[Image above] An infographic showing the five-step pyrometallurgy process developed by Nissan and Waseda University to recover rare-earth compounds from electric vehicle motor magnets. Credit: Nissan
As more electric vehicles hit the roads every year, the question of what to do with the batteries when they reach end-of-use grows as well.
The question stems in part from the fact that improper disposal can contribute to water and air pollution. However, an increasing focus is on the critical materials within batteries as well.
Critical materials are materials with high economic importance but also high supply risk. Electric vehicle batteries often contain several critical materials, such as lithium, cobalt, and bauxite. As demand for electric vehicles increases, manufacturers worry about securing enough critical materials to fabricate the batteries.
Governments and industry are putting money into an array of research initiatives to improve battery recycling and recovery of critical materials. For example, the U.S. Department of Energy launched the ReCell Center to coordinate studies by scientists in academia, industry, and at government laboratories on advanced battery recycling. Across the pond, the Faraday Institution in the United Kingdom is coordinating the Recycling of Lithium-Ion Batteries (ReLiB) project to safely and economically manage the materials contained in lithium-ion batteries at the end of their life.
Batteries are not the only component of electric vehicles that contains critical materials, however. At the heart of many electric vehicle motors are strong magnets made from the rare-earth metal neodymium, yet less attention has focused on developing methods to effectively recover this critical material.
Nissan Motor Co., Ltd. and Waseda University are an exception. Since 2017, Nissan has collaborated with Waseda University on recovering rare-earth compounds from electric vehicle motor magnets. This month, the two collaborators announced they started testing a jointly developed recycling process.
The five-step pyrometallurgy process that they developed involves:
- Adding a carburizing material and pig iron to the motor, which is then heated to at least 1,400°C so it can begin to melt.
- Adding iron oxide to oxidize the rare-earth elements in the molten mixture.
- Adding a small amount of borate-based flux to the molten mixture. (This flux is capable of dissolving rare-earth oxides even at low temperatures.)
- Wait for the molten mixture to separate into two liquid layers: the top layer, which contains the molten oxide (slag) with rare-earth elements; and the bottom layer, which contains higher density iron–carbon alloy.
- Recover the rare-earth elements from the slag.
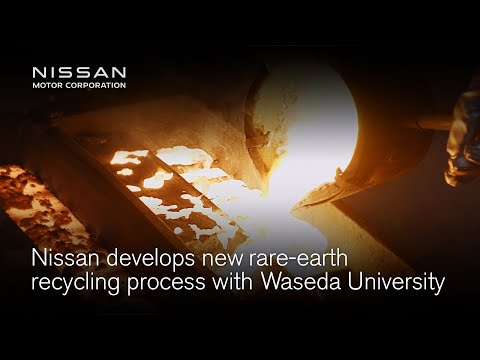
Credit: Nissan, YouTube
According to the Nissan press release, the process can recover 98% of the motors’ rare-earth elements. “This method also reduces the recovery process and work time by approximately 50% compared to the current method because there is no need to demagnetize the magnets, nor remove and disassemble them,” the press release continues.
Nissan and Waseda plan to continue their large-scale facility testing, with the aim of developing the process into a practical application.
Author
Lisa McDonald
CTT Categories
- Electronics
- Manufacturing
- Transportation