[Image above] Researchers from Korea experimented with applying ultra-high temperature ceramic (UHTC) coatings to composites using a vacuum plasma spray (VPS) process. Credit: Kang et al., Materials (CC BY 4.0)
In the April issue of ACerS Bulletin, ceramics took to the skies as parts within next-generation aircraft. While some articles focused on developing ceramic matrix composites (CMCs) for use in jet engines and “super” turbines, other articles focused on using ceramics as environmental barrier coatings on CMCs to increase resistance to ablation and oxidation.
Another area of research that has received increasing attention of late—and the focus of this month’s Deciphering the Discipline column—is ultra-high temperature ceramics (UHTCs). UHTCs are a class of refractory ceramics that have high melting temperatures and good thermal properties, which make them ideal to protect against ablation and oxidation in high-speed aircraft.
Among UHTCs, zirconium carbide (ZrC) is particularly promising. ZrC has a melting point over 3,400°C, its density is relatively lower than other refractory carbides, and it exhibits no phase changes in the solid state.
Despite these desirable properties, conventional methods for coating a composite with ZrC leave something to be desired. As explained by researchers of a recent open-access study, “[Chemical vapor deposition of ZrC] is complex, expensive, time-consuming, and hazardous to the environment. An alternative low-cost method is chemical vapor infiltration … however, it has the disadvantage of low efficiency.”
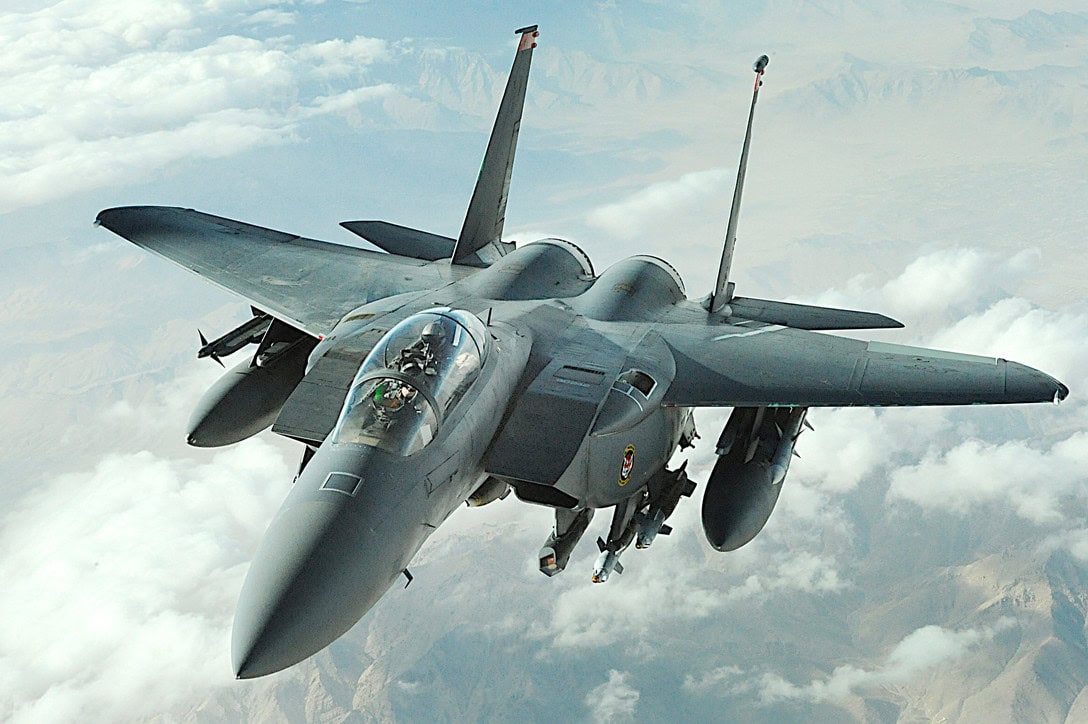
As we push aircraft to achieve faster and faster speeds, we need protective coatings that will keep them safe from ablation and oxidation. Credit: U.S. Air Force photo (of an F-15E Strike Eagle), Staff Sgt. Aaron Allmon
The researchers of the open-access study come from two places in Korea: the High-enthalpy Plasma Research Center at Chonbuk National University and the Agency for Defense Development in Daejeon. And in their study, they looked at the efficacy of a different coating method—vacuum plasma spray (VPS).
VPS works by injecting metal or ceramic powders into a hot gas plasma, which melts the powders. These molten droplets are then projected onto a substrate to form a coating. During the coating process, the VPS spray chamber is filled with an inert gas and maintained at low pressure, ensuring no oxidation takes place.
In their paper, the researchers explain they chose to study VPS as a potential alternative to chemical vapor deposition and chemical vapor infiltration because “plasma spraying … is economical and can be easily applied on an industrial scale.” Additionally, “VPS coatings … [have] high purity with low porosity and high deposition rate without the formation of oxides.”
Velocity and temperature of the VPS plasma jet are closely associated with phase change, thickness, and porosity of the coating. As such, the researchers’ goal in the recent ZrC study was to investigate how the discharge current (which controls plasma jet velocity and temperature) affects a ZrC coating on carbon/carbon (C/C) composites.
Prior to coating their C/C composites with ZrC, the researchers fabricated a thick silicon carbide layer on top of the C/C composites to reduce the difference in thermal expansion coefficients between ZrC and the C/C composites. During the VPS process, they used argon and helium as the plasma forming gases.
To test resistance to ablation, the researchers placed coated and uncoated samples under a high-pressure flame generated by a diamond jet gun for 30 seconds. The ablation tests were conducted in open air, and maximum surface temperatures of the coated and uncoated samples measured 2,052°C and 2,275°C, respectively.
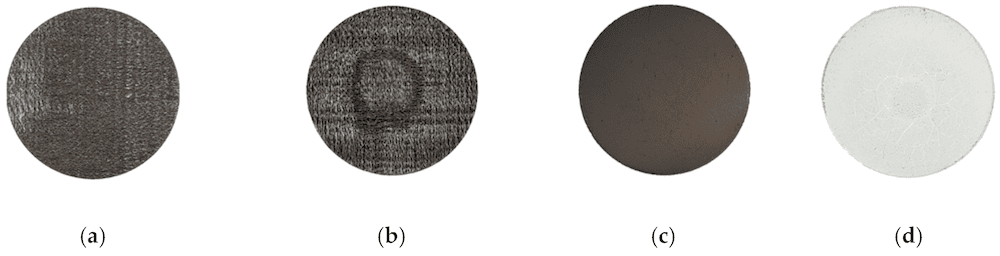
Uncoated (a, b) and coated (c, d) samples prior to (a, c) and after (b, d) the ablation test. In the uncoated composite, the center was subjected to maximum ablation. In the coated composite, surface color changed from black to white following oxidation. Credit: Kang et al., Materials (CC BY 4.0)
The researchers found that the sample without coating decreased weight by 0.95 grams, while the coated sample’s weight and thickness increased by 0.8 g and 113 µm, respectively. They attributed this finding to oxidation of ZrC into ZrO2 along the outer surface.
Looking closer, they found cracks and pores on the coated sample’s surface following ablation, likely due to the ZrO2 undergoing two phase changes during the high heat and subsequent cooling following the ablation test. Regardless, “it is clear that the ZrO2 protective film on the surface of the coating layer effectively prevents oxygen diffusion from ZrC to the C/C composite,” the researchers note in the paper.
In their conclusion, the researchers summarize the effectiveness of the VPS technique for coating composites. “The coating process using VPS effectively protected a C/C composite in an ablation environment; moreover, a detached coating was not detected between the ZrC coating and substrate, indicating good adherence between them.”
The open-access paper, published in Materials, is “Characteristics of ZrC barrier coating on SiC-coated carbon/carbon composite developed by thermal spray process” (DOI: 10.3390/ma12050747).
Author
Lisa McDonald
CTT Categories
- Aeronautics & Space
- Thermal management