[Image above] Hummingbirds are the epitome of harnessing vibrations to achieve desirable outcomes. Energy researchers are looking to harness vibrations as well to generate electricity. Credit: Becky Matsubara, Flickr (CC BY 2.0)
With clear evidence of the role atmospheric carbon dioxide plays in the rapidly changing climate, many countries are committed to phasing out coal-fired power plants in favor of renewable energy sources. Even the G7 recently announced its intention to stop international funding for coal.
However, for this move away from fossil fuels to work, global energy conversion and storage capabilities must grow substantially. As Texas most notably illustrated, this year’s record cold and heat in the span of a few months already stretched current electricity resources beyond their limits—and such extreme weather is expected to become increasingly common.
Olivier Guillon, from RWTH Aachen University and Forschungszentrum Jülich GmbH, recently published a perspective on the role ceramic materials will play in expanding the energy conversion and storage infrastructure. He explains how the mechanical and chemical properties of ceramics, along with their direct thermal-to-electrical or mechanical-to-electrical energy conversion capabilities, make them superior materials for advanced energy applications.
One energy application for ceramic materials is piezoelectric energy harvesting (PEH). PEH converts mechanical motion, notably from vibration sources, directly into electricity. One of the most interesting applications of PEH is to provide small-scale, off-grid power for sensors and communications, such as pipeline monitoring in remote areas.
A PEH component consists of an active piezoelectric material fabricated onto or otherwise attached to a flexible metal substrate, typically steel, in disk “vibrator” or rectangular cantilever formats. Electrodes are attached to the PEH component to connect it to electrical testing fixtures and component assemblies. The image below shows a cantilever mounted in a forced-vibration test fixture.
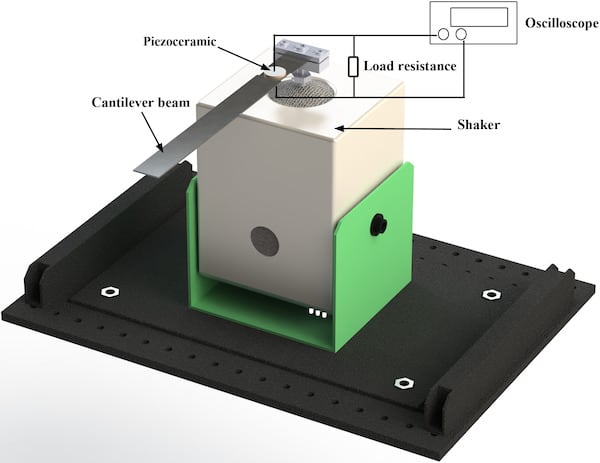
Schematic of an energy harvesting test system. Credit: Yan et al., International Journal of Ceramic Engineering & Science (CC BY 4.0)
Natural vibrations create strains in the active piezoelectric materials in a periodic fashion with both positive and negative voltages and currents, as shown in parts A and B, respectively, of the figure below. While there is some interest in alternating current (AC) power generation by piezoelectric harvesting, direct current (DC) device power sources are more applicable to the remote sensor applications. DC PEH devices are conceptually simple, as illustrated in the inset of part D.
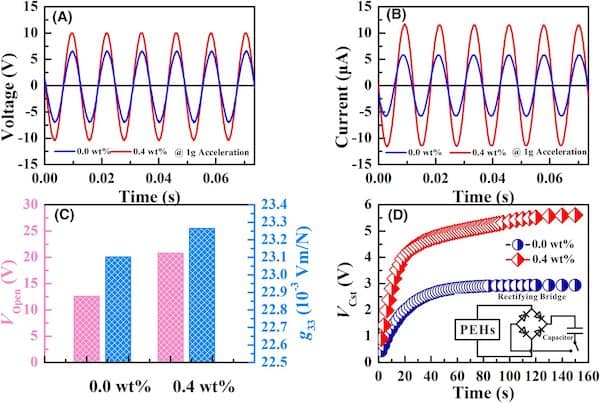
A) The open circuit output voltage and B) short circuit current for piezoelectric energy harvesters doped with samarium. C) Comparison of output voltage and g33 values of undoped and 0.4 wt.% Sm2O3-added 0.2PZN-0.8PZT ceramic. D) Charging curves of the electrolytic capacitor powered by x = 0.0 wt.% and x = 0.4 wt.% piezoelectric energy harvesters as a function of charging time. The inset in (D) is the schematic of the charging circuit for storing the electric power generated by the piezoelectric energy harvesters. Credit: Yan et al., International Journal of Ceramic Engineering & Science (CC BY 4.0)
The biggest challenges for PEH devices are
- Reducing or replacing lead in piezoelectric materials while achieving performance characteristics similar to lead-based materials, or at least within acceptable ranges for these applications.
