[Image above] 3-D printed ceramic objects by Viridis3D on display at Ceramics Expo 2015. Credit: ACerS
Ceramic 3-D printing company Tethon 3D is making a big move to improve additive manufacturing of our favorite material—the company has filed a U.S. patent application for a new ceramic printer design that seeks to optimize additive manufacturing of ceramics.
“There has never been a powder-based 3-D printer designed specifically for ceramics before now,” says Karen Linder, co-founder, president, and CEO of Tethon 3D, in an email. “Tethon 3D developed Tethonite ceramic powder for 3-D printing and released it in 2014 to solve some of the problems encountered when 3-D printing ceramics. The new printer design that we filed the patent for this month is the next step in improving the ceramics 3-D printing industry.”
Tethon 3D’s new printer design incorporates compression into the additive manufacturing process. The company recently built a prototype design that “utilizes the compression plate to apply mechanical pressure to the entire build bed in repetitive motions at predetermined intervals,” Linder says in the email. “The result is a ceramic 3-D printed object that is stronger and more dense than was previously possible.”
Dense ceramics printed from the new printer design are a stark contrast to the last project we reported on from Tethon 3D—the light and airy CoolBrick the company developed earlier this year with Emerging Objects.
Akin to traditional ceramics, compression is the key to making a strong product. “The act of compression is essential for producing strong porcelain, stoneware, and earthenware 3-D printed objects, and this printer design could possibly also improve the production of objects printed in other powder materials,” Linder says in a PRweb news release.
Tethon 3D is still processing strength tests for the new 3-D-printed ceramics, but Linder says in the email that “early results are good.”
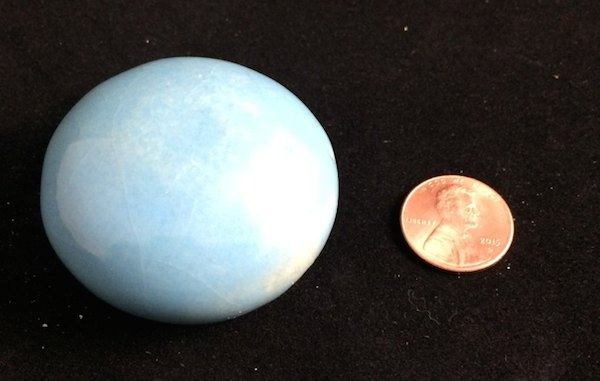
Adjustments have to be made to successfully print 3-D objects with compression. This object was 3-D printed with Tethon 3D’s new printer. The object was designed as a round sphere, so adjustments have to be made to achieve the desired shape and size. Credit: Tethon 3D
And, although compression seems like a complex addition to 3-D printing, Linder says that the addition adds minimal cost to the printer in terms of hardware. The company has already adapted printer software to address the challenges of adding compression.
“Additional printing time is required for the compression sequencing, so we shorted other processing steps to ultimately condense the overall length of time to create a ceramic 3-D printed object while improving its quality,” Linder adds.
After successful testing with the prototype printer, the company is now trying to patent the design and is evaluating business development partners for engineering and manufacturing of the new 3-D printer design, Linder says.
Although the timeline will depend on several factors, she adds that commercialization of the new 3-D printer could happen in as little as 12 months. We’ll stay tuned to provide you with the latest details.
Beyond 3-D printers for ceramics only, other companies are blazing forward with multimaterial additive manufacturing, too. Poland-based ZMorph manufactures a new 3-D printer with interchangeable heads that can print with a host of various materials.
According to a Product Design & Development article, “The machine uses the multi-fab heads to use different materials in quick succession or on the same project, and can perform 12 different functions, including laser cutting, CNC milling, 3-D-scanning, liquid printing, and liquid mold injection. In September, three more toolheads were introduced: a multi-material mixing extruder can blend plastics together, a generation IV thick paste extruder that can be used for food or ceramics, and a new integrated CNC milling toolhead provides high-powered professional milling.”
And the Collaborative Glass Robotics Laboratory—a joint initiative between Virginia Tech and Rhode Island School of Design—is expanding in a move to push 3-D printing of glass in new directions. The lab’s robotic glass printing method is “pushing the boundaries of material exploration and strategic process intervention,” according to a Virginia Tech news release.
See the robotic glass printing in action in the short video below.
Credit: NathanKing; Vimeo
Author
April Gocha
CTT Categories
- Glass
- Manufacturing
- Material Innovations