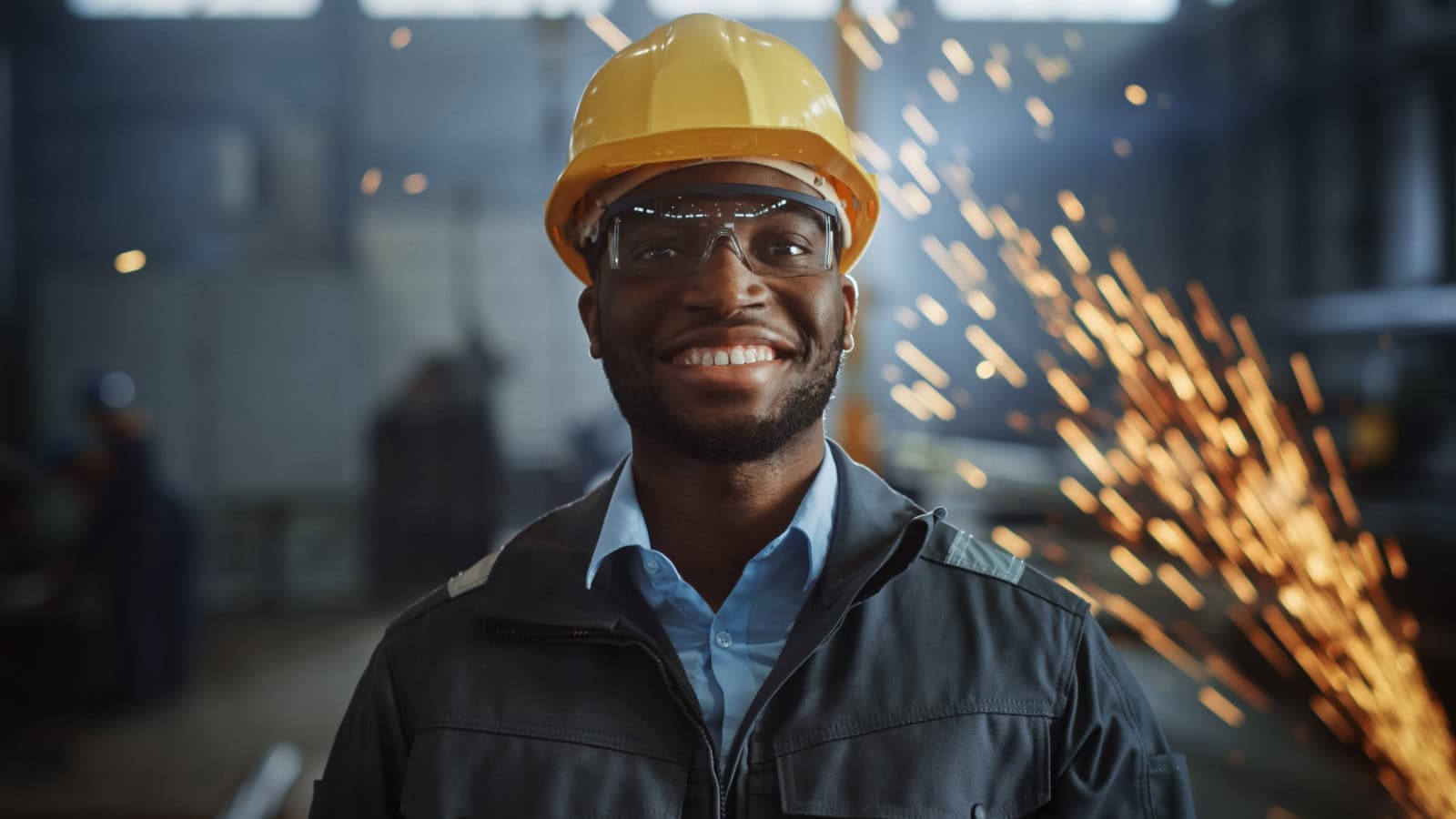
Career Center
The Ceramic and Glass Career Center website at careers.ceramics.org is the best place for job and internship seekers to find a great ceramic and glass career opportunity.
ACerS Mentor Program
ACerS Mentor Program is designed to equip you with the insight, tools and connections necessary to make a lasting impact in your career.