- Fabricating the supported disk and cantilever components with good performance and longevity in a cost-effective and reproducible fashion.
From the articles that I read for this post, I gathered the following lists of key performance measurements for PEH devices. Feel free to email me at jforeman@ceramics.org with corrections or additions to improve this list.
- Piezoelectric coefficient (d): Relates force to charge; developed much like modulus relates stress (force) to strain (motion) in mechanical properties.
- Relative permittivity (ε): The factor by which the electric field between charges is decreased or increased relative to vacuum; is related to the capacitance/dielectric constant.
- Dielectric loss (often denoted by tan δ): A measure of energy “lost” (converted to heat), most commonly through charge conduction within a dielectric material and processes affecting dipole alignment and charge motion.
- Coupling coefficient (k): The degree of conversion from mechanical to electrical energy, most often measured through resonance evaluations.
- Figure of merit (FOM): A ratio of piezoelectric coefficient and permittivity, while some papers also include dielectric loss.
There are many additional quantities used to compare different materials and fabricated components, such as remnant polarization and electrostrictive coefficient. However, these quantities are not as ubiquitous across articles, and many are supportive and/or derived from the above key measurements.
The ideal material for PEH has high values for the piezoelectric and coupling coefficients while minimizing permittivity and loss. For better or for worse, these properties depend not only on composition but also on crystal structure, grain size, and density/porosity, among other properties, which in turn depend upon processing conditions. The ideal component optimizes mechanical, physical, and piezoelectric properties, but it must do so under conditions designed to fabricate components with good adhesion and shapes. Coupling factor is particularly dependent on component fabrication.
Recent papers in several ACerS journals discuss challenges and research into developing both materials and processes for PEH. These articles take on one or more of the following research challenges:
- Improving the performance of lead-based materials.
- Improving the performance of lead-free materials.
- Reducing sintering temperatures.
Improving piezoelectric properties through both smaller and larger grain sizes
An open-access paper by researchers at Beijing University of Technology explores doping lead-based PZN-PZT piezoceramics with samarium oxide to improve the piezoelectric response and control the grain size.
All samples were sintered at 1,200°C. They found that as more samarium was added, the grain sizes went down, from 2.5 micrometers to 1.5 micrometers with 0.7% added samarium oxide. The piezoelectric coefficient increased until 0.4% samarium was added, going against the generally accepted trend that larger grains have better piezoelectric properties.
The authors discovered similar trends in permittivity and polarization, and they attribute the high performance at 0.4% samarium to smaller ferroelectric domains in the doped structure and substitution of samarium for lead.
The open-access paper, published in International Journal of Ceramic Engineering & Science, is “Boosting energy harvesting performances of fine-grained piezoceramics by samarium doping strategy” (DOI: 10.1002/ces2.10088).
In contrast to the above study, a paper led by researchers at Brno University of Technology in the Czech Republic found the opposite trend when exploring compositional variations in barium calcium zirconium titanium oxides, which are lead-free piezoelectric materials.
The grain sizes increased from 15 micrometers to 90 micrometers while the piezoelectric coefficient peaked in the middle of the composition range tested. Importantly, they found the crystal structure varied from rhombohedral to orthorhombic to tetragonal as the calcium content increased.
Their very thorough evaluation discusses the many interrelationships among the measured quantities, with some comparing quite favorably to lead-based piezoelectric materials. However, the ceramics were all fired at 1,500°C, which is far too hot for component fabrication.
