[Image above] Waste glass could be used as packaging material for high-power automotive lighting applications, such as headlamps and side turn lamps, according to a recent open-access study. Credit: rawpixel
Even though glass is 100% recyclable in theory, fulfilling this potential is constrained by current recycling systems. Single-stream recycling specifically, where all recyclable materials are placed in a single bin, is a huge culprit.
This system leads to broken glass of different colors mixing with each other and other recyclables, making it difficult or impossible to reprocess. As a result, all the recyclables are often dumped in a landfill instead.
Fortunately, the circular economy concept, which describes an industrial system that is designed to bring products back into the cycle through reuse, recycling, and repurposing, has made its way out of academia into the real world. Governments and companies have started implementing circular economy strategies and initiatives, including better collection methods for glass.
But collection is only the first step in glass recycling. There must be end-use markets for the waste glass, and identifying suitable markets can be challenging. That is because many applications of glass require specific chemical and mechanical properties, and achieving these requirements with recycled glass is not possible and/or cost effective.
Recent studies have shown, however, that recycled glass can meet the needs of some markets previously considered unsuitable. For example, the Audi Group’s “GlassLoop” pilot project showed that damaged automotive windshields can be recycled back into new windshields.
A recent open-access study led by researchers at SungKyunKwan University and Korea Photonics Technology Institute demonstrate another application of waste glass in automobiles—as packaging for white light-emitting diodes (WLEDs) in headlamps and side turn lamps.
Current commercial WLEDs consist of a blue LED chip (indium gallium nitride) and yellow phosphor (cerium-doped yttrium aluminate garnet, YAG:Ce3+) mixed with a silicon or organic resin. However, when used in high-power applications, such as automobile lighting, the resin used to package the phosphor can become damaged by the heat.
Researchers have considered various types of packaging materials to replace the resin, and phosphor in glass (PiG) is considered an attractive option. PiG is a simple mixture of phosphor with glass powder that is sintered at temperatures of less than 800°C. Replacing the resin with glass improves the thermal and chemical stability of the WLED while maintaining the color conversion efficiency of the conventional phosphors.
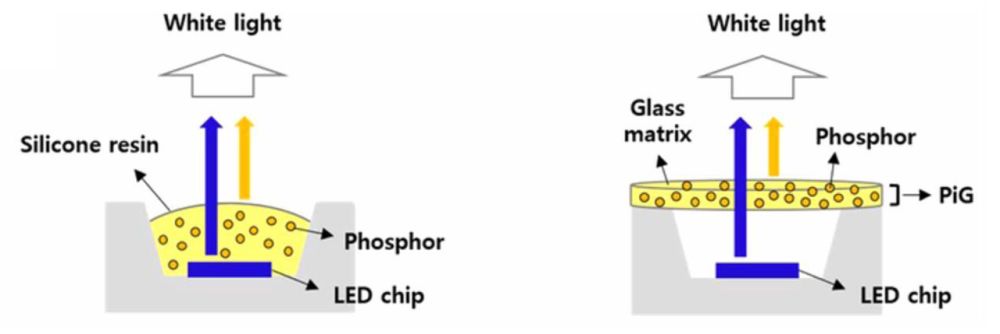
Schematic diagram of conventional white LEDs with silicone resin (left) and phosphor in glass (right). Credit: Chung and Nam, ECS Journal of Solid State Science and Technology (CC BY 4.0)
In the recent study, the researchers explored whether waste glass could be used to prepare PiGs for application in WLEDs. They do not identify the specific waste glass used, except to say it was initially in the form of a cylinder and could not be used for its original purpose due to fracture, failure, and/or scratches. Energy dispersive spectroscopy revealed the glass contained silicon, calcium, sodium, oxygen, and potassium as main components.
They pulverized the glass into a fine glass frit and then mixed it with one of two phosphors, either yellow YAG:Ce3+ or amber europium-doped calcium-stabilized alpha-SiAlON. After mixing, pellets were prepared from the mixtures and heat-treated at 650°C for 1 hour, after which they were polished and diced into square-shaped phosphor converters.
A blue-chip package test revealed that the yellow phosphor-based PiG matched the commercial WLED standards for use in automobile headlamps, while the amber phosphor-based PiG could be used for side turn lamps.
“We believe that this [study] will be a stepping stone for overcoming limitations in the field of [glass] recycling,” the researchers conclude.
The open-access paper, published in Scientific Reports, is “Fabrication of phosphor in glass using waste glass for automotive lighting application” (DOI: 10.1038/s41598-023-27685-2).
Author
Lisa McDonald
CTT Categories
- Environment
- Glass