[Image above] Credit: Vee; Flickr CC BY 2.0
Scientists continue the mission to scale up synthetic spider silk—it’s been tough to spin fiber synthetically in the lab that rivals the impressive strength and durability of the real thing.
The real thing, however, is expensive and impractically slow to harvest. This video from the Oxford Silk Group in the Department of Zoology at Oxford University in England demonstrates just how tedious it is to harvest spider silk from spiders themselves.
Silk is pulled by tweezers from the spinnerets and attached to a spool with a dab of glue, after which a motor is started to begin harvesting. The group says it’s possible to harvest only about 30–80 meters of silk per session before the spider needs to be released back to its web to rest.
That’s quite an involved, time-consuming process—hardly scalable.
But scientists at Bolt Threads in Emeryville, Calif., have been working to develop a scalable way to create synthetic spider silk-like fibers using genetic engineering.
Back in June, we reported that the company finally made “meaningful progress” on the challenge of developing synthetic spider silk for commercial use—thanks in large part to the $40 million in investments and government grants it secured for the research, including a nice chunk of change from the National Science Foundation.
Since then, the company has been making good on its promise to put that funding to work and deliver a scalable, versatile solution for developing durable synthetic spider silk fibers.
Last week, MIT Technology Review reported the latest developments from the Bolt Threads laboratory, giving readers an inside look into the process that Bolt cofounders Dan Widmaier and David Breslauer and their team have been streamlining.
Take a look at the step-by-step process, complete with pictures.
The process works by using “genetically engineered yeast brew silk proteins that can be spun into fibers. The properties of those fibers can be altered by tinkering with the protein concentration and the temperature, tension, and other aspects of the spinning process,” MIT Technology Review reports.
And that versatility is important. “While synthetic fibers made from petroleum tend to be good at one thing, silk can be reengineered to suit diverse applications. Spiders themselves do this, fine-tuning their silk to make strong structural struts for their webs, sticky spots to capture prey, and a tough line to hang from,” according to the article.
The company tells MIT Technology Review that it expects the first products to use this synthetic silk fiber will be in consumer apparel—debuting as early as 2016—to prove the technology can be manufactured for large-scale industry applications.
But that’s just the beginning. “If we can get it to that scale, we can do anything.” Widmaier says in the article.
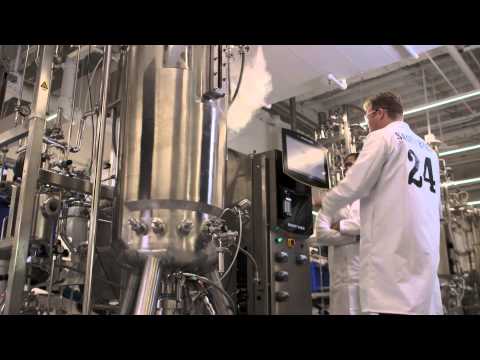
Bolt Threads is spinning the future of high-performance fabrics. Credit: Bolt Threads; YouTube
Author
Stephanie Liverani
CTT Categories
- Manufacturing
- Material Innovations