[Image above] A prototype rail bogie created out of surplus and recycled carbon fiber materials was unveiled at the University of Huddersfield in 2019. Credit: University of Huddersfield
From aerospace to sports equipment, glass and carbon fiber-reinforced polymers are rapidly making their mark in numerous industries.
These composites are used to replace traditionally metal parts so that a device retains its strength while weighing considerably less. However, the upfront cost of fiber-reinforced composites can be significantly more than for metal, so the investment is not always worth it for certain sectors.
The rail industry is one sector that has been much slower to adopt fiber-reinforced composites compared to other transportation industries. Though glass fiber-reinforced polymers have appeared in limited semistructural applications such as railcar passenger doors and seat shells for decades, use of advanced fiber composites in major structural components remains scarce.
However, with passenger and freight activity expected to more than double by 2050, the role of rail in global transport is gaining attention because of its potential to help reduce energy use and environmental impacts associated with transport.
As such, investing in the development of major structural components made from fiber-reinforced composites is becoming more profitable for rail companies. And as explained in an Ingeniería Civil article, railcar bogies are the focus of several notable studies in the past decade.
Bogies are the structure underneath a railway vehicle body to which axles and wheels are attached through bearings. If fiber-reinforced composites are used instead of traditional metal alloys for bogies, the considerable weight reduction could reduce track wear and infrastructure maintenance costs by reducing vertical and transverse loads on the rails.
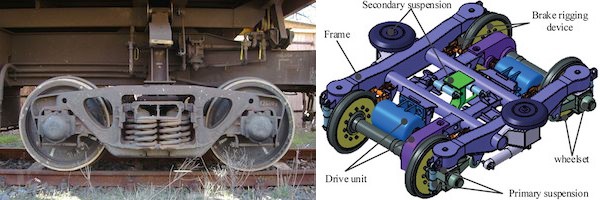
Left, picture of a rail bogie. Right, schematic illustrating the parts of a rail bogie. Credit: (Left) Ketamin, Wikimedia; (Right) Zhang et al., International Journal of Production Research (CC BY-NC-ND 4.0)
Below is a short timeline of recent advancements on fiber-reinforced rail bogies.
2012: Eureka 1841 Eurobogie project explores bogies containing glass fiber composites
Eureka is an intergovernmental organization that coordinates and funds international cooperation for innovative R&D projects. In 2012, partners in the Eureka 1841 Eurobogie project, which focused on advanced rail suspension using fiber-reinforced plastics, reported results from tests on a glass fiber composite rail bogie. They said the experiment not only showed feasibility of the component design but also achieved satisfactory component strength as well as good manufacturing parameters using the resin transfer molding method.
2014: efWING features first use of carbon fiber composite in bogie frame
Since 2011, Japanese manufacturer Kawasaki Heavy Industries Ltd. has worked to develop a carbon fiber composite leaf spring, which is a basic form of suspension used in train bogies. The company conducted a running test of the composite spring in 2012 and received a Good Design Award for the new product, called efWING, in 2013.
In 2014, Kumamoto Electric Railway Co. Ltd. brought the composite into commercial operation when the company replaced two conventional bogies with efWING bogies (see video below). Since then, other railway companies including Shikoku Railway Co., Kyushu Railway Co., and Nishi-Nippon Railroad Co. Ltd. have conducted running tests with efWING bogies.
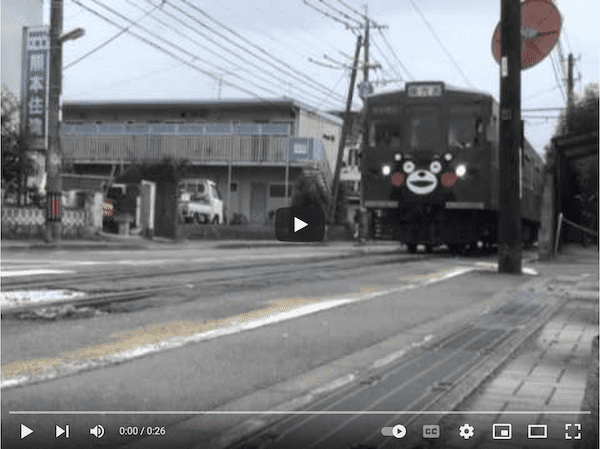
Video cannot be embedded. Click image to see the original video. Credit: S. Takahashi’s footages, YouTube
2018: Chinese railway develops subway train containing carbon fiber composites throughout the vehicle’s structure
In September 2018, Chinese rolling stock manufacturer CRRC unveiled its new generation of metro car called CETROVO at the InnoTrans-2018 International Exhibition in Berlin, Germany. Carbon fiber composites make up not only the bogie frame in this vehicle but the car body, cab, equipment compartment, and equipment body as well. CRRC released a video (below) highlighting this and other features.
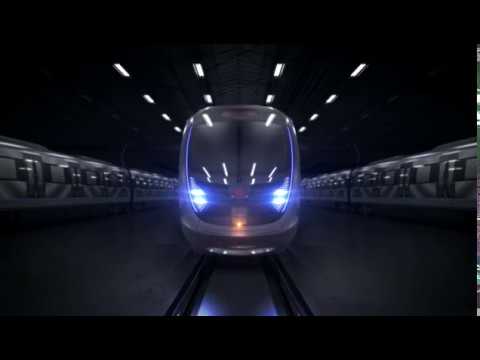
Credit: tjrgx, YouTube
2019: UK industrial–academic consortium makes bogie out of surplus and recycled carbon fiber materials
In 2019, a United Kingdom industrial–academic consortium unveiled a prototype of a rail bogie created out of surplus and recycled carbon fiber materials. Funded by the U.K.’s Rail Safety Standards Board, the prototype represents the culmination of a three-year effort by
- ELG Carbon Fibre Ltd. (Coseley, Dudley, U.K.), which supplied the recycled carbon fiber and performed materials testing;
- Magma Structures (Portsmouth, U.K.), designer and fabricator of the rail bogie;
- University of Birmingham (Birmingham, U.K.) Sensors and Composites Group, which worked with Magma to develop an embedded health monitoring system for the bogie; and
- University of Huddersfield (Huddersfield, U.K.), on whose dynamic test rig the prototype would undergo initial full-scale testing.
Alstom U.K. (London) helped assemble the consortium and provided additional support through consulting and existing bogie design information.
2022: Spanish rolling stock manufacturer designs carbon fiber composite wheelset frames
In April 2022, Spanish rolling stock manufacturer Talgo announced that it had developed a wheelset frame made from carbon fiber-reinforced polymers for its Avril high-speed train. Wheelset refers to a pair of railroad vehicle wheels mounted rigidly on an axle such that both wheels rotate in unison. Bogies typically have two or three wheelsets mounted on them.
The project was supported by the European Commission’s Shift2Rail Joint Undertaking, a public–private partnership established under Horizon 2020 to provide a platform for coordinating research activities to drive innovation in the rail sector. Talgo now plans to conduct running tests with the new frame, operating under real conditions for final acceptance.
Author
Lisa McDonald
CTT Categories
- Transportation