[Image above] Corrosion observed deep in the bondlines of 316 steel metal–metal lap shear specimens conditioned at Pacific Northwest National Laboratory. Credit: National Renewable Energy Laboratory
One cannot think of the movie “Jaws” without hearing the two-note theme song echoing in their head. Yet this iconic music score only came about as a solution to technical difficulties experienced with the originally planned 25-foot animatronic sharks.
“When the crew lowered the first shark into the water, he sank straight to the bottom. Bruce [the shark] performed well in freshwater tests, but no one checked to see if salt water would be a problem. It was. It corroded both the inside and outside of the shark and leaked into the pneumatic hoses. … [As such, director Steven Spielberg needed] to make up something else that didn’t exactly show the shark, but gave the sense the shark was near,” a Bold Entrance article explains.
While this complication ended up for the best for Spielberg, the challenge this anecdote highlights—operating advanced technologies in salt water—remains a pressing issue for marine energy researchers, one that cannot be overcome with a clever soundtrack.
Though less reported on than wind and solar technologies, marine energy technologies are also making waves in the renewable energy market. Intellectual property firm Marks & Clerk reports that the global ocean energy technology market is worth an estimated 53 billion euros (US$56.6 billion) annually, and it is expected to grow as in-development technologies reach commercialization.
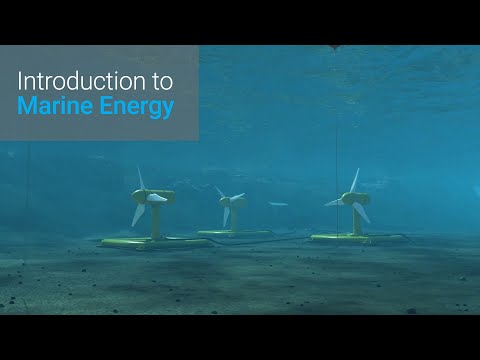
Credit: National Renewable Energy Laboratory, YouTube
As marine energy technologies mature, there is the risk that companies will learn the hard way, like Spielberg, that their devices will not last long in salt water. To help technology developers avoid wasted time and money, a new multiyear study provides much-needed data on the benefits and pitfalls of about 300 different specimens built from materials commonly used in marine energy devices.
The study is a product of the Marine Energy Advanced Materials project, which aims to address barriers and uncertainties facing marine energy developers in adopting advanced materials for structural applications.
A multi-institutional team led by Sandia National Laboratories conducted the multiyear study, which took place from 2019 to 2022. Collaborators on the project include Florida Atlantic University, Montana State University, the National Renewable Energy Laboratory, and Pacific Northwest National Laboratory.
To collect the data, the researchers soaked the specimens for up to 18 months in different types of ocean water baths. The parts were then shipped to the National Renewable Energy Laboratory’s Structural Technology Laboratory for stress tests.
The data revealed that each material had its own merits, performing well in some circumstances and poorly in others. For example, composites with embedded steel generally held up well, but one specific fiberglass composite with a certain steel exhibited significant corrosion.
The biggest surprise for the researchers was that some specimens corroded at a shockingly fast rate in Pacific Ocean water versus Atlantic Ocean water. They hypothesize that it may be due to differences in the saltwater chemistry or oxygen concentrations (Pacific Ocean water has higher oxygen concentrations than Atlantic Ocean water).
The multi-institutional group plans to further investigate this strange reaction, in addition to experimenting with other materials, like recyclable plastic resins, to assess which might be best suited for 3D printing. They also hope to perfect the aging process to make future materials testing a little less cumbersome and more accurate.
Ultimately, “The more understanding you have, the more cost you can save in the long run,” says Paul Murdy, mechanical engineer at the National Renewable Energy Laboratory, in a press release.
The report, “Subcomponent validation of composite joints for the Marine Energy Advanced Materials Project,” is freely available at this link.
Author
Lisa McDonald
CTT Categories
- Energy