Resources
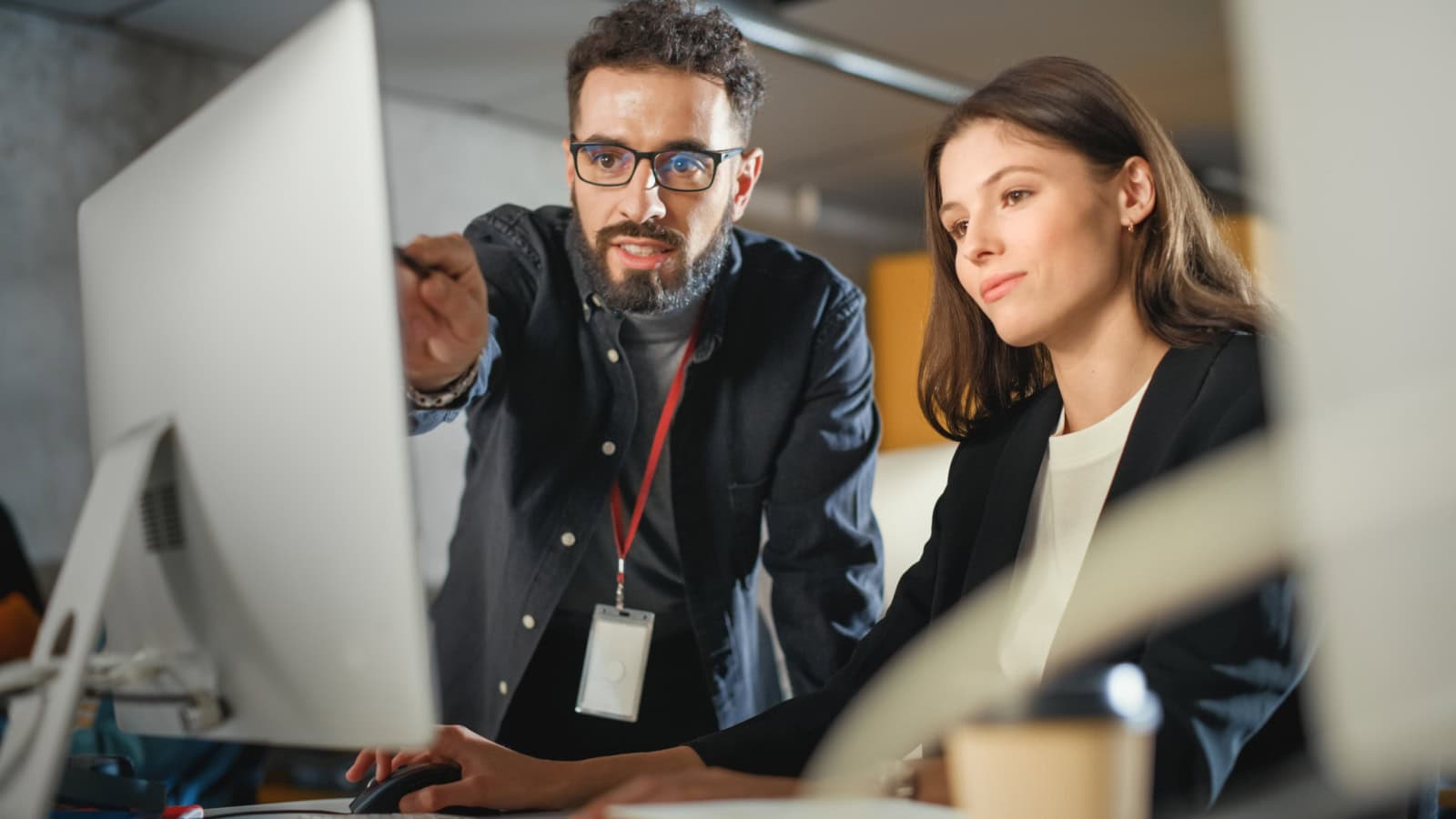
Communicating Science
Communicating science to a nonspecialist audience is something that is done almost daily for a scientist, and a skill that is always going to be important to future innovations in science. Learn more about some useful resources that help communicate effectively to nonspecialist audiences.
