[Image above] Example of a Bavarian porcelain plate done in the Dresden style with reticulation along the edges. Credit: My Take On Home & Garden, YouTube
The year is 1700. Alchemists across Europe are chasing the Philosopher’s Stone, a substance that would transmute base metals into gold.
An impetuous teenage alchemist’s apprentice named Johann Friedrich Böttger claimed to know its secret. When word of his knowledge got out, Frederick I of Prussia kidnapped Böttger. Then, Augustus II (the Strong) of Poland kidnapped him from Frederick I and managed to hold on to him for several years, growing steadily more impatient with his failures to produce gold.
Although impetuous, Böttger was smart and decided he had better come up with something good. In his quest to produce gold, he developed some heat-resistant crucibles made of durable red stoneware. This success gave him the idea to pivot to making porcelain.
Europeans covet the hard-paste porcelain produced by the Ming Dynasty in China. They know that it contains kaolin but are unable to figure out what it is mixed with or how to reach the high firing temperatures required (between 2,200°F and 2,600°F; approximately 1,200°C to 1,425°C).
Böttger teamed up with Ehrenfried Walther von Tschirnhaus, whose own porcelain pursuits had come close to success already. The two worked together to replicate hard-paste porcelain. Böttger redeemed himself in the eyes of Augustus II when, in 1709, he combined kaolin, feldspar, and quartz to produce true hard-paste porcelain. These efforts led to the founding of the Meissen porcelain factory in 1710.
Early history of porcelain in Europe
Porcelain’s complicated European story does not end in Meissen. A French Jesuit priest, Father Francois Xavier d’Entrecolles, had been sent to Jingdezhen, China, in 1698. It seems clear from his letters that a major purpose of his mission was to gain the secret of hard-paste porcelain production. By 1718, his conversations with porcelain workers who converted to Catholicism had provided enough details to establish a rival porcelain business in Vienna.
Silkworms, another of China’s cultural treasures, had previously been stolen by Catholic missionaries in the mid-sixth century. The removal of silkworms from China is the first example of industrial espionage and could have gotten the responsible priests killed. Four additional pivotal inventions also have roots in China (among many others): gunpowder, the compass, paper, and movable type. Recognizing the loss of crucial cultural secrets provides some context for China’s seemingly cavalier view on modern “technology transfer”—there is a lot of history behind their current approach!
The Meissen and Vienna manufactories were the first hard-paste porcelain production sites in Europe. Or were they? There is some evidence to suggest that European hard-paste porcelain was produced in England sometime before 1683. Several small pots in the Burghley House collection are connected to the 2nd Duke of Buckingham, George Villiers, who was keenly interested in science and alchemy. The English porcelain recipe is different from both the Chinese porcelain and the Meissen/Vienna porcelain, so the claim is not without merit.
Böttger luster: An enduring legacy
After developing expertise in producing porcelain, artisans in Europe began to experiment with decorating it in styles that were uniquely their own. Artists struggled at first to develop appropriate glaze formulas because of the high firing temperatures required for porcelain production.
One of the eventual differentiators of European porcelain production was an overglaze known as Böttger luster, developed in the Meissen porcelain manufactory. It is attributed to Johann Friedrich Böttger, the alchemist who was trying to turn base metals into gold. His namesake luster contains gold nanoparticles, which give it an unmistakable purple iridescence.
By the late 18th century, artists in Europe had developed the distinctive colors and themes that make these porcelain producers’ wares instantly recognizable. European porcelain had become every bit as elaborate and sought after as its Chinese forebears.
