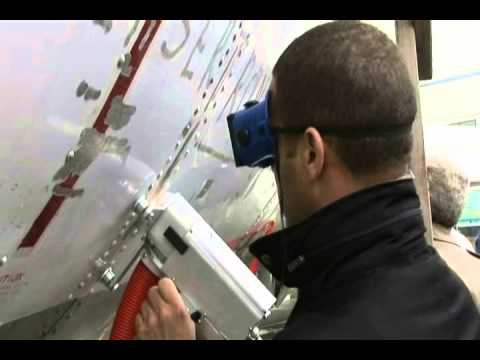
A closed-loop, real-time sensor ensures that only the paint is stripped off the workpiece by a pulsed laser. Credit: GLC/lastertronics1; You Tube.
Lasers were invented in the 1960s (by whom is a made-for-Hollywood story waiting to be told) and at the time were called a “solution looking for a problem.” As laser technology evolved, it turns out there were lots of problems waiting for that solution, and lasers have worked their way into the fabric of everyday life as barcode scanners, CD readers, laser pointers and surgical tools.
Laser engineers and scientists have known for a long time that lasers can deliver enough power to blow away stuff the beam hits, and, consequently, they have found a place on the factory floor for laser machining, laser welding and laser cutting. Laser machining mainly has been a domain for bulk material removal, but a related question has been whether a laser process can be developed to remove very thin layers of material, such as coatings or surface contamination.
The short answer is, yes. Engineers at General Lasertronics Corp. (San Jose, Calif.) have figured out how to remove coatings and other surface layers without damaging the underlying substrate using a pulsed laser. Ralph Miller, vice president of marketing communications and one of the company founders, explained in an interview that the trick is to selectively ablate coatings based on their color or texture.
The first application (and the largest market) is aviation, where it is used to remove paint, corrosion, sealants and dirt for repair and refinishing. Lasers easily could damage the underlying aluminum, so the company developed a closed-loop fiber optic system with a selectivity sensor that provides a real time response. Miller says, “We look before we fire. When the paint’s gone, the laser quits trying.”
Besides color, the tool can be programmed to selectively remove coatings with certain textures, as determined by optical properties, such as reflectivity or luminescence. As long as there is enough contrast (color or texture) between the surface and the substrate, only the surface layer will be removed. In multilayer situations, the selectivity can be programmed such that layers are ablated in successive passes of the tool leaving “setback” areas, for example, areas where the intermediate layers are visible between the primer and the topcoat in a desired pattern.
The laser is a pulsed, Q-switched Nd:YAG and delivers an output of about 300-375 watts to the surface of the workpiece. As the video shows, the pulsed beam “jumps” around on the surface. Miller says the beam itself is in constant motion, either in an x-y scan pattern or a spiral pattern, and the spot does not return to any location it has already visited.
According to the GLC website, the “surface heating is so intense that ablation temperatures are achieved … before heat conduction … can become significant,” that is, the ablation “occurs faster than the heat conduction time constant of the material.” The ablation mechanism proposed by the company is that the “coating compounds vaporize and chemically dissociate, generating gas phase pressure waves that drive materials from the surface at explosive speed.” The pressure waves also serve to propel particulate coating debris away from the workpiece. However, the power remains concentrated in the surface; tests done for the FAA showed that the transient temperature in the base aluminum alloy reached a maximum of about 65°C.
The laser ablation process can be done robotically or by an operator. Miller says part of the beauty of the system is that the training is simple and takes only two to four hours to learn (because of the built-in look-then-fire aspect).
Miller says that there are few coatings the technology cannot handle, although some coatings come off faster than others. Not surprisingly, ceramic and glass coatings are among them. The company conducted successful demonstration tests for removing thermal barrier coatings from power-generation turbines. (Unfortunately, the process was not adopted for non-technical reasons.) The system is being used to remove vitrified silicates from helicopter turbines, a contamination that develops when sand and dust get sucked into hot engines when they fly low in certain environments.
The competing methods for surface layer removal are various forms of blasting (grit, plastic, sand, etc.) and chemical solvents. Both of these generate large amounts of solid waste, according to the GLC’s website, and an example is provided for paint removal. Media blasting can generate about 4.1 pounds of solid waste for every pound of paint removed and solvent stripping generates about 9.1 pounds (plus 165 pounds of liquid waste). In contrast, the laser process generates 0.5 pounds of solid waste for every pound of paint removed.
Other applications that the company is pursuing are nuclear decontamination, surface cleaning for joining processes—such as friction stir welding and composite bonding—and manufacturing equipment maintenance. Miller says that tests show that cleaning the bonding surfaces of composites showed the process “made a significant contribution to the bonding strength.”
GLC is not alone in this marketplace. The Edison Welding Institute (Columbus, Ohio) just announced that it has developed a laser-based paint stripping system. The website is light on details, but the video demonstrates that the system also has a color sensing capability and that the laser can be precision controlled to make patterns, like checkerboards.
Author
Eileen De Guire
CTT Categories
- Aeronautics & Space
- Manufacturing
- Thermal management