its high heat resisting properties,” they write.
They tested the performance of steel plates and mortar as joint materials in three types of atmospheres: air, low oxygen, and sulfur. Among these conditions, it was the sulfur atmosphere that benefitted most from using mortar because the mortar did not disappear (the steel plates melted and diffused into the bricks) and demonstrated excellent stress relaxation properties.
Ultimately, the researchers conclude their results demonstrate why “it is important to study the joint material that suits the environment inside the furnace and the structures.”
The paper, published in Journal of the Technical Association of Refractories, Japan, is “The influence of steel plates on refractory in cement rotary kilns.” (Original title: セメントロータリーキルンにおける目地鉄板の耐火物への影響. Translated from Taikabutsu, November 2019, pg. 481.)
Author
Lisa McDonald
CTT Categories
- Cement
- Manufacturing
- Refractories