[Image above] Using viscoplastic fluid to support preceramic polymers during 3D printing could make the process technologically and economically feasible. Credit: Majid Minary, YouTube
Additive manufacturing of ceramics is a topic that continues to garner more interest every year. The opportunity it provides to save time and money during the prototyping stage of manufacturing is invaluable, so it is of little surprise there was standing room only during an additive manufacturing panel at Ceramics Expo last year.
Current methods of 3D printing advanced ceramics generally take place in one of three ways:
- Selective curing of a photosensitive resin that contains ceramic particles,
- Selective deposition of a liquid binder agent onto ceramic particles, or
- Selective fusion of a powder bed with a laser.
However, “All these techniques are limited by slow fabrication rates, and in many cases, a time-consuming binder removal process. By starting with powders, consolidation to a dense part is an almost insurmountable challenge, and residual porosity is typically unavoidable,” a Science article explains.
Instead of starting with ceramic powder, one idea that has gained interest in recent years is using preceramic polymers instead—the basis of polymer-derived ceramics.
Polymer-derived ceramics are a class of ceramics obtained by pyrolysis (thermal decomposition) of polymer precursors. For example, polycarbosilanes and polysiloxanes transform through pyrolysis to silicon carbide and silicon oxycarbide-type ceramics, respectively.
Compared to powder-based methods of ceramic fabrication, use of preceramic polymers allows fabrication of dense ceramics in near net shape without sintering. As such, polymer-derived ceramics hold great potential in commercial manufacturing applications, and the numerous research and development activities since the first reports of such ceramics in the 1960s have extended significantly the possible applications of polymer-derived ceramics.
(The September issue of the Bulletin features a look at some of the polymer-derived ceramic research currently taking place at the U.S. Naval Research Laboratory.)
In theory, polymer-derived ceramics should lend themselves well to additive manufacturing, as the polymer state is viscous and could presumably be ejected quite easily from a nozzle. However, preceramic polymers tend to have low viscosity, making it difficult to control flow of the material.
Currently, the main method for 3D printing polymer-derived ceramics is stereolithography, or methods in which a photosensitive resin is laid down layer-by-layer and cured using UV light. But stereolithographic fabrication of polymer-derived ceramics faces several limitations.
“Stereolithography is too slow for large scale applications. In addition, the method makes use of very expensive and a limited range of raw materials (photosensitive resins), while additional care must be taken owing to the environmentally hazardous solvents used to clean up parts,” Majid Minary says in an email.
Minary is associate professor of mechanical engineering at the University of Texas at Dallas. His lab conducts research on ceramic materials for composite applications, and since 2015, they have studied additive manufacturing techniques as well, mostly in regard to metals at micro/nanoscale for electronics and sensors.
About two years ago, Minary’s lab combined those two areas of research when they started work on 3D printing polymer-derived ceramics. “We were inspired by work in the biological community in printing hydrogels for tissue engineering applications as well as work for soft robotics,” Minary says.
In particular, Minary and his colleagues were inspired by studies like these ones that used viscoplastic fluids to provide support to liquid precursors during the 3D printing process.
Viscoplastic or “yield stress” fluids are materials that reversibly switch from a semisolid to a liquid state when subjected to sufficiently high shear stress. Such materials surround us in our daily lives, from mustard and hair gel in the home to heavy oils and fresh concrete in industry.
In the biological studies that used viscoplastic fluids for 3D printing, a nozzle was used to inject liquid precursors into containers filled with semisolid, gel-like viscoplastic fluids. The motion of the nozzle through the viscoplastic fluid caused shear stress, which led the fluid to liquify. Once the nozzle extruding the liquid precursor moved on, the viscoplastic fluid returned to a semisolid state, thus holding the liquid precursor in place until it could be cured and removed as a solid piece.
Minary and his colleagues were curious if viscoplastic fluids would support low-viscosity preceramic polymers as well. However, they knew that unlike the other studies, which used liquid precursors that cured at low temperatures, preceramic polymers require thermally induced curing at elevated temperatures over 120°C.
In a recent paper, Minary and his colleagues developed through an iterative process a viscoplastic fluid based on mineral oil and silica nanoparticles that could handle higher temperatures. Then, they used this fluid to support successful fabrication of polymer-derived silicon oxycarbide parts.
The three-step process used to fabricate the silicon oxycarbide (SiOC) parts, illustrated below, includes
- Injecting the preceramic polymer into the viscoplastic fluid,
- Curing the polymer at 160°C (while still in the fluid), and
- Removing the cured polymer from the fluid and placing it in a furnace to undergo pyrolysis at 900°C.
(The researchers note the process can be readily extended to other preceramic polymers, such as silicon carbide and silicon carbon nitride, and can be extended to ceramic composites as well by adding chopped ceramic fibers and/or functional nanoparticles.)
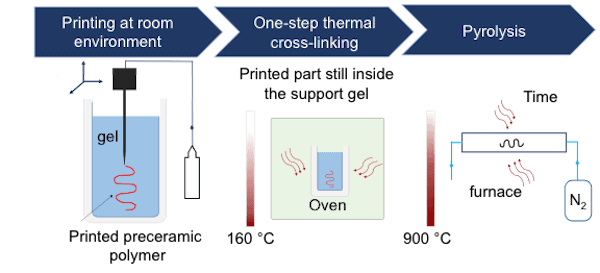
Illustration showing the process of 3D printing a polymer-derived ceramic using a viscoplastic fluid support bath. Reprinted with permission from Mahmoudi et al., ACS Applied Materials & Interfaces 2020, 12(28): 31984–31991. Copyright 2020 American Chemical Society.
A video uploaded to YouTube by Minary demonstrates the first part of the process happening in real time.
Credit: Majid Minary, YouTube
Minary says the success of this scalable process opens up “new opportunities for low-cost and high-speed production of complex 3-dimensional ceramic parts.” He adds they are now actively collaborating with a company and a national lab to expand this work to hypersonic and harsh environment applications.
The paper, published in ACS Applied Materials & Interfaces, is “Three-dimensional printing of ceramics through ‘carving’ a gel and ‘filling in’ the precursor polymer” (DOI: 10.1021/acsami.0c08260).
Author
Lisa McDonald
CTT Categories
- Manufacturing
- Material Innovations