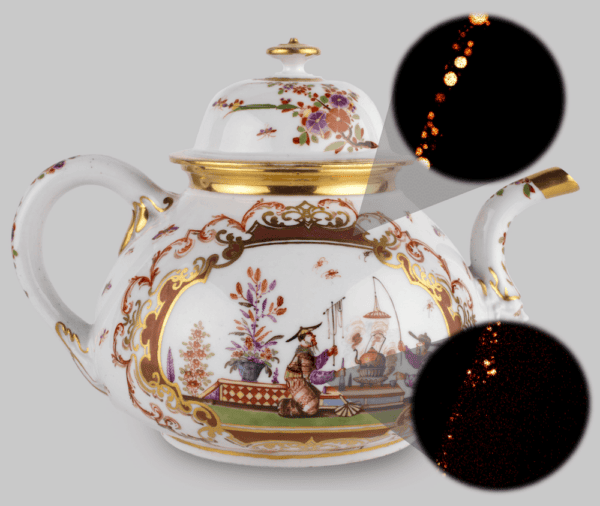
18th century Meissen teapot (Art Institute of Chicago) with Böttger luster (top) and Purple of Cassius enamel (bottom) noted with cross-sectional maps of gold nanoparticle signatures from energy dispersive X-ray spectroscopy. Credit: Celia Chari
Dresden porcelain plates and their namesake quilts
Despite the name, no actual porcelain was produced in Dresden—it was produced in Meissen, then shipped to Dresden for decorating and sale. White Meissen porcelain pieces—often factory seconds (pieces not perfectly made)—were decorated by artists in Dresden, which became the cultural center of Saxony and, perhaps, of Europe. Before the devastating fire-bombing at the close of World War II, Dresden was known as Germany’s Florence. Today, the city has been rebuilt, evoking much of its prewar Baroque glory.
Dresden-style porcelain really took off in the 19th century, when Romanticism captured the world’s fancy. The designers and artists in Dresden embellished the plates in many ways, adding three-dimensional elements such as ribbons and flowers, as well as experimenting with colorful glazes.
Some of the porcelain received delicate patterned edges by reticulation, in which small, interlaced holes are cut individually into the unfired porcelain as it dries. This practice is both time-consuming and meticulous.
Another technique that Dresden artists are well known for was the development of Dresden lace. Cotton lace was carefully coated with porcelain slip and then applied to figurines. When the figurines were fired, the cotton burned away, leaving the delicate porcelain lace decoration behind.
The fragility and exquisite artwork of the Dresden plates increased their value and, in turn, inspired fabric artists.
The Dresden plate quilt pattern reached its peak of popularity in the 1920s and 30s. However, the quilt block’s shape is not modeled on the fronts of the plate; rather, it is modeled on the mark that Dresden artists used on the back or bottom of plates to identify their work. The blue crown mark became the model for the quilt block’s alternating pattern of rounded and pointed wedge ends.
From industrial espionage to nanoparticles to fabric arts, the influence of porcelain production on history is indisputable.
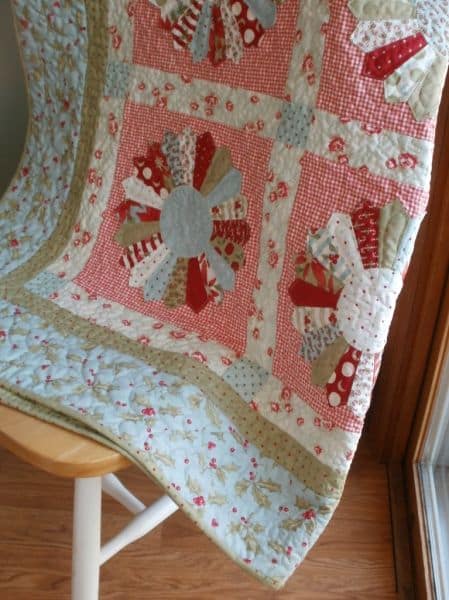
Example of the Dresden plate quilt pattern. Credit: Amy, Flickr (CC BY-NC-SA 2.0)
Further reading
Chari, C.S., et al., “Nanoscale engineering of gold particles in 18th century Böttger lusters and glazes,” Proceedings of the National Academy of Sciences 2022, 119(18), e2120753119.
Hoffman, R. “Meissen chymistry,” American Scientist 2004 92(4), 312.
Author
Becky Stewart
CTT Categories
- Education