[Image above] A silicon carbide power semiconductor from German company Bosch. To prepare for an expected surge in demand for SiC electronics, several semiconductor manufacturers have announced plans to construct new or expand existing fabrication facilities. Credit: Bosch
“Semiconductor chip” has become a household term in recent years as countries around the world rush to increase domestic manufacturing of this key electronic component.
Semiconductor chips are small electronic circuits that provide the foundation for computers and other electronic devices. They consist of complex components, such as transistors and wiring, laid out in specific patterns on top of a wafer, i.e., a thin slice of semiconductor material.
Silicon is the traditional semiconductor used as the wafer in chip fabrication. Many of the massive fabrication plants under construction around the world will produce chips based on this traditional design.
However, despite their ubiquity, silicon-based chips have some disadvantages. For example, silicon’s performance degrades badly at high temperatures. And as manufacturers have worked to place more transistors on each chip, considerable heat is generated.
To dissipate this heat, fans and heat sinks are common ancillary components used to help cool electronics. But while this solution works well for data centers, cooling the electronics used in automobiles is more difficult.
In addition to the heat generated by the chips themselves, chips placed in and around the engine experience high external temperatures. Plus, with the trend toward electric vehicle adoption, cars on average have more semiconductor chips than ever before. While a traditional car needs about 500–600 chips, an electric car has about 2,000 chips—meaning the need for cooling will be far greater.
For this reason, automakers are starting to embrace silicon carbide (SiC)-based chips for automotive applications. Compared to silicon, SiC has excellent thermal conductivity, which enables high-temperature operation with straightforward cooling control. SiC also has a much higher critical electric field strength, which allows it to withstand the higher voltages needed to enable fast battery charging times.

Credit: Nexperia, YouTube
Toyota was an early adopter of SiC, developing and testing SiC power semiconductors for its hybrid vehicles back in 2014. However, Tesla was the first electric vehicle manufacturer to include SiC in its vehicles, with the adoption of a SiC main inverter for the Model 3 in 2017. Now, almost all automakers have expressed an interest in SiC, with companies such as BYD, Hyundai, and Kia choosing SiC modules for their new car models.
To prepare for an expected surge in demand for SiC electronics, several semiconductor manufacturers have announced plans to construct new or expand existing fabrication facilities. For example,
- February 2022: German multinational engineering and technology company Robert Bosch GmbH announced plans to further expand its wafer fabrication facility in Reutlingen, Germany. The expansion will primarily serve the growing demand for microelectromechanical systems and SiC power semiconductors.
- September 2022: U.S. semiconductor manufacturer Wolfspeed announced it will build a new, state-of-the-art, multibillion-dollar materials manufacturing facility in Chatham County, North Carolina. The investment is targeted to generate a more than 10-fold increase from Wolfspeed’s current SiC production capacity on its Durham campus.
- February 2023: Wolfspeed and German global technology company ZF Friedrichshafen AG announced a partnership to create a joint R&D center in Germany to accelerate SiC innovation. The partnership also includes a significant investment by ZF to support Wolfspeed’s planned construction of a SiC device fabrication facility in Ensdorf, Germany.
- April 2023: Bosch announced plans to acquire U.S. chipmaker TSI Semiconductors. It plans to upgrade TSI’s existing manufacturing facilities in Roseville, Calif., so SiC chips can be produced there.
- August 2023: German semiconductor manufacturer Infineon Technologies AG announced it is expanding its factory in Kulim, Malaysia, to increase production of SiC powder modules.
There are challenges to scaling up SiC production, however. The interview below with Wolfspeed senior vice president and general manager Cengiz Balkas summarizes some of these challenges and outlines several solutions.
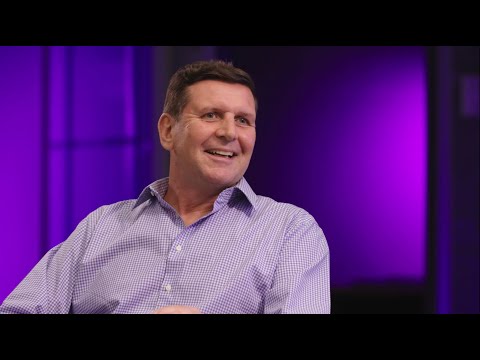
Credit: Wolfspeed, YouTube
Author
Lisa McDonald
CTT Categories
- Material Innovations