[Image above] Credit: Purdue Engineering, YouTube
From a manufacturing perspective, cutting certain metals is harder than you think, and many variables can affect different metals’ machinability.
Some metals are considered “gummy”—meaning that they are soft and ductile. Examples include copper, aluminum, stainless steel, and nickel. And though some of them have desirable properties for making kitchenware, for instance, they pose challenges in the manufacturing process.
“A wide range of products rely on the machining of gummy metals,” assistant professor of mechanical engineering at the University of West Florida James Mann explains in a Purdue University news release. “These could be something we use every day, such as the valve in a sink faucet, or something more critical like a compressor part in the jet engine of an airplane.”
These gummy metals tend to deform when machined, making it costlier for manufacturers. “Gummy metals characteristically deform in a very wiggly manner,” professor of industrial engineering Srinivasan Chandrasekar says in the release. “This wiggly flow involves significant energy consumption, which means that these metals require more force to machine than even some hard metals.”
But Chandrasekar and his team may have come up with a solution involving common office supplies—glue sticks, tape, Sharpies—even liquid paper correction fluid.
The researchers demonstrated that coating gummy metals with ink or an adhesive immediately resulted in cleaner cuts. In fact, the machined surface also improved, according to the researchers.
They arrived at their solution after much trial and error. Previous attempts to solve this problem involved using liquid metal and other chemicals, but those efforts resulted in crumbling, cracking, or tearing of the machined surface.
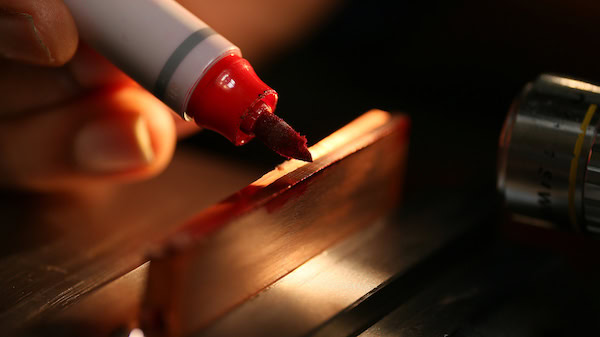
The application of a permanent marker, glue or tape makes gummy metals such as aluminum, stainless steels, copper, and tantalum much easier to cut for industrial applications. Credit: Erin Easterling, Purdue University
“…We began to discover that it’s not any particular chemical that was making a difference, but it’s the nature of these agents to stick to the metal surface,” Chandrasekar explains in the video.
The researchers envision commercializing their process for manufacturers.
“The excitement for the manufacturer is they can finally do something in a way that makes their processes more stable and ultimately reduces cost,” Mann says in the video.
The paper, published in APS Physics, is “Material-Independent Mechanochemical Effect in the Deformation of Highly-Strain-Hardening Metals” (DOI: 10.1103/PhysRevApplied.10.014009).
Watch the video below to learn more about their process.
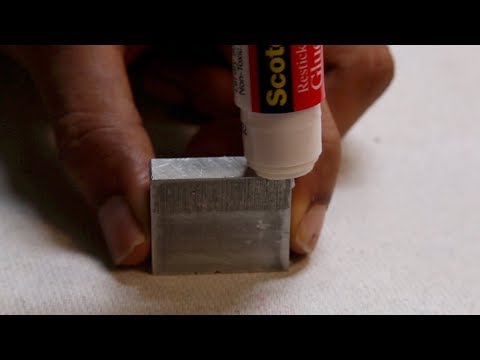
Credit: Purdue Engineering, YouTube
Did you find this article interesting? Subscribe to the Ceramic Tech Today newsletter to continue to read more articles about the latest news in the ceramic and glass industry! Visit this link to get started.
Author
Faye Oney
CTT Categories
- Manufacturing
Spotlight Categories
- Member Highlights