[Image above] An MIT team has achieved the thinnest and lightest complete solar cells ever made. To demonstrate just how thin and lightweight the cells are, the researchers draped a working cell on top of a soap bubble, without popping the bubble. Credit: Joel Jean and Anna Osherov; MIT
Editor’s note: This story originally appeared in print in the April 2016 ACerS Bulletin.
Will the world one day be entirely reliant on solar energy?
Advancements in photovoltaic research may be slow moving, but innovations will pay off in big ways when it comes to powering the future. Researchers have been busy developing new ways to increase solar cell efficiency in ways that are widely applicable and highly scalable.
A first-of-its-kind ‘green’ antenna that could double efficiency of solar cells, making them more affordable, made recent news.
Scientists are also developing solar cells that generate fuel instead of electricity—a promising potential replacement for fossil and other polluting sources of fuel.
And solar cells made from perovskites have been making news for their great potential for high efficiency and low cost—but more research needs to be done to scale up this technology for manufacturing use.
But solar cells really need to shed some bulk and gain flexibility if they’re ever going to be our go-to, ubiquitous power source.
Researchers at the Massachusetts Institute of Technology have developed a proof-of-concept for “solar cells so thin, flexible, and lightweight that they could be placed on almost any material or surface, including your hat, shirt, or smartphone, or even on a sheet of paper or a helium balloon,” according to an MIT press release.
The real deal may be years away from large-scale development, but this new approach to making solar cells could be key in powering the next generation of portable electronic devices, the release explains.
MIT professor Vladimir Bulović, research scientist Annie Wang, and doctoral student Joel Jean say the key is to make the solar cell, the substrate that supports it, and a protective overcoating to shield it from the environment all in one process, according to the release.
“The innovative step is the realization that you can grow the substrate at the same time as you grow the device,” Bulović says.
The single-process approach means that the substrate isn’t handled, cleaned, or removed from the vacuum during fabrication, drastically minimizing any exposure to contaminants that might degrade performance.
For both the substrate and the overcoating, the team used a common flexible polymer called parylene—a commercially available plastic coating used to protect implanted biomedical devices and printed circuit boards from environmental damage—and an organic material called DBP as the primary light-absorbing layer, the release explains.
And, unlike conventional solar cell manufacturing, which requires high temperatures and harsh chemicals, this process takes place in a vacuum chamber at room temperature and sans solvents. Both “the substrate and the solar cell are ‘grown’ using established vapor deposition techniques,” the release explains.
The materials used in this proof-of-concept were just examples—the in-line substrate manufacturing process is the key innovation, the team emphasizes.
“Different materials could be used for the substrate and encapsulation layers, and different types of thin-film solar cell materials, including quantum dots or perovskites, could be substituted for the organic layers used in initial tests,” the scientists explain.
For the proof-of-concept, the team used a flexible parylene film—only one-tenth as thick as traditional kitchen cling wrap—and deposited it on glass, a more sturdy carrier material. Mastering clean separation of the thin material from the glass was particularly challenging, explains Wang, who has many years’ experience working with parylene.
After fabrication, the scientists lifted the entire parylene/solar cell/parylene stack off the carrier using a frame made of flexible film.
The final ultra-thin product is just one-fiftieth the thickness of a strand of human hair and one-thousandth the thickness of equivalent cells on glass substrates—which are about two micrometers thick. Yet, “they convert sunlight into electricity just as efficiently as their glass-based counterparts,” says the team.
The researchers demonstrated just how thin these thin solar cells are by draping a working cell on top of a soap bubble without popping the bubble.
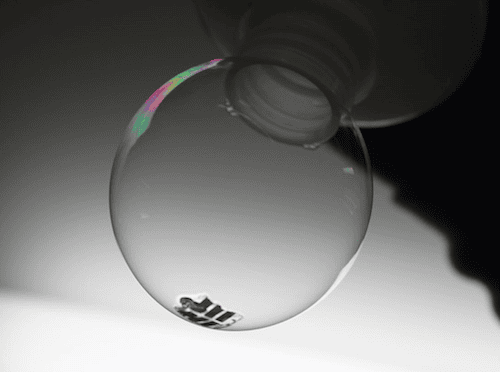
“It could be so light that you don’t even know it’s there, on your shirt or on your notebook,” Bulović says. “These cells could simply be an add-on to existing structures.” Credit: Joel Jean and Anna Osherov; MIT
That’s impressively thin—but is it too thin to be practical?
“Parylene films of thicknesses of up to 80 micrometers can be deposited easily using commercial equipment, without losing the other benefits of in-line substrate formation,” the team says.
The time it will take to scale-up this material is still up in the air, but this work could be a new frontier in the solar power revolution.
“We have a proof-of-concept that works,” Bulović says. “The next question is, how many miracles does it take to make it scalable? We think it’s a lot of hard work ahead, but likely no miracles needed.”
The research, published in Organic Electronics, is “In situ vapor-deposited parylene substrates for ultra-thin, lightweight organic solar cells” (DOI: 10.1016/j.orgel.2016.01.022).
Author
Stephanie Liverani
CTT Categories
- Energy
- Material Innovations