[Image above] An example of fiberglass reinforced polymer being produced via pultrusion. Researchers led by Skolkovo Institute of Science and Technology believe pultrusion could be useful for producing shape memory polymer composites. Credit: Liberty Pultrusions, YouTube
Many of the materials that we talk about on CTT are designed to resist change. For example, environmental barrier coatings are expected to protect a gas turbine’s core materials from chemical attack and thermal degradation, and so must resist such influences themselves.
However, there are many applications in which adapting to the environment is more useful than resisting it. For instance, biomaterials that integrate with the body and flexible electronics embedded in pliable materials like clothing. For these applications, shape memory polymers, of SMPs, are of great interest.
SMPs are polymeric smart materials that can recover their initial shape under the influence of external stimuli, such as temperature, light, moisture, acidity, or electricity. SMPs are quickly making their mark on the materials world with applications in aerospace, biomedicine, the automotive industry, 4D printing, temperature sensors, and electronic devices.
A drawback of SMPs is their comparatively low tensile strength and stiffness, which can limit their application in demanding environments. Fortunately, researchers can improve the mechanical properties of SMPs by reinforcing the polymer matrix with various fibers, such as carbon, basalt, or glass.
Researchers have described several methods for producing SMP composites in the literature, including press molding, vacuum infusion, and 4D printing, among others. Yet surprisingly, the highly automated and continuous pultrusion process is not one of them.
In pultrusion, reinforcement fibers are impregnated with resin and then fed into a heated die where the resin is polymerized, after which the cured composite is cut to the required lengths.
Not only does pultrusion offer several benefits over traditional manufacturing processes—such as high production speed, low waste, and virtually indefinite length of the produced profiles—the final composites have a high volume fraction of reinforcement, thus ensuring excellent mechanical properties.
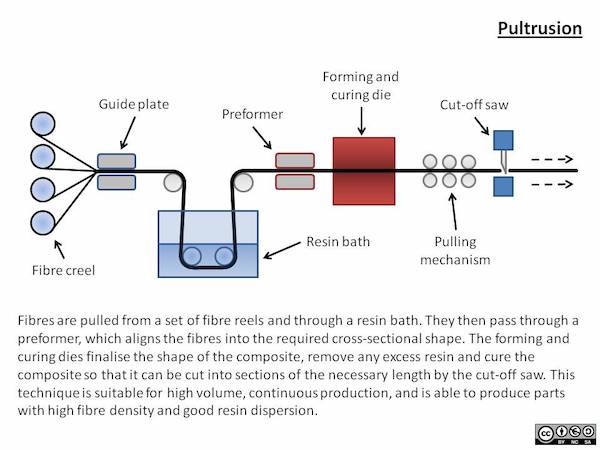
Diagram demonstrating the pultrusion process. Credit: CORE-Materials, Flickr (CC BY-NC-SA 2.0)
Based on these benefits, “it is believed that pultrusion can be successfully used to produce new types of shape memory structural components with unique combinations of geometries and mechanical properties,” researchers write in a recent paper.
The researchers come from the Skolkovo Institute of Science and Technology in Russia, plus a colleague from the University of Southern Queensland in Australia. They are led by assistant professor Alexander Safonov of the Skoltech Center for Design, Manufacturing, and Materials.
In an email, Safonov explains that they chose to investigate the potential of pultrusion via glass fiber reinforced epoxy-based composites for two reasons.
- Glass fiber reinforcement is much cheaper when compared to carbon fiber reinforcement, and thus is more often used in civil applications.
- Glass fiber reinforcement and its composites are better studied than those made of basalt fiber reinforcement.
They evaluated the shape memory performance of the pultruded composites via a series of bending tests on flat, rectangular specimens with either 0° or 90° fiber orientation.
Test results showed that the shape programming angle had no effect on the shape fixity and shape recovery ratios. In addition, the researchers established a linear relationship between the shape fixing angle and shape programming angle, allowing them to obtain the desired shape after programming.
“Considering these results, pultruded [SMP composites] show significant promise for structural applications based on shape memory composites,” they conclude. (See some pictures of the pultruded composites in the Skoltech press release.)
Safonov says that in the future, they plan to investigate the shape memory performance of full-scale structural members produced by the pultrusion process. “In particular, it is promising to develop composite structures without the use of bolted joints, i.e., the SMP composites will allow the use of high-performance snap-fit joints,” he says.
The paper, published in Composites Part A: Applied Science and Manufacturing, is “Shape memory behavior of unidirectional pultruded laminate” (DOI: 10.1016/j.compositesa.2021.106609)
Author
Lisa McDonald
CTT Categories
- Manufacturing