[Image above] A new beetle-inspired ceramic radiative coating applied on a house roof. Credit: City University of Hong Kong
More people are at risk from heat-related diseases and death than ever before as global temperatures continue to rise. Though air conditioners may appear to be a solution, use of this technology leads to the emission of hydrofluorocarbons and greenhouse gases, which drive climate change. While energy-efficient air conditioners help reduce emissions from these devices, other cooling methods that do not cause any emissions are needed.
Radiative coatings can provide passive cooling without the use of mechanical refrigeration equipment. These coatings are designed to reflect solar radiation and emit thermal radiation to the cold outer space, thereby achieving electricity-free spontaneous cooling.
Researchers have made numerous advancements in radiative coatings in recent years, thanks largely to innovations in micro/nanofabrication. Today’s CTT overviews two recent papers, both published in volume 382, issue 6671 of Science, that harnessed such manufacturing techniques to develop new radiative coatings.
Beetle-inspired ceramic coating achieves near-perfect solar reflectivity
Researchers at several Hong Kong universities designed a new ceramic radiative coating that exhibits a near-perfect solar reflectivity of 99.6%. The coating’s impressive properties are due to its nanostructure, which was inspired by the Cyphochilus beetle.
The Cyphochilus beetle, native to Southeast Asia, is considered the whitest insect on Earth. Its coloring is due to the arrangement of tiny tear-shaped scales that cover the beetle’s whole exoskeleton.
These scales, only 6 µm thick, form a highly connected and dense network of chitin, i.e., a long-chain polymer that gives strength to the exoskeletons of crustaceans, insects, and the cell walls of fungi. Chitin scatters light extremely efficiently, resulting in the ultrawhite appearance.
Previous studies, such as here, have drawn inspiration from the Cyphochilus beetle to create sustainable and biocompatible ultrawhite coatings. But the new study took this inspiration a step further by creating a coating that is both aesthetic and functional.
The Hong Kong researchers fabricated the ceramic coating through a process that can be easily scaled for mass production. First, they cast a solution of polyethersulfone (PES), N-methyl-2-pyrrolidone (NMP), and alpha-alumina onto a flat substrate and immersed it in ethanol, which caused the NMP to dissolve. They then sintered the material to remove the PES and bond the alumina particles in a porous pattern that resembles the Cyphochilus beetle scales.
In addition to a record-high solar reflectivity of 99.6%, the final alumina coating exhibited an infrared thermal emission of 96.5% and withstood temperatures of more than 1,000°C (1,832°F). When applied to a house roof, the coating reduced the amount of electricity used for space cooling by 20%.
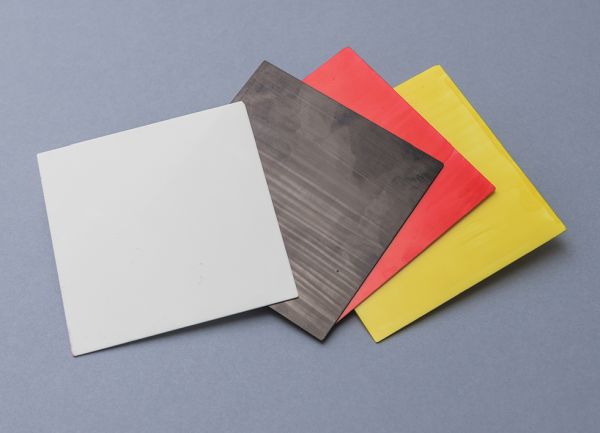
Samples of the beetle-inspired ceramic radiative coating in different colors. Credit: City University of Hong Kong
Other characteristics of the ceramic radiative coating include
- Ultralow thickness. The coating requires a thickness of only 150 µm to achieve a reflectance above 95%. Conventional high-performance roof cooling coatings typically require a thickness above 1 mm.
- High mechanical strength. The coating demonstrates a high mechanical strength of more than 100 MPa (building envelopes require a minimum of 35 MPa).
- Low reflectivity. The coating has low reflectivity within the atmospheric window transmittance range at any thickness, making it suitable for coating concrete and similar substrates.
- Subambient cooling. The coating achieves subambient cooling above 4°C even around midday (between 11 a.m. and 2 p.m.), resulting in lower temperatures compared to white commercial tiles.
- Either water-loving or water-repelling. The coating can be converted from superhydrophilic (attracted to water) to hydrophobic (repels water) by impregnation with organosilicon compounds. This change to the coating causes only a small drop in solar reflectance.
- Resistant to environmental stimuli. The coating resists pollutants when treated with fluorosilane, maintaining a solar reflectance above 97%. The coating also exhibits resistance to ultraviolet radiation and fire.
- Recyclable. The coating is recyclable and can be turned into a new material with well-preserved optical properties.
