[Image above] Swedish multinational engineering firm Sandvik announced a new 3D printable cemented carbide in April 2022. Credit: Sandvik Additive Manufacturing, YouTube
Improving the speed, cost, and energy aspects of a fabrication process is top of mind for manufacturers, especially those working with difficult-to-handle materials such as cemented carbides.
Cemented carbides are metal matrix composites used extensively as cutting tool materials because of their high hardness, wear resistance, and fracture strength. Tungsten carbide–cobalt cemented carbides, in which cobalt is the cementing phase between the tungsten carbide grains, are one of the main types of cemented carbides used.
Cemented carbide parts traditionally are shaped through subtractive machining processes, which are difficult to implement due to the high hardness of the material. As such, in recent years, researchers across government, industry, and academia are exploring the use of additive manufacturing processes to fabricate cemented carbides parts.
Some methods have even been commercialized, such as the 3D printable cemented carbide announced by Swedish multinational engineering firm Sandvik in April 2022. (See Sandvik’s announcement video below.)
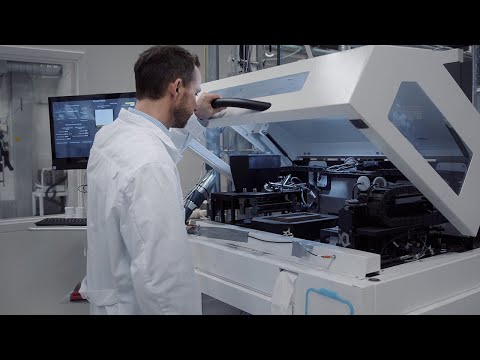
Credit: Sandvik Additive Manufacturing, YouTube
Binder jetting is a main additive manufacturing method explored for creating cemented carbide parts. In this process, a liquid binding agent is selectively deposited to join powder material together to form a 3D part. The printed part is cured to improve the handling strength and then subjected to debinding and sintering using conventional powder metallurgy techniques.
Grain size of the cemented carbide is an important property to consider when fabricating the 3D-printed part. In a recent paper, researchers from Global Tungsten & Powders Corp. (Towanda, Pa.) explain that previous studies (here and here) found while cemented carbide parts with dual grain size microstructures demonstrated good hardness and high wear resistance, the parts also exhibited a lower transverse rupture strength compared to conventionally produced cemented carbides with a uniform grain size.
In light of this knowledge, the researchers explored the creation of 3D-printed cemented carbide parts with a uniform grain size to analyze the effect on properties.
They used prealloyed, spherical tungsten carbide–cobalt powders with 10 and 12 wt.% cobalt to create the cemented carbide parts. The binder employed in the printing process (a water-based diethylene glycol monoethyl ether) was provided by ExOne Inc.
After printing, the parts were cured by heating to 200°C in air. Then, they were debound and liquid phase sintered in the presence of external pressure (applied by argon gas).
Wear properties of the sintered samples were determined using the ASTM B611 (higher wear) and ASTM G65 (lower wear) testing procedures. ASTM B611 involves forcing an abrasive material (in this case alumina) against the test specimen with a steel wheel. ASTM G65 involves forcing dry sand (silica) against the test specimen with a rubber wheel.
Testing revealed the 3D-printed cemented carbides demonstrated hardness, fracture toughness, and wear resistance values that matched conventionally produced parts. However, the transverse rupture strength remained at the low end of the conventionally produced range.
Despite the unfavorable outcome regarding transverse rupture strength, the researchers still considered the experiment a success.
“The new powders exhibited excellent printability and sinterability. … [as well as] good handling strength after curing,” they write. Thus, “These parts exemplify the advantages offered by BJ3DP [binder jetting 3D printing].”
The paper, published in International Journal of Refractory Metals and Hard Materials, is “Coarse cemented carbide produced via binder jetting 3D printing” (DOI: 10.1016/j.ijrmhm.2022.106016).
Author
Lisa McDonald
CTT Categories
- Manufacturing