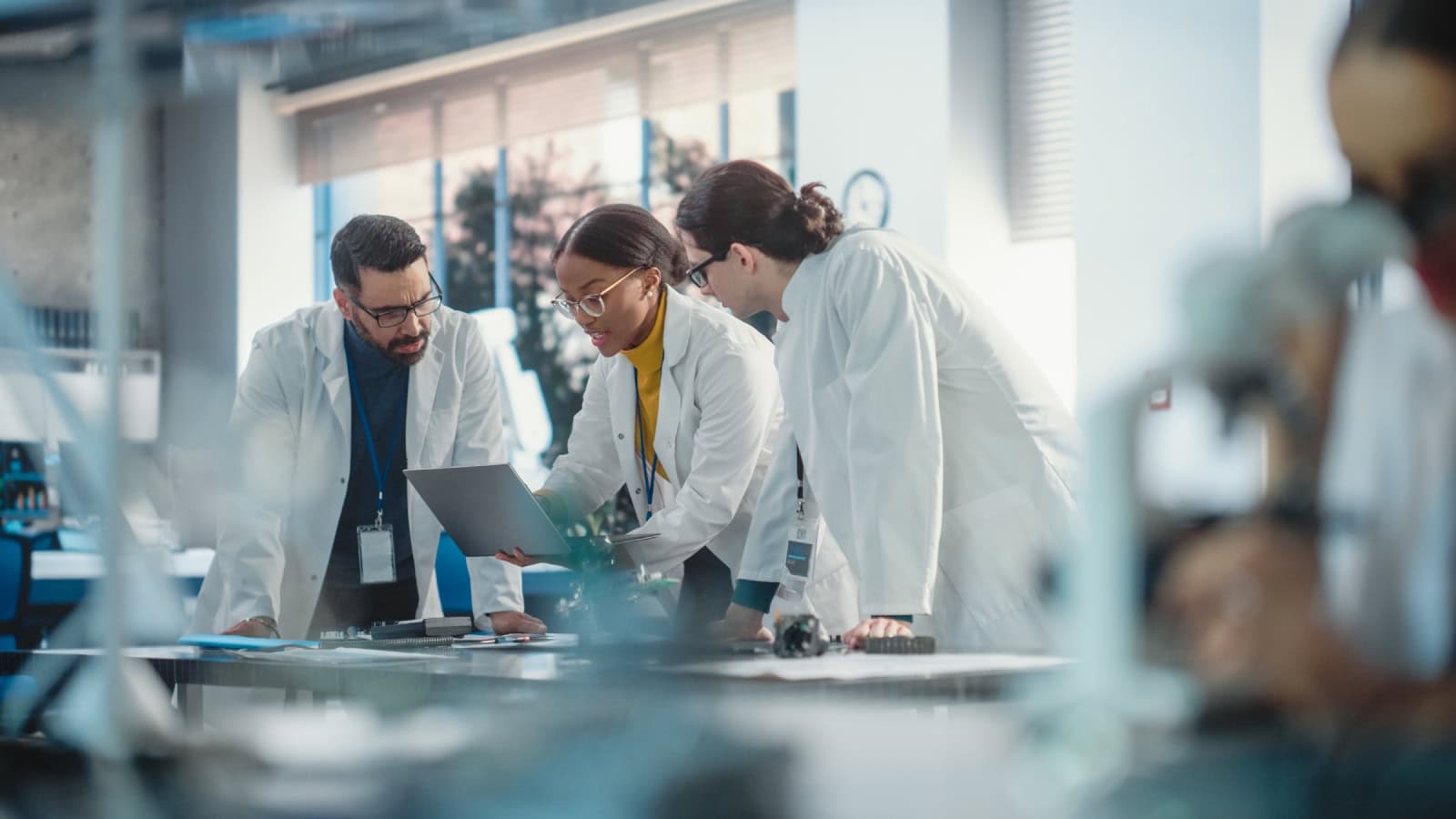
Promoting Full Participation in Science
The American Ceramic Society represents all people involved in the global ceramics and glass community. Check out the resources page to learn more on how ACerS promotes full participation in science.
ACerS Awards
ACerS has the privilege of being a professional home to global leaders in the ceramics and glass community. It is with great respect that ACerS recognizes those members that distinguish themselves within our community.