- Color options. The coating can be colored using a dual-layer design while mostly retaining its reflective properties. For example, yellow, red, and green coatings exhibited reflectivity in the near infrared region of 95%, 96%, and 87%, respectively.
“[This study] confirms the great potential of cooling ceramic in reducing people’s reliance on traditional active cooling strategies and provides a sustainable solution for avoiding electricity grid overload, greenhouse gas emissions, and urban heat islands,” says Chi Yan Tso, associate professor of energy and environment at the City University of Hong Kong, in a university press release.
The paper, published in Science, is “Hierarchically structured passive radiative cooling ceramic with high solar reflectivity” (DOI: 10.1126/science.adi4725).
Microporous glass coating enables temperature drop even under high-humidity conditions
Researchers at the University of Maryland and the University of Wisconsin-Madison used a solution-based process to fabricate a microporous glass coating that achieves a cooling effect even under high-humidity conditions.
The solution consisted of phosphate glass particles (2–15 μm) and alpha-alumina nanoparticles (0.3–1.0 μm) suspended in ethanol. The glass particles acted as a nonconventional binder to form a robust porous supportive framework, while the alumina particles strongly scattered light and prevented densification of the porous structure during manufacturing.
After sintering at about 600°C, the glass particles formed an interconnected mesoporous structure, with the alumina particles surrounded by the glass. Scanning electron microscopy analysis showed a porosity of about 50% and an average pore size of 6.7 μm.
Testing identified the optimal mass fraction of alumina particles to be 40–60 wt.%. Coating thickness needed to be more than 500 µm to achieve solar reflectance greater than 95%.
The researchers note that the solution’s viscosity could be modified for different coating techniques, such as spray or brush coating, thus allowing the coating to be applied with good adhesion on various substrates, including brick, tile, metal, and glass.
However, solar reflectance depended on the coating method. Compared with brush-on glass coatings, spray-on glass coatings had a rougher, more porous structure, resulting in slightly lower solar reflectance. Increasing the alumina mass fraction to about 60 wt.% in spray-on coatings achieved solar reflectance of more than 96% at a thickness of about 500 µm.
Other advantages of the glass radiative coating include
- Combines high solar reflectance (>96%) and high infrared emissivity (95%) in the atmospheric transparency window.
- Enables temperature drop of about 3.5° and 4°C during midday and nighttime, respectively, even under high-humidity conditions (up to 80%).
- When applied to roofing, can reduce annual carbon dioxide emissions by about 10%, resulting in an average annual cost savings of about $350 for old buildings and about $290 for new buildings.
- Maintains high solar reflectance even when exposed to harsh conditions, including water, ultraviolet radiation, soiling, and high-temperature flame shock.
- Compatible with several different combinations of glasses featuring different softening points (300°C to 1,000°C) and dielectric particles (titanium dioxide, zinc oxide, boron nitride).
- Can incorporate inorganic dyes to produce pink, green, and yellow colors while retaining solar reflectance properties ranging from 90% to 95%.
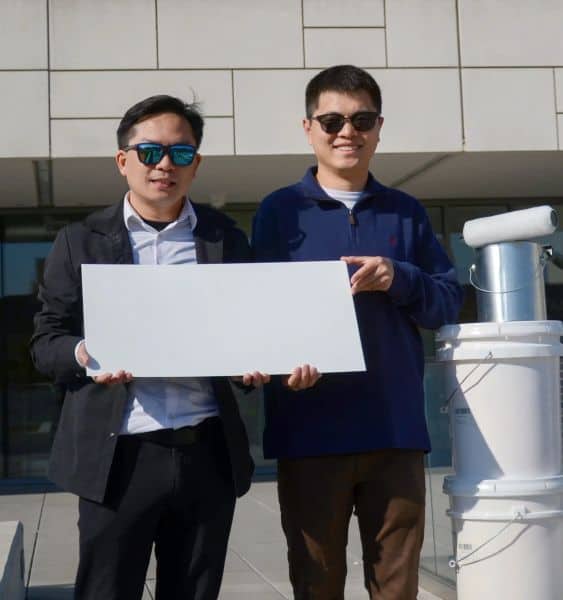
Distinguished University Professor Liangbing Hu (left) and assistant research scientist Xinpeng Zhao at the University of Maryland display a panel of steel coated with their new radiative cooling glass. Credit: A. James Clark School of Engineering, University of Maryland
“It’s a game-changing technology that simplifies how we keep buildings cool and energy-efficient,” concludes first author Xinpeng Zhao, assistant research scientist at the University of Maryland, in a university press release.
The researchers established a startup company called CeraCool to scale up and commercialize the glass coating technology.
The paper, published in Science, is “A solution-processed radiative cooling glass” (DOI: 10.1126/science.adi2224).
Author
Laurel Sheppard
CTT Categories
- Energy
- Environment
- Glass
- Thermal management