[Image above] Aircraft flies over Marie Byrd Land, West Antarctica. Credit: NASA Goddard Space Flight Center; Flickr CC BY 2.0
Researchers and scientists keep getting closer to understanding graphene’s future game-changing potential across many industries.
Here’s what we can expect to see from this unique, multifunctional material in the coming years, according to the latest research:
Better sound amplification. Researchers at the University of Belgrade, Serbia, have developed a graphene-based microphone that’s nearly 32 times more sensitive than microphones of standard nickel-based construction.
More sophisticated, cost-efficient night vision technology. Scientists at Massachusetts Institute of Technology are working to develop a flexible, transparent, and low-cost infrared vision system featuring graphene.
Heat flow management in electronics. Researchers from Rice University in Houston, Texas, suggest that 3-D structures of boron nitride—aka ‘white graphene’—could be an effective tunable material to manage heat flow in electronic devices.
Automotive, nuclear, and beyond. Chemists and materials scientists at University of Manchester in England are teaming up to revolutionize graphene’s many practical applications, including (but not limited to) use in fuel cells, hydrogen-based technologies like electric cars and air-powered generators, water purification, and even nuclear power plants.
But graphene’s reach doesn’t stop there.
Chemists from Rice University are now using the material to help heat surfaces and simplify ice removal. The team developed a thin coating of graphene nanoribbons in epoxy that is effective at melting ice on a helicopter blade—and that means it may be an effective real-time de-icer for aircraft, wind turbines, transmission lines, and other surfaces exposed to winter weather, according to a Rice University news release.
James Tour, chemist at Rice, and his team tested centimeter-thick ice from a static helicopter rotor blade in a –4°F environment. “When a small voltage was applied, the coating delivered electrothermal heat—called Joule heating—to the surface, which melted the ice,” the release explains.
“Applying this composite to wings could save time and money at airports where the glycol-based chemicals now used to de-ice aircraft are also an environmental concern,” Tour says in the release.
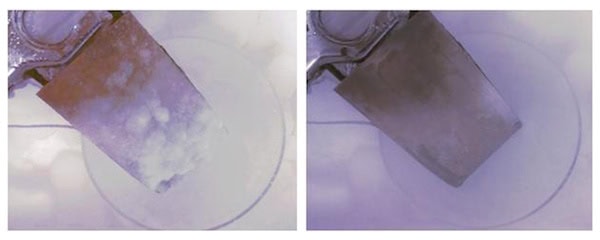
Rice University scientists coated graphene nanoribbon-infused epoxy on a section of helicopter blade to test its ability to remove ice through Joule heating. Credit: Tour Group; Rice University
The team, led by Rice graduate student Abdul-Rahman Raji, added graphene nanoribbons to a composite material where the nanoribbons comprised no more than 5% of the composite and spread a thin layer on a segment of helicopter rotor blade. Then the scientists replaced the thermally conductive nickel abrasion sleeve used as a leading edge on rotor blades and heated the composite to more than 200°F.
The team cranked the heat higher and found that the composite “remained robust in temperatures up to nearly 600°F,” according to the release.
“For wings or blades in motion, the thin layer of water that forms first between the heated composite and the surface should be enough to loosen ice and allow it to fall off without having to melt completely,” Tour says.
Given the coating’s durability and impressive heat resistance, this composite could protect aircraft from lightning strikes and provide an extra layer of electromagnetic shielding, according to Tour.
The research, published in the American Chemical Society’s Applied Materials & Interfaces, is “Composites of graphene nanoribbon stacks and epoxy for Joule heating and deicing of surfaces” (DOI: 10.1021/acsami.5b11131).
Author
Stephanie Liverani
CTT Categories
- Manufacturing
- Material Innovations
- Thermal management
- Transportation