The paper, published in Journal of the American Ceramic Society, is “Composition driven (Ba,Ca)(Zr,Ti)O3 lead-free ceramics with large quality factor and energy harvesting characteristics” (DOI: 10.1111/jace.17497)
Investigating coating thickness on piezoelectric performance
In a paper published last July, researchers from France and Canada fabricated thick disks of lead zirconate titanate mixed with lithium, bismuth, and copper (LBC) oxides. They also screen-printed the same material as coatings on stainless steel cantilever supports and as free-standing films (by printing onto a polymer film).
The “LBC” sintering aid allowed the PZT to be cofired with electrodes at 900°C, which is a substantial reduction from the typical firing temperatures of 1,200°C or higher. This result is particularly useful for lead-based materials because lead begins to evaporate at about 800°C. While the thick disk density was close to theoretical with grain sizes around 3 micrometers, the printed PZT had 14–20% porosity and broader grain size distributions.
It is generally held that thicker piezoelectrics are needed for energy harvesting, though the authors found there can be too much of a good thing. Due to thermal mismatch, cantilevers with coating thicknesses greater than 55 micrometers had too much curvature to be useful.
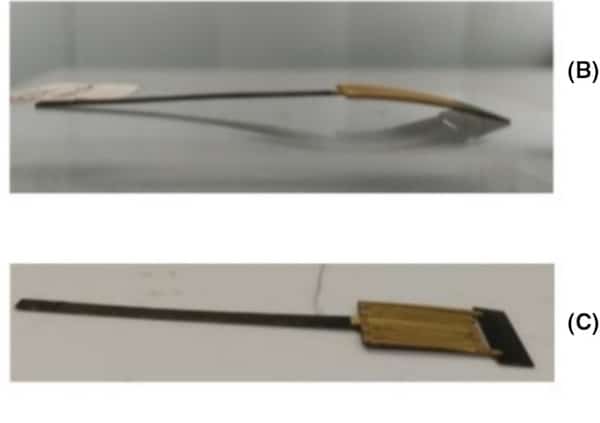
Top: Cantilever with 100 micrometer PZT coating. Bottom: Cantilever with 55 micrometer coating. Credit: Taborda et al., International Journal of Applied Ceramic Technology
The cantilever and free-standing film exhibited permittivity about half that of the thick disk, which should improve energy harvesting capability. However, this benefit is counteracted by dielectric loss values 10 times larger than for the thick disk. The authors attribute these changes to the greater porosity of the printed PZT.
Finally, the coupling coefficient for the cantilever is about half as much as the unsupported disk and film, which the authors attribute to the steel support.
The paper, published in International Journal of Applied Ceramic Technology, is “Key features in the development of unimorph stainless steel cantilever with screen-printed PZT dedicated to energy harvesting applications” (DOI: 10.1111/ijac.13588).
An open-access paper by researchers from the University of Cologne (Germany) and Grenoble Institute of Technology (France) brings together low-cost fabrication of components using lead-free lithium titanate.
Using sol-gel and spin coating technologies, the authors prepared coatings on steel cantilevers and compared performance to film thickness. Using a final firing temperature of 650°C, the researchers produced uniform films with small grains. The films had minor cracks, but no delamination was observed.
The results of the study somewhat surprised me—while the relative permittivity increased with increasing thickness, the piezoelectric coefficient held relatively steady. As a result, the Figure of Merit decreased with increasing thickness.
Though a high FOM is generally better for energy harvesting, the cantilever with the thickest coating (highest ε) produced the highest voltage, current density, and power density. Also, the authors observed leakage currents of decreasing orders of magnitude as thickness increased.
The authors conclude that their materials and methods show promise for large-scale fabrication of lead-free piezoelectric energy harvesting devices.
The open-access paper, published in Journal of the American Ceramic Society, is “Interdependence of piezoelectric coefficient and film thickness in LiTaO3 cantilevers” (DOI: 10.1111/jace.17606).
Author
Jonathon Foreman
CTT Categories
- Energy