[Image above] Ouch. Credit: Sharon Drummond; Flickr CC BY-NC-SA 2.0
[Title inspiration: Ron Popeil’s infomercial-tastic Showtime Rotisserie. Just set it, and forget it!]
If you’ve ever sprained, strained, pulled, or disconnected a tendon or ligament, you know it can be a slow road to recovery.
[The difference between tendons and ligaments? Tendons connect muscle to bone or other structures, while ligaments connect bone to bone.]
That’s because healing tissues that are meant to flex and bend is tricky—you can’t just immobilize them and wait for them to heal in place, like bone. But you also can’t just let them continue stretching and moving, or they’ll never heal properly—especially those that have separated completely.
To heal properly, moving parts need limited movement yet adequate mechanical strain to promote proper healing and prevent buildup of scar tissue. And for parts that have completely separated, they need to be reattached, too.
Tendon and ligament injuries are specifically common to human shoulder joints, a place where a little innovation is needed to sufficiently put the moving parts back together again.
Surgeons have lots of innovations at their disposal, one of which is the aptly named suture anchor. These little pieces of hardware look like a dull screw with an eyelet instead of a head. They work by screwing into the bone and leaving the eyelet accessible to attach sutures to, providing a stable anchor point for tendons, ligaments, and such.
Suture anchors themselves are nothing new (surgeons have been using them since the 1990s). The hardware can be composed of titanium, but metal can be problematic because it can eventually damage repaired tissues. Alternatively, non-absorable and absorbable polymer suture anchors have been used, but there are some concerns about the strength of polymer replacements.
The researchers are Fraunhofer Institute (Germany) have a solution in metal-ceramic composites, however, which they are using to fashion into bioabsorbable implants. Bioabsorbable is preferable in the case of soft tissue fixes because the hardware is no longer needed after the injury is repaired.
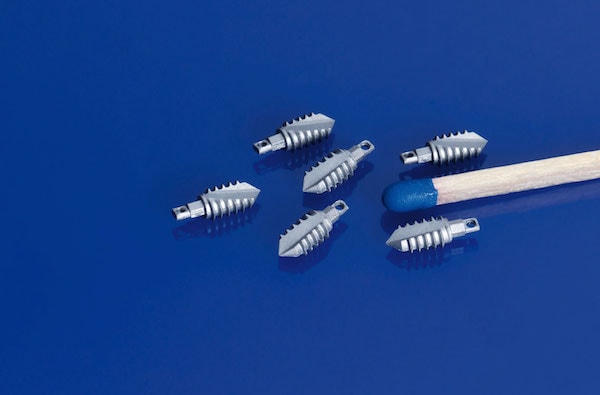
New metal–ceramic composite suture anchors are barely bigger than a match head. Credit: Fraunhofer IFAM
“With the implant, severed tendons can be anchored to the bone until they have grown again,” says Philipp Imgrund, Fraunhofer manager of Medical Technology and Life Sciences, in a Fraunhofer press release. “Since the function of the fixing element is satisfied after the healing process, it is no longer needed in the body. If implants or protheses that are as wear resistant as possible are required—such as in an artificial hip joint—metallic alloys such as titanium will certainly continue to be used. However, for plates, screws, pins and nails which should not remain in the body, there are other requirements.”
Using powder injection molding, the team fabricated suture anchors, merely bigger than a match head, out of an optimized mix of 60% iron alloy and 40% beta-tricalcium phosphate ceramic. The researchers used injection molding because, while being economical and scalable, the process allowed them to control the composition’s strength through density and porosity.
“Iron alloys corrode slowly and ensure high mechanical strength, while ceramic decomposes quickly, stimulates bone growth and aids the ingrowth of the implant,” Imgrund says. “It is important to determine the right amount of ceramics as a function of the powder amount. If the proportion is too high, the material will be brittle. On the other hand, the tricalcium phosphate accelerates the degradation of the implant.”
Because the team is pioneering this process with powder injection molding, that also means that they can adjust the composition of the powders that comprise the hardware, allowing them to adjust the degradation rate of the implant.
According to the release, the researchers achieved degradation rates “in a laboratory model” that would mean the anchor would absorb in the body within one to two years. According to the release, part of the team is now working on an “in-vivo monitoring system that can monitor and document the degradation behavior of the implants in the human body,” so we’ll have to stay tuned to see how the new hardware holds up in further tests.
Author
April Gocha
CTT Categories
- Biomaterials & Medical
- Material Innovations