[Image above] ACerS member Ed Garboczi from the National Institute of Standards and Technology gives his invited talk at the workshop. Credit: Joe Biernacki
It’s true—3-D printing is revolutionizing materials processing. From printing glass to graphene aerogels, 3-D printing technology seems to be evolving at warp speed these days. Think micro-devices, electronics, turbine engine components, and automobile parts (and whole automobiles)—these are all being fabricated using additive manufacturing processes.
Innovators from industries that span everything from medical to aerospace are focusing on how to leverage this technology to take their products and solutions to the next level. And one industry (of many) where scaling up this technology is making considerable impact is the construction industry.
In the not-too-distant future, parts used to build new homes and buildings will likely be largely fabricated using 3-D printing machines.
The technology and basic science that will one day make it possible to print infrastructure-scale objects was the recent subject of a workshop sponsored by the National Science Foundation, called Combined Multiscale Modeling and Additive Manufacturing—Enabling Tools for the Engineering of Novel Infrastructure Materials, held at Vanderbilt University (Nashville, Tenn.), July 16–17.
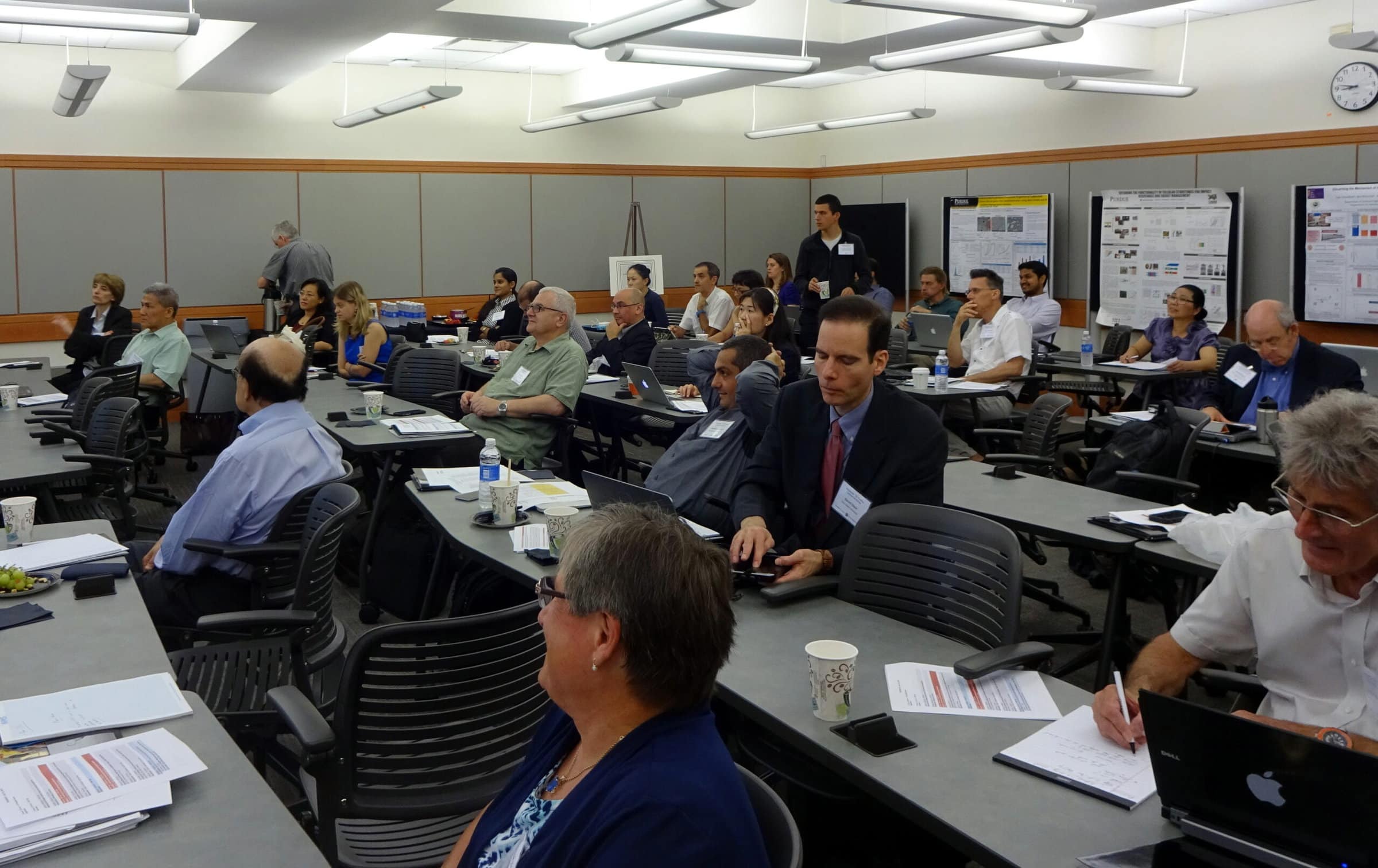
Attendees take notes during a presentation at the multiscale 3-D printing cement workshop, held at Vanderbilt University July 16-17. Credit: Joe Biernacki
Co-organized by fellow ACerS members Florence Sanchez, civil and environmental engineering professor at Vanderbilt; Jan Olek, from Purdue University’s (West Lafayette, Ind.) civil and environmental engineering program; and Joseph Biernacki, from Tennessee Technological University’s (Cookeville, Tenn.) chemical engineering program, the workshop brought together 32 individuals from a broad range of disciplines and backgrounds, including biomedical engineering, civil and chemical engineering, the Federal Highway Administration, NASA, and the National Institute of Standards and Technology.
The two-day event included a day of invited talks on the workshop’s four thematic areas: cement microstructure modeling, additive manufacturing processes and fabrication strategies, additive manufacturing and advanced modeling as tools for engineering materials, and 3-D printing of cement-based materials. Following the talks, a series of sessions focused on key scientific hurdles in the path to widespread commercialization of additive manufacturing of cement-based materials.
Those hurdles to commercialization are key, because the technology is already present for additive manufacturing with cement. Students are building their own backyard 3-D concrete printers.
And the same 3-D-printing mastermind that delivered this guitar earlier this year—Olaf Diegel, an engineering professor at Lund University in Sweden—has now also built a mobile concrete printer. In hopes of eventually being able to build houses on the fly, Diegel’s team has built a prototype that can conjure concrete chairs and public artwork anywhere.
Interested in learning more about the multiscale 3-D printing cement workshop? Check out Vanderbilt’s website.
Materials scientists and engineers: How do you see additive manufacturing revolutionizing the future of your respective industries? Share your field experiences with us in the comments!
Author
Stephanie Liverani
Spotlight Categories
- Division News
- Meeting Highlights
Divisions
- Cements