[Image above] Credit: Mauro Cateb; Flickr CC BY 2.0
[Editor’s note: This report comes to us from Sanjay Sampath PhD, professor of materials science and director of the Center for Thermal Spray Research at Stony Brook University (Stony Brook, N.Y.).]
by Sanjay Sampath
Researchers from the Center for Thermal Spray Research (CTSR) at Stony Brook University have recently reported the ability to use thermal-sprayed ceramic deposits as templates for synthesis of ceramic–polymer composites with striking microstructural similarity and mechanical behavior similar to those observed in nacre (mother-of-pearl).
Nacre’s brick-and-mortar structure has a layered arrangement of CaCO3 ceramic tablets sandwiched with a thin biopolymer. This unique combination synergistically increases the material’s strength, stiffness, and toughness, significantly exceeding those predicted from rules of mixtures.
Accordingly, rich scientific literature has emerged to understand the fundamental natural design principles of nacre and to incorporate these into strategies for synthesis of tough composites. Approaches based on self-assembly, synthetic mineralization, layer-by-layer stacking, and ice templating via freeze casting have resulted in nacre-like structures and, in some cases, behavior.
However, although much progress has been achieved, key challenges remain in developing a scalable manufacturing process, while remaining true to the architecture and composition of the natural inspiration.
Using a rod flame spray ceramic deposition process, the team produced layered and porous templates with porosity of 10–14 vol%. An example of such a layered arrangement along with comparative structure of nacre is shown below.
The sprayed deposit is separated from the substrate, and the freestanding template is then infiltrated with a low viscosity epoxy mixture. The epoxy components infiltrate the channels, and curing results in a hybrid composite with 5–10 vol% porosity and dramatic improvements in strength and crack initiation toughness.
Values are shown in the Ashby-type plot below, along with data for natural materials and also some of the best data for synthetic composites reported in literature.
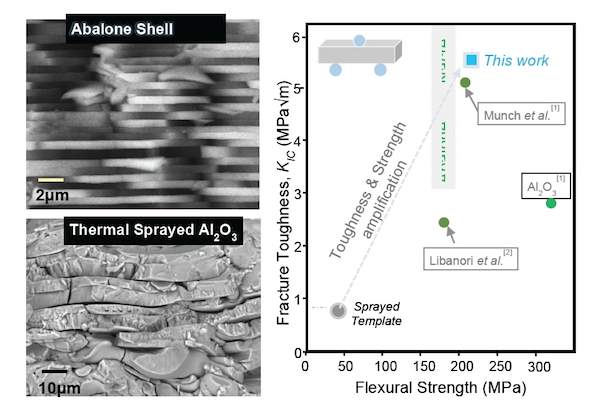
Micrographs of the layered structure of thermal-sprayed Al2O3, which mimics that of nacre (left). On the right, an Ashby-type map depicts the mechanical properties, fracture toughness, and strength of sprayed composites, which are similar to nacre and are higher than values reported in previous studies. Reprinted with permission from John Wiley and Sons.
The robust behavior is revealed in microstructural observation of the deformation zone, revealing several characteristics seen in nacre, including layer sliding and pull out, crack deflection, and branching. This initial data shows the technique is promising, with additional work underway to both refine template architecture (thinner platelets), more appropriate polymers, and enhanced infiltration techniques.
A unique attribute of this approach is the intrinsic scalability of the technology. Thermal spray is a widely used manufacturing process for deposition of metallic, ceramic, and cermet coatings across a range of industrial sectors—gas turbines, aerostructures, heavy machinery, semiconductor manufacturing, automotive, and biomedical implants.
Beyond material selection, the process also offers flexibility in compositional grading, both in-plane and through-thickness. Finally, the ‘mortar’ has numerous potential directions for design, including in-situ polymerization within templates, interface pretreatment, or even substitution of metals for higher temperature applications.
In addition to composite synthesis, natural design principles may also be contemplated—and more rapidly applied—for enhancing damage tolerance of protective thermal spray coatings. From a manufacturing perspective, there is precedent to use polymeric sealants to fill voids within porous spray coatings to prevent infiltration of potential corrodents.
One particularly promising direction for such a practice is in the reduction of damage from tribological contact or impact.
The team has also reported a multilayer concept in which a dense ceramic layer is applied by high-velocity thermal spray. The process produces a material that mimics the hard calcite layers on top of nacreous material.
In nature, the unique combination of tough followed by hard layers offers impact protection to shell animals from predator attack. However, a similar system also can be envisioned as a direction for future armor designs. Thermal spray is the only technique from which such ‘system-level’ biomimetic design can be achieved.
The paper, published in Advanced Materials, is “Bio-inspired hybrid materials from spray formed ceramic templates” (DOI: 10.1002/adma.201500303).
The work was supported by the National Science Foundation GOALI program through the CMMI division under award CMMI 1030942.
Contact: Sanjay Sampath, Distinguished Prof. and Director
Center for Thermal Spray Research
Department of Materials Science and Engineering
Stony Brook University, NY 11790
sanjay.sampath@stonybrook.edu
References
1. Munch, E., et al., Tough, bio-inspired hybrid materials. Science, 2008. 322(5907): p. 1516-1520.
2. Libanori, R., R.M. Erb, and A.R. Studart, Mechanics of platelet-reinforced composites assembled using mechanical and magnetic stimuli. Acs Applied Materials & Interfaces, 2013. 5(21): p. 10794-10805.
Author
April Gocha
CTT Categories
- Biomaterials & Medical
- Manufacturing
- Material Innovations