[Image above] Using stereolithography, engineering company Sandvik successfully created a 3D-printed diamond composite. Credit: Sandvik, YouTube
I look forward to the Met Gala every year with a mixture of fascination and horror to see what bizarre outfits the celebrities will wear. This year was no exception, but a few outfits in particular caught my eye—the dresses and accessories designed by Zac Posen.
The theme of Met Gala 2019 was “Camp: Notes on Fashion,” in honor of American writer Susan Sontag’s 1964 essay that defines camp as “love of the unnatural: of artifice and exaggeration.” Though Posen’s dresses may not have been as exaggerated as some of the outfits on display, his creations were certainly “unnatural”—instead of plant- and animal-based textiles, Posen used plastics and metals to 3D-print his designs!
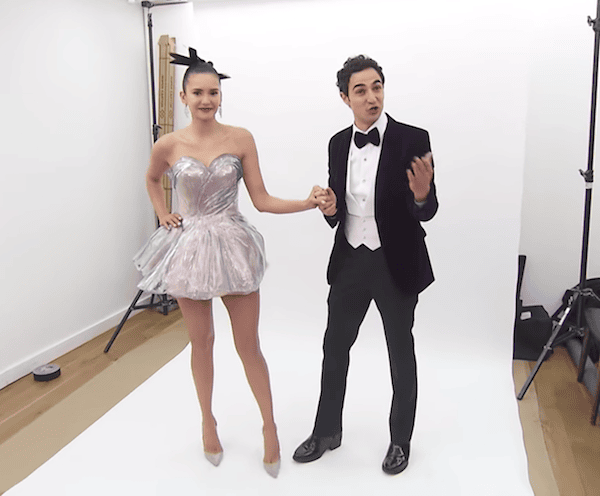
Canadian actress Nina Dobrev poses with American fashion designer Zac Posen in the 3D-printed dress he created for her to wear at the 2019 Met Gala. Credit: E! Red Carpet & Award Shows, YouTube
Industry frequently discusses 3D printing in manufacturing contexts, but additive manufacturing (AM) offers attractive possibilities to many other spheres as well, including fashion. That is because challenges faced by manufacturers—for example, creating complex, specialized shapes—are challenges also inherent to other fields.
Engineering company Sandvik is one company that has demonstrated AM’s potential for applications outside manufacturing. I wrote on CTT in May about their project creating a 3D-printed guitar, which shows one way AM can affect the music industry.
Now, a new project by Sandvik demonstrates an AM application desirable to the manufacturing industry—but likely of equal interest to the fashion industry as well.
As the hardest of the (common) naturally occurring substances, diamond is a material desirable in both jewelry and industrial applications due to its high strength, resistance to chemical corrosion, and broad optical transparency. However, because diamond is so hard, it is almost impossible to form diamond into intricate, complex shapes.
In new research, Sandvik has developed a proprietary process based on the AM technique stereolithography to create 3D-printed diamond composites—meaning we can now print this super hard material in complex shapes!
A Sandvik article explains that although most of the material is diamond, the diamond needs to be cemented in a very hard matrix to make it printable. Mikael Schuisky, head of R&D and operations at Sandvik Additive Manufacturing, elaborates, “We are printing in a slurry consisting of diamond powder and polymer using a method called stereolithography, where complex parts are produced, layer by layer, using ultraviolet light.”
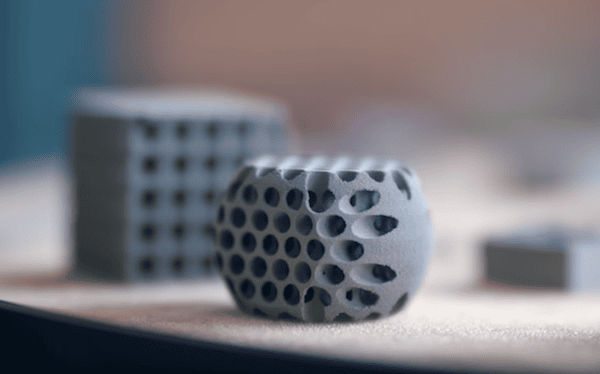
An example of the complex shapes that can be formed with Sandvik’s 3D-printed diamond composite. Credit: Sandvik, YouTube
Although this process supposedly keeps “the most important physical properties of pure diamond,” it appears sparkle was left off that list.
Without translucency, this first 3D-printed diamond composite will likely shine in industrial applications more than jewelry (Ocean’s 8 was a bit much to expect on a first round). However, this first example does not mean 3D-printed diamond composites will always be opaque.
As mentioned before, Sandvik used stereolithography to create their diamond composite, so it is possible that development of a special resin could result in a future diamond composite that is translucent as well—an innovation for which I am sure Zac Posen will keep a lookout.
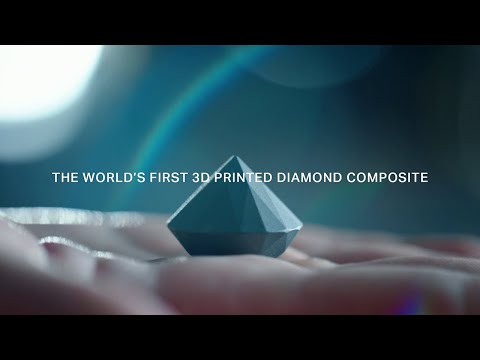
Credit: Sandvik, YouTube
Author
Lisa McDonald
CTT Categories
- Manufacturing
- Material Innovations
Spotlight Categories
- Member Highlights