[Image above] An illustration of the rare earth metal, alloy, and magnet manufacturing facility that MP Materials plans to build in Fort Worth, Texas. Credit: MP Materials
From semiconductor chips to baby formula, shortages across numerous and varied industries are driving a serious reevaluation of our supply chain structure.
The need to bolster domestic manufacturing capabilities is one key takeaway from current events. This need is especially true for the rare earths market.
Rare earth elements are a set of 17 metallic elements—the 15 lanthanides plus scandium and yttrium—that are essential components of many advanced technologies. While rare earth elements are relatively abundant in the Earth’s crust, it is uncommon to find these minerals in concentrations large enough to mine.
The largest concentrations of rare earth ores occur in China, which commands an estimated 85% of the rare earth elements export market. The video below summarizes how China positioned itself to take over the rare earths market.
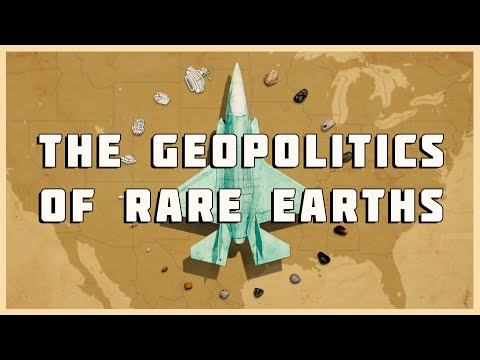
Credit: The Red Line, YouTube
With the possibility of China weaponizing the rare earth supply chain becoming a widely recognized concern, countries are pouring resources into expanding rare earth extraction operations elsewhere, such as in North America and Australia.
However, mining rare earth ores is only the first step in securing the rare earths supply chain. For these ores to be useful, they must undergo refining processes to extract and purify the rare earth minerals so they can be used to manufacture various products.
Unsurprisingly, China controls nearly all of the world’s rare earth processing facilities. Even when rare earth ores are mined elsewhere, they are shipped to China for separation and refining.
However, more companies are starting to lay plans for domestic processing facilities. In the April 2022 issue of Ceramic & Glass Manufacturing, content editor David Holthaus discusses how Las Vegas-based MP Materials is planning to restore the capacity to separate and process rare earths at the California-based Mountain Pass facility sometime late this year. The company also plans to build a rare earth metal, alloy, and magnet manufacturing facility in Fort Worth, Texas.
This month, Texas-based USA Rare Earth made the significant announcement that it will establish the first fully integrated U.S.-based rare earth metal and sintered neodymium magnet manufacturing facility in Stillwater, Oklahoma.
USA Rare Earth controls and operates the Round Top Heavy Rare Earth, Lithium, and Critical Minerals Project in Hudspeth County, Texas. In April 2020, the company acquired the only sintered neodymium magnet manufacturing equipment in the western hemisphere from Hitachi Metals America Ltd. They stored this equipment while deciding where to locate the new magnet operation—which will be the newly announced $100 million Stillwater plant. It is expected to start production in 2023.
In addition to the new facility, USA Rare Earth is collaborating with Texas Mineral Resources Corp. on a pilot plant in Wheat Ridge, Colorado, to improve separation capabilities. The plant first opened in June 2020, and the company provided an update on progress in August 2021.
Author
Lisa McDonald
CTT Categories
- Manufacturing
- Market Insights
Related Posts
Hype cycles: The uphill climb for hydrogen bikes
June 26, 2025