[Image above] Researchers at Nanyang Technological University in Singapore created ultrathin, ultralong, high-quality semiconductor fibers that can be woven into different garments. Pictured is a beanie created using the fibers. Credit: NTUsg, YouTube
In a world that is continuously growing louder, brighter, and overall more stimulating, navigating a city’s busy streets can be overwhelming. Fortunately, even though technology is generally the cause of sensory overload, it can also help with cutting through the noise.
For example, wearable technology offers an inconspicuous way to receive help navigating everyday tasks. This category of electronic devices can be worn as accessories, embedded in clothing, implanted in the user’s body, or even tattooed on the skin.
Though medical uses of wearable technology are frequently highlighted, this technology can also help with more mundane but equally vital tasks. Several CTTs in 2021 showed that people with visual impairments accomplished errands more quickly when using specially designed smartwatches, shoes, and white canes.
Smart textiles, or fabrics that have technological components woven into them, are highly desirable for wearable technology because of their potential design freedom. Unlike other smart devices, like the examples given above, smart textiles do not require printed circuit boards or other cumbersome hardware components. Instead, they are flexible and can be integrated directly into any garment, from your hat to your socks.
The challenge with smart textiles, however, is producing them at scale. Current methods for manufacturing crystalline semiconductor fibers, the basis of most smart textiles, typically produce only a few centimeters per hour, and the final fibers are only tens of centimeters in length.
The molten-core method is an exception. In this method, the semiconductor core is melted into a fluid flow that is confined by a glass cladding and thermally drawn into fibers. During a single drawing process, hundreds of meters of semiconductor fibers can be produced at the speed of a few tens of meters per minute.
Achieving this high production rate, though, is often unattainable due to complex stress development in the core that arises from the cladding/core interface. This stress leads to either perturbed or fractured fibers, which restricts the large-scale production of functional fibers.
In a new open-access study, researchers at Nanyang Technological University (NTU) in Singapore conducted a thorough mechanical study on each stage of fiber formation in the molten-core method. Based on their findings, they identified the ideal combination of materials and processing parameters to achieve consistent production of ultrathin, ultralong, high-quality semiconductor fibers.
The NTU researchers wove these semiconductor fibers into hats and shirts, creating smart beanies and tops that can assist in crossing busy roads and navigating crowded museums, respectively, as seen in the video below. They also used the fibers to create a wristband that replaces the bulky sensors in the body of a smartwatch, thus allowing for a slimmer watch design.
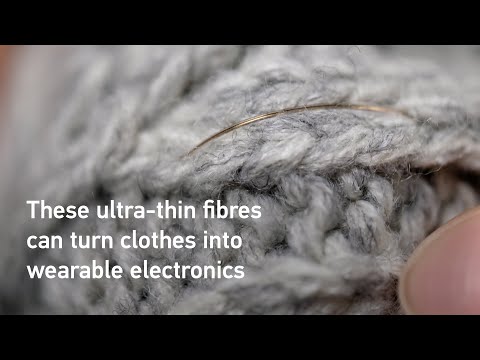
Credit: NTUsg, YouTube
The researchers also evaluated the fibers for their washability by creating a cloth woven with the fibers and throwing it in a washing machine. After 10 cycles, the fibers showed no significant drop in performance.
In an NTU press release, coauthor Dong Li, senior lecturer in the School of Mechanical and Aerospace Engineering at NTU, says their findings could help revolutionize the smart textile industry.
“Our fiber fabrication method is versatile and easily adopted by industry. The fiber is also compatible with current textile industry machinery, meaning it has the potential for large-scale production,” he says.
The researchers plan to expand the types of materials used for the fibers and develop semiconductors with different hollow cores, such as rectangular and triangular shapes, to expand their applications.
The open-access paper, published in Nature, is “High-quality semiconductor fibers via mechanical design” (DOI: 10.1038/s41586-023-06946-0).
Author
Lisa McDonald
CTT Categories
- Material Innovations