[Image above] 0.12 mm thick, 4 m wide—how can the float glass process create such a glass? Scientists at the State Key Laboratory for Float Glass in China describe how to determine parameters for the process in their new study. Credit: Shou et al., International Journal of Applied Glass Science/Wiley
Ultrathin glass, defined as glass with thickness under 0.5 mm, offers a number of benefits in many consumer and commercial applications, notably display glass for electronics and protective glass for photovoltaic solar panels.
As demand for these high-tech products grows, so does the need for ultrathin glass. According to a 2018 market survey by Energias Market Research Pvt. Ltd., the market for ultrathin glass is expected to grow by 10% per year over the next five years.
There are a number of commercial manufacturers of ultrathin glass, notably Corning, Schott, AGC, and Nippon Electric Glass. Most of these manufacturers use a gravity-based drawing process where the molten glass flows over or through tooling and is stretched as it drops through the air.
However, there are limits to the maximum width of glass sheets that can be formed by these processes, which place these processes at odds with the consumer electronics market demand for larger and larger screens. For example, Samsung has a 98-inch (diagonal) single screen TV available on its website. The display glass on this television is 2.2 m wide by 1.2 m high, dimensions that approach the maximum sheet width found on corporate websites. As screens continue to grow, so too does the need for more cost-effective, large dimension glass panel production.
The most common method for fabricating glass panels with large dimension is the float glass process. In this process, molten glass is floated on top of molten metal (usually tin) and then biaxially stretched using edge or top rollers. The float glass process has a large number of variables to control, including
- Temperature profile along the float bed;
- Length of the various zones in the process;
- Roller position, angle, number and speed; and
- Draw speed.
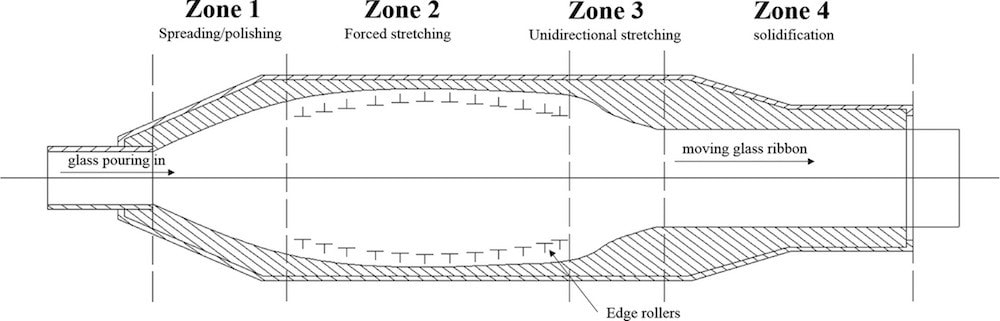
Schematic description of functions of tin bath in float glass process. Credit: Shou et al., International Journal of Applied Glass Science/Wiley
There is little information on determining parameters for a float glass process to manufacture ultrathin glass. Some researchers have developed models for producing ultrathin float glass and others have studied the surface properties of the ultrathin float glass. Few, if any, have coupled the analytical data to production-level experiments. Of the aforementioned manufacturers, AGC uses float glass processing, but they do not share information on their methods. This is completely understandable given the complexity of the process and competition in the market.
In a recent article published in the International Journal of Applied Glass Science, scientists at the State Key Laboratory for Advanced Technology of Float Glass in Bengbu, China, report an excellent float glass process to create ultrathin glass—while still retaining large dimensions!
In the study, the researchers provide an easy-to-understand description of the float glass process and processing variables. They base their study on theoretical relationships, such as mass and volume balance equations, and use engineering adjustments for temperature changes and the resulting viscosity changes.
The researchers explain the parameters required in each of the three shaping zones: initial flattening, biaxial stretching with the edge rollers, and uniaxial stretching to overcome thickening due to the viscoelastic nature of molten glass. Most interesting was their discussion on optimizing the number, angle, and speed of the rollers so that the linear acceleration of the molten glass stayed within its optimal ranges within the second processing stage.
Using the optimized parameters, the researchers produced 0.12-mm-thick glass sheets, nominally 4 m wide with 10% thickness variation across the middle 80% of the sheet. This reported width is substantially larger than widths listed on commercial suppliers’ websites.
The technology described in the article is now used at China Triumph International Engineering Co., Ltd. in their production of ultrathin float glass.
In a side note, Peng Shou, corresponding author of the article, has joined the International Journal of Applied Glass Science editorial board, according to Mario Affatigato, IJAGS editor-in-chief.
The paper, published in International Journal of Applied Glass Science, is “Continuous forming of ultrathin glass by float process” (DOI: 10.1111/ijag.13132).
Author
Jonathon Foreman
CTT Categories
- Glass
- Manufacturing