[Image above] A transparent dome-shaped spinel component sintered by the U.S. Naval Research Laboratory. Credit: U.S. Naval Research Laboratory; Jamie Hartman
About a year ago, I reported on advances at the U.S. Naval Research Lab (NRL) that were making spinel 50% harder than existent transparent armor. The NRL scientists had done so by pioneering a sintering technique called enhanced high pressure sintering.
Why were the scientists messing around with spinel in the first place? Spinel is a glass alternative with some serious advantages—and serious commercial potential.
“Spinel is actually a mineral, it’s magnesium aluminate,” says Jas Sanghera, who leads the research at NRL, in a press release. “The advantage is it’s so much tougher, stronger, harder than glass. It provides better protection in more hostile environments—so it can withstand sand and rain erosion…For weight-sensitive platforms—UAVs [unmanned autonomous vehicles], head-mounted face shields—it’s a game-changing technology.”
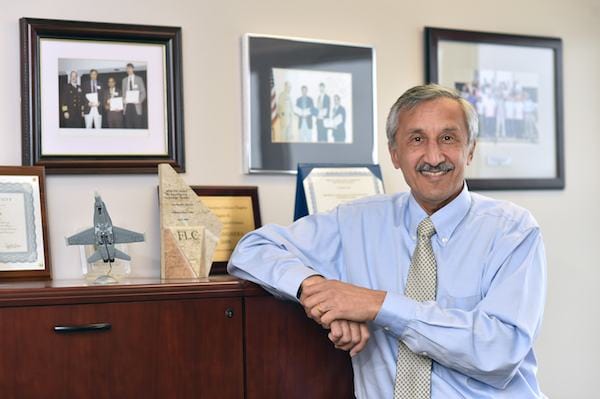
Jas Sanghera at the U.S. Naval Research Laboratory. Credit: U.S. Naval Research Laboratory; Jamie Hartman
Transparent armor is stronger and more durable than amorphous glass because spinel has a polycrystalline structure, which provides sinks for dissipating crack energy. That strength means less spinel is needed to achieve similar or better levels of protection as provided by bulletproof—or, more accurately, bullet resistant—glass, with less material and less weight.
[For more about transparent armor, including aluminum oxynitride and magnesium aluminate spinel varieties, travel back in time to the cover story in the March 2013 issue of the Bulletin.]
NRL scientists have continued experimenting with sintering to the point where their technique can not only produce harder ceramics, but also larger pieces and those with challenging shapes—all thanks to a deconstruction of the science behind the process.
Although NRL wasn’t first to sinter spinel, its scientists perfected the process to optimize fabrication of larger and more complex pieces of spinel, according to the NRL press release. Previous iterations of the method produced inconsistent results, with only portions of the sintered material coming out of the hot press transparent.
Digging deeper into the science behind the process, NRL researchers found that a big problem with fabricating transparent spinel was the starting materials, which need to be superbly pure to get a quality final product. “Lousy chemicals in, lousy material out,” Sanghera says in the release.
In addition to the purity and quality of the starting materials, getting the mix of materials just right is equally critical. Sanghera says that the spinel powder they were using contained about 1% lithium fluoride sintering aid.
Although the sintering aid helps the process, it can at the same time hinder the final product. Reactions between the spinel powder and lithium fluoride can produce scattering sites within the material, creating opaque regions in the otherwise clear product.
Part of the problem with lithium fluoride arises when the spinel powder particles aren’t mixed adequately. Although the NRL team was mixing in a shaker overnight, the process wasn’t getting the job done. “The thing is, on a scale of the powder, it’s never mixed uniformly,” Sanghera says.
Inputting a higher quality, thoroughly mixed spinel powder—achieved through a novel spray-coating process—into the hot press was key to producing uniform, clear, and uniquely shaped spinel products.
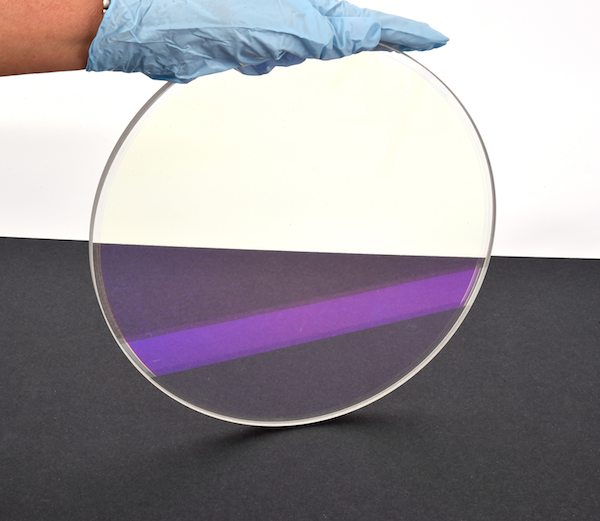
This spinel window has an infrared anti-reflective coating. Credit: U.S. Naval Research Laboratory; Jamie Hartman
Improved mixing also meant scientists could reduce the amount of lithium fluoride in the spinel powder. “Additionally, the sintering process was modified to completely eliminate residual LiF through evaporation and thereby avoids unwanted chemical reactions,” according to an NRL TechTransfer about the material.
The NRL press release states that the team is also working on ways to decrease the need to grind and polish the hot-off-the-hot-press product to reduce finishing costs and production time.
“Ultimately, we’re going to hand it over to industry, so it has to be a scalable process,” says Sanghera. In the lab, the NRL team pressed spinel pieces eight inches in diameter. “Then we licensed the technology to a company who was able then to scale that up to much larger plates, about 30-inches wide.”
The capability to scale the process, coupled with its ability to produce unique shapes—in concert with the fact that spinel allows infrared light to pass through—mean that the spinel components have many potential applications in defense systems.
But beyond those extreme environments, making the spinel better and more cost-effective could expand the reach of applications, too—even to watches, consumer electronics, and smartphones.
Could spinel be the next big thing to prevent scratched and cracked smartphone screens? You’re the experts—do you think that spinel will ever be able to compete with engineered glasses, such as Corning’s now fourth-generation Gorilla Glass, in consumer products?
Author
April Gocha
CTT Categories
- Material Innovations
- Optics