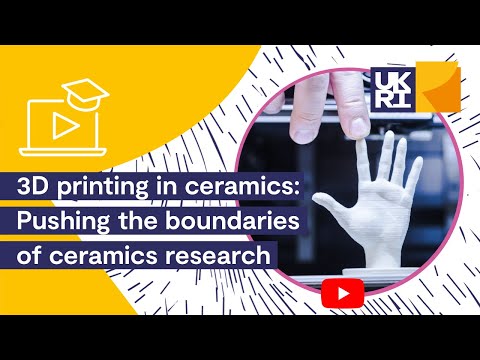
Credit: AHRCPress; YouTube
Gizmag has a new story by David Szondy about research on 3D rapid-prototype printing of ceramic objects at University of West England, Bristol and a new grant the school has received to explore the use of faience as a possible way to reduce manufacturing time of commercial ceramic products.
A point needs to be clarified first. By faience, Szondy and UWE Bristol are referring to what they describe as a self-glazing, non-clay paste developed (or at least used) in ancient Egypt composed of quartz or sand, calcite lime and a mixture of alkalis, rather than the more contemporary tin-glazed earthenware (see this for an example) that goes by the same name.
The work is being done at UWE, Bristol’s Center for Fine Print Research. Stephen Hoskins, featured in the above video, is director of the center and a professor at the university.
Hoskins and his center are mainly coming at this from an “arts” point of view and apparently are working with manufacturers of tableware to see how the 3D-printing processes can increase speed-to-market rates for new designs.
Even with the arts focus, a couple of things interest me about the story and video. First, this is the first time I have come across a discussion of any thoughts about applying faience-like technology to things like tableware, but the attraction quickly becomes obvious: The use of a faience paste would eliminate the two-step firing process (bisque followed by glaze firing). Also, the video itself is one of the better explanations and demonstrations online of 3D/rapid prototype printing/additive manufacturing.
However, I am not sure I agree with Hoskins’ views on how long it will take before 3D printing can be decentralized. Hoskins apparently acknowledges that the technology will be highly disruptive, but Szondy quotes him predicting that it will take 15 years for decentralized manufacturing of custom ceramic parts to become commonplace, a figure that he repeats in the video.
I don’t have a crystal ball, but three factors are going to make decentralized printing of not only ceramics, but also metals, glass, semiconductor circuits, organics, hybrids, etc. happen much faster: 1) the military wants the capability ASAP (if it doesn’t have much of it already); 2) there is already a lot of public and private investment going into efforts to bootstrap advanced additive manufacturing in the United States and elsewhere; and 3) the technology seems to be very hackable, and we have already covered the explosion of low-cost, low-tech approaches that are available online, even for complex shapes.
Some of this may be semantics and what is meant by “decentralized.” For comparison, if one looks at the timeline for the growth of desktop publishing, high-quality desktop typesetting and design quickly spread from research to typesetting houses (remember those?), which could afford high-resolution film printers. This stage was rapidly followed by quick-print shops (remember Kinkos?) that were able to produce high-resolution graphics for a fraction of the cost of typesetters. Eventually, everyone could afford high-resolution printers for small-run jobs and direct-to-printer services for larger runs. That only took about ten years and (arguably) affected a relative narrow range of businesses.
Some materials are going to be more quickly adapted to 3D printing than others, but additive manufacturing will disrupt and transform nearly every type of manufacturing (from electronics to medical devices to weapons), and there are tremendous sums being wagered on who the winners and losers will be. And, as is oftentimes the case, the first wave of winners may be determined by who is first-to-market rather than whether it’s the best technology.
CTT Categories
- Electronics
- Manufacturing