[Image above] A sample of transparent nanocrystalline spinel developed at University of California Davis. Credit: Nanoceramics Thermochemistry Laboratory
Editor’s note: This report comes to us from Ricardo Castro, professor in the Department of Materials Science & Engineering at the University of California Davis. For more information about Castro and his UC Davis lab, visit the Nanoceramics Thermochemistry Lab website.
By Ricardo Castro
Nanocrystalline ceramics can have extraordinarily high hardness.
Classic size–effect relationships predict that decreasing grain size will increase hardness, but the phenomenon is only observed when ceramics are pore-free—a condition difficult to achieve because elimination of porosity at final stages of sintering is linked to grain growth.
However, by further understanding the dependence between densification and grain growth, the Nanoceramics Thermochemistry Laboratory at the University of California, Davis—led by ACerS member Ricardo Castro—has circumvented this problem to devise a new process to fabricate fully dense ceramic parts with virtually no grain growth.
The method produced transparent nanocrystalline magnesium aluminate (MgAl2O4) spinel with grain sizes of 7 nm and a record-breaking Vickers hardness of 28.4 GPa—even harder than sapphire.
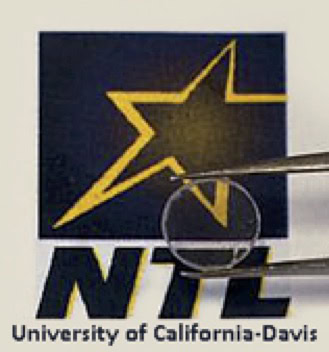
Credit: Nanoceramics Thermochemistry Laboratory
“Magnesium aluminate spinel is the primary material of choice for stringent optical and transparent armors, with a combination of high hardness, light weight, and broadband optical properties that exceed that of competing materials, such as sapphire and AlON,” Castro says. “However, high processing costs of truly dense spinel ceramics limits their market.”
Densification slows down at the final stage of sintering because pores become highly stable. Castro’s group managed to break this stability by using pressure-assisted sintering with a punch designed to deform when the system reaches the final stage of sintering.
This spark plasma sintering (SPS) process, named deformable punch spark plasma sintering (DP-SPS), uses the high heating rates of SPS. However, uniaxial pressures from SPS are not enough to induce full densification without some level of grain growth, which can form grains larger than 10 nm.
Therefore, the team used a complaint punch to transfer transversal momentum to the grains, shifting contact angles—where pores and grain boundaries meet—and breaking the pores’ stability cages. The result is fully dense ceramics with unprecedentedly small grain sizes.
“Our results show that we can lower the sintering temperature to below 800°C, using nanoparticles as a starting material and a deformable punch in the die set that helps achieve full densification with minimal—truly minimal—grain growth,” Castro adds. “The method removes residual porosity, which is critical for optical applications, by sliding the grains instead of growing them during sintering. This means very small grains that are mostly limited by initial grain size rather than by processing conditions.”
Using a controlled chemical synthesis method, the UC Davis team densified nanopowders with 4-nm grain sizes into spinel samples with 7-nm grain sizes. The highly transparent sample can be used as strike face materials for transparent armor system and other applications that require transparency and high hardness.
The team measured an increase in hardness from 17.2 to 28.4 GPa—surpassing sapphire hardness—when it refined grain sizes from 188 to 7 nm, following a square-root function of grain size.
“The hardness for the nanospinel is higher than sapphire for any given plane, while being equally transparent,” Castro says. “Combined with the fact that the spinels are isotropic due to their cubic structure, in terms of shock resistance this nanospinel can offer better performance for sure.”
This behavior can be explained by a quasi-plasticity model that assumes load-induced deformation in ceramics is accommodated by grain shearing, which breaks (and reforms) bonds at grain boundary regions. Therefore, there is a correlation between strength of grain boundaries, their networking area, and room temperature macro-mechanical behavior.
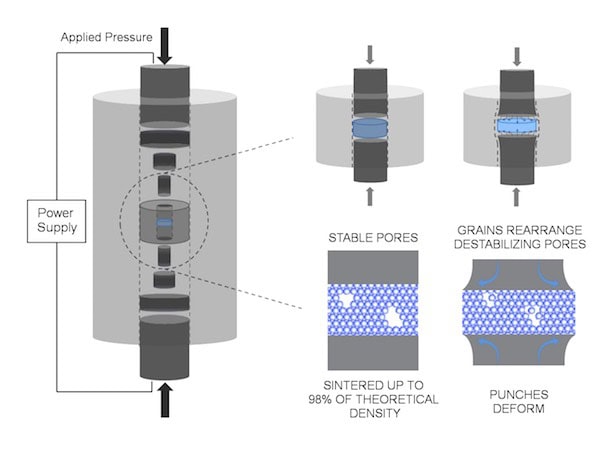
Credit: Nanoceramics Thermochemistry Laboratory
Correspondingly, an increased grain boundary network (small grains) should lead to more efficient intergranular cracking deflection, macroscopically representing an increase in hardness.
From this perspective, there should be no expected low grain size limit, except for when grains are so extremely small that there is loss of long-range ordering and the material is mostly amorphous.
DP-SPS has finally allowed production of such small-grained samples to prove this concept, suggesting contrary data are likely related to impurities and residual porosities.
Although tests mostly involved DP-SPS in spinel densification, the team suggests there is no reason to believe this method is exclusive to spinel densification. As long as deformation of the punch is set to occur at the ceramic’s final stages of sintering, the method can likely eliminate residual porosity as well.
The UC Davis team also successfully tested the technique for BaTiO3, suggesting the rise of a new generation of nanoceramics with truly nanoscale sizes (<10 nm) that may unveil the full potential of nanoceramics without porosity interference.
Moreover, while the process can allow densification of nanograined ceramics, it can also help densify micrograined samples—in particular those difficult to sinter to full densities.
“With this unprecedented sizes and fully dense samples, we can finally assess the nano-effects with great reliability, without interfering porosity. We have tested the compliant punch in other oxides now—achieving fully dense nanocrystalline samples is not exclusive for MgAl2O4. So, testing magnetic behavior, electric behavior, conductivity etc. can now be done without the inconvenience of contaminations, cracks, and other common sample problems in nanoceramics.”
“The secret is the compliant punch,” Castro says. “While at this point we are focused on the science behind this, I’m positive this can be scaled up. Once one can make thin nano-spinel discs, cutting them with a laser will be much easier than cutting sapphire due to its isotropic properties. Moreover, with higher hardness than sapphire, this can be a scratch-free surface that largely surpasses Gorilla Glass and sapphire for display applications as well.”
The paper, published in Materials Letters, is “Colossal grain boundary strengthening in ultrafine nanocrystalline oxides” (DOI: 10.1016/j.matlet.2016.10.035).
This work was sponsored by NSF DMR Ceramics, 160978.
Author
April Gocha
CTT Categories
- Material Innovations
- Nanomaterials