[Image above] Credit: Materials Research Society; YouTube
According to a February 2017 report from Zion Research, the global rare-earth metal market was worth nearly $5 billion in 2014 and is projected to reach $9 billion by 2020. China is currently the top country producing rare-earth elements. In 2016, it exported 32,500 metric tons of the 105,000 metric tons it produced.
And the United States didn’t even make the list of the top rare earth producing countries last year. The U.S. Geological Survey tracks the U.S.’s net import reliance for mineral commodities every year. In 2016, the U.S. was fully reliant on foreign countries for 20 mineral commodities, including rare-earth elements (REEs).
Rare earths are crucial in the manufacture of high-tech devices—computers, rechargeable batteries, cell phones, cameras, magnets, aircraft engines, and more. The only rare earth mine in North America closed last year, leaving the U.S. completely reliant on imports.
That’s why back in September, the U.S. Department of Energy announced a shared funding initiative for nine projects with a goal of developing “cost-effective and environmentally benign approaches for the recovery of REEs from domestic coal and coal by-products.”
And one of these projects is apparently paying off. The DOE’s National Energy Technology Lab, which was managing these projects, recently announced that it has found high concentrations of REEs, greater than 300 parts per million, in coal samples that were taken from coal basins in Illinois, Northern and Central Appalachia, Rocky Mountain, and the Anthracite Coal Region of Pennsylvania.
“REEs are vital to the development and manufacturing of high-tech devices, such as computers, cell phones, and our national defense systems,” U.S. Secretary of Energy Rick Perry says in a DOE news release. “The current difficulties and high expenses associated with REE extraction has left the U.S. dependent on foreign REE imports. Supporting innovative research and development to establish efficient, cost-effective REE extraction methods is critical to our country’s energy and national security.”
The project involved a collaboration of industry and academia: West Virginia University, University of Kentucky, Tetra Tech, and XLight Corporation. Scientists found high REE concentrations after examining bituminous, subbituminous, and anthracite coal from the basins.
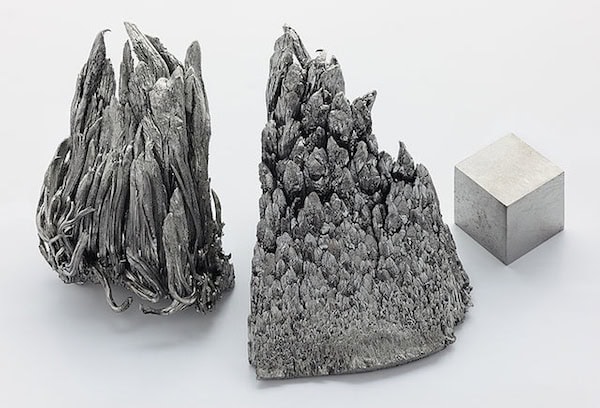
Yttrium sample. Credit: Museum für Naturkunde Berlin, Y_Yttrium_By Alchemist-hp_Wikimedia Commons; Flickr CC BY-NC-ND 2.0
REE concentrations of 300 ppm are critical for extracting REEs from coal to develop domestic supplies, according to the DOE release. The discoveries will enable scientists to develop feedstocks to aid in producing higher purity REEs.
Other DOE cost-sharing projects are in the works to recover REEs from coal basins across the U.S., including technology to recover REEs, acid mine drainage from bituminous mines as a feedstock, and a test facility to recover REEs from lignite, another type of coal.
It’s exciting to hear about initiatives that DOE is taking with business and academic partners to develop methods of recovering REEs from existing coal basins. The projects provide hope for the U.S. to end its dependence on imports for rare-earth materials.
To learn more about the DOE’s projects, visit this link.
Did you find this article interesting? Subscribe to the Ceramic Tech Today newsletter to continue to read more articles about the latest news in the ceramic and glass industry! Visit this link to get started.
Author
Faye Oney
CTT Categories
- Electronics
- Energy
- Environment
- Manufacturing
- Market Insights