[Image above] This isotropic, neodymium–iron–boron bonded permanent magnet was 3-D-printed at DOE’s Manufacturing Demonstration Facility at Oak Ridge National Laboratory. Credit: ORNL
Innovations in 3-D printing continue to evolve, with companies like auto manufacturer Local Motors planning to drive mass production of 3-D printed cars through this year.
The evolution doesn’t stop there—it seems like there’s nowhere additive manufacturing won’t go. From 3-D printed concrete to electronics to glass, this technology is changing how we manufacture materials.
And when it comes to the future of the rapidly changing manufacturing industry, waste reduction and a more mindful approach to environmental impact are paramount concerns.
Researchers at the Department of Energy’s Oak Ridge National Laboratory (ORNL) in Oak Ridge, Tenn., are focused on using 3-D printing to create permanent magnets that outperform conventional versions—a process they say can help preserve the rare materials used to create those standard magnets.
Magnets are widely applicable—they’re used in everything from data storage to sound production to MRIs. So producing magnets in a way that reduces waste without sacrificing efficacy is important.
ORNL researchers say they’ve created permanent magnets produced by 3-D printing using the Big Area Additive Manufacturing (BAAM) machine that can “outperform bonded magnets made using traditional techniques while conserving critical materials,” according to an ORNL press release.
“While conventional sintered magnet manufacturing may result in material waste of as much as 30–50%, additive manufacturing will simply capture and reuse those materials with nearly zero waste,” ACerS member Parans Paranthaman, principal investigator and a group leader in ORNL’s Chemical Sciences Division, says in the release.
ORNL’s 3-D printing process is designed to conserve neodymium and dysprosium—rare-earth elements that are mined and separated outside the U.S., the release explains. Neodymium magnets are the most powerful on earth and used in everything from computer hard drives and head phones to clean energy technologies, such as electric vehicles and wind turbines.
“The 3-D printing process not only conserves materials but also produces complex shapes, requires no tooling, and is faster than traditional injection methods, potentially resulting in a much more economic manufacturing process,” Paranthaman adds.
The study, published in Scientific Reports, is “Big area additive manufacturing of high performance bonded NdFeB magnets” (DOI: 10.1038/srep36212).
Check out the video from ORNL to learn more about the process!
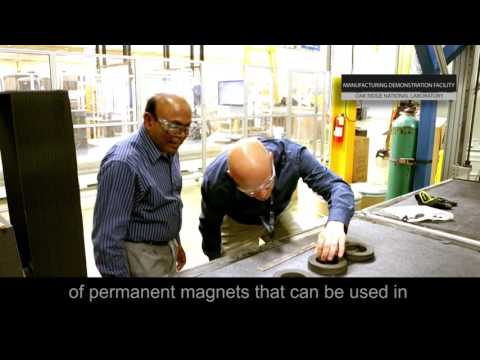
Credit: Oak Ridge National Laboratory; YouTube
Author
Stephanie Liverani
CTT Categories
- Electronics
- Energy
- Manufacturing
- Material Innovations