[Image above] A midmorning break provides time to talk and network. Credit: ACerS
I’m in the beautiful city of Vancouver, Canada, where the 11th International Conference on Ceramic Materials and Components for Energy and Environment Applications is underway. The conference opened yesterday and runs through Friday.
One need only look out the window of the conference venue for a visual anchor of the contrast this conference addresses—a cosmopolitan city of skyscrapers, air conditioning, transportation of every sort, and electronic devices of every sort—against a backdrop of Vancouver Bay and mountains on its opposite shore.
Progress versus the pristine.
Thankfully, 550 of the smartest minds from 45 countries are here to grapple with the ceramic materials aspects of energy and environmental technologies.
Coorganizers Tatsuki Ohji, Alex Michaelis, and Mrityunjay Singh opened the conference and plenary session with the theme, “Ceramic Technologies for Sustainable Development.” The term “sustainable” may mean different things to different people, however, a common thread of cost-effectiveness as it applies to energy wove through all four talks.
Leading off the session, Dan Arvizu, director of the National Renewable Energy Lab in Colorado, spoke on the topic of “Maximizing the potential of renewable energy.”
Arvizu describes himself as a “technology agnostic” advocate for transforming today’s unsustainable energy systems to a future powered by sustainable energy systems. “We should not care what technology gets us there,” he says.
The market dynamics must be considered, Arvizu emphasized. “It’s always about the money,” he says. Over the last 10 years, for example, $2 trillion was spent to deploy renewables. Infrastructure investment in just the United States could reach $20 trillion over the next decade. He says research from the 1970s led to the commercial renewable energy systems. “We need different technologies to get us where we need to go,” says Arvizu. “Technologists reduce the risk of investors.”
“We are at the beginning part of a transformation,” he says. “There’s lots of opportunities and lots of options, and we’re not sure where we’re going to end up.” But it will take a partnership between technologists, investors, and policy makers.
Some of Arvizu’s points were demonstrated in the second speaker’s talk. Tony Leo of Fuel Cell Energy Inc., (Conn.) spoke on the role of fuel cells in the national energy portfolio. The balance between technology strengths and weaknesses dictate applications and commercial opportunities. “Fuel cells still sit at the nexus between energy policy, economic policy, and environmental policy,” he says.
Government policy helps monetize the less tangible values of fuel cell energy, he says, such as eliminating transmission and distribution, improving grid resiliency in the face of calamities such as hurricanes, and lack of noxious emissions. A significant challenge from a business perspective is the lack of a national energy policy. Instead, companies such as FCE must deal with 50 state policies.
To demonstrate the elegance of clean energy systems, Leo described a molten carbonate fuel cell system his company installed at a wastewater treatment facility. The system runs off methane byproduct from the digester. In turn, it provides power to the plant and heat for the digester system. The fuel cell tolerates the carbon dioxide excess in the methane and has reduced NOx emissions by 10 tons/year, simply by not generating new NOx.
Moving away from energy conversion technologies, Sanjay Correa of GE Aviation described GE’s investment in ceramic matrix composites and the significant energy savings new aircraft engines are expected to realize.
Correa noted that materials advances have preceded aviation advances, citing aluminum production technology and superalloy development. GE expects similar advances in engine technology from its SiCf–SiC/Si composites. These materials weigh only one-third of the metal parts they replace and allow engines to run hotter than they do now—with a combined effect of increasing fuel efficiency by two percent.
Two percent might seem unimpressive, but, Correa says, “The reality is, for airlines it adds up to a lot of money.” For example, a one percent improvement in a two-aisle aircraft saves $2 million per aircraft, which translates to $3 billion in savings for the fleet. The savings are even more significant for single-aisle aircraft because more of them will be built: $1 million per aircraft; $14 billion for the fleet.
Rounding out the plenary session, Richard Metzler of Rauschert GmbH (Germany) talked about how the company used the 2008 global recession to spur innovation and energy efficiency. The company had been quite successful for more than 100 years as a ceramic component manufacturer.
In 2008, the company lost half its revenue overnight, according to Metzler. “We realized we needed to develop new things that are our own products,” he says. “We were looking to reduce risk and maximize long-term stability.” On the efficiency side, the company developed a power microgrid system to optimize energy use during production. Meanwhile, they developed several products of its own that address energy efficiency, such as ceramic liquid separation membranes.
The conference continues with technical sessions, a poster session, and conference banquet. Meanwhile, enjoy a few photos from the first few days of the conference.
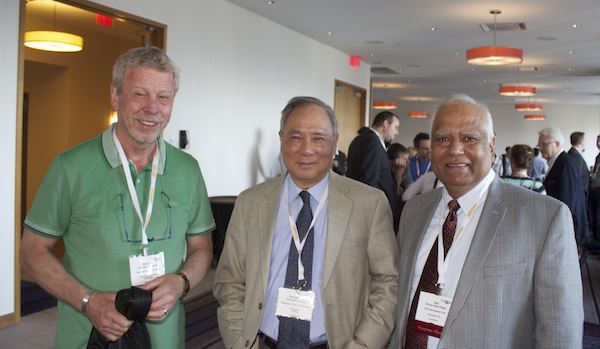
The technical program includes two honorary symposia. The symposium honoring Juergen Heinrich (left) is on laser processing of materials. The symposium honoring Donling Jiang (center) is on innovative processing and microstructural design of advanced ceramics. Jay Singh (right) served as chair of CMCEE. Credit: ACerS
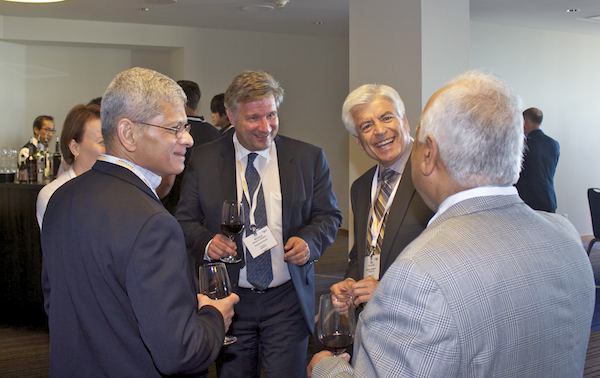
Three of the four plenary speakers chat with conference organizer, Jay Singh. From left: Sanjay Correa, Richard Metzler, Dan Arvizu, and Singh (back to the camera). Cheryl Brayman is barely visible between Correa and Metzler. Brayman is US-based business development director of Inopor GmbH, which is affiliated with Rautschert, the company Metzler works for. Credit: ACerS
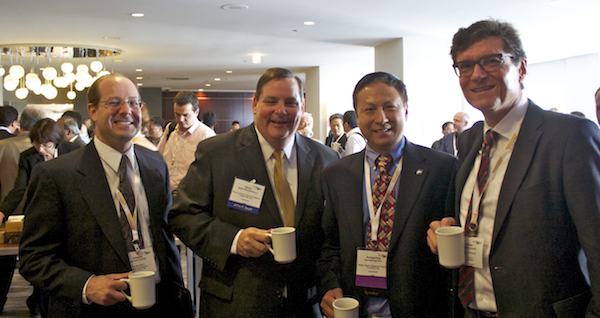
Lots of good things happen at breaks. Delicious coffee is just one. From left: Mike Halbig, Mark Mecklenborg, Dongming Zhu, and Walter Krenkel. Credit: ACerS
Author
Eileen De Guire
Spotlight Categories
- Meeting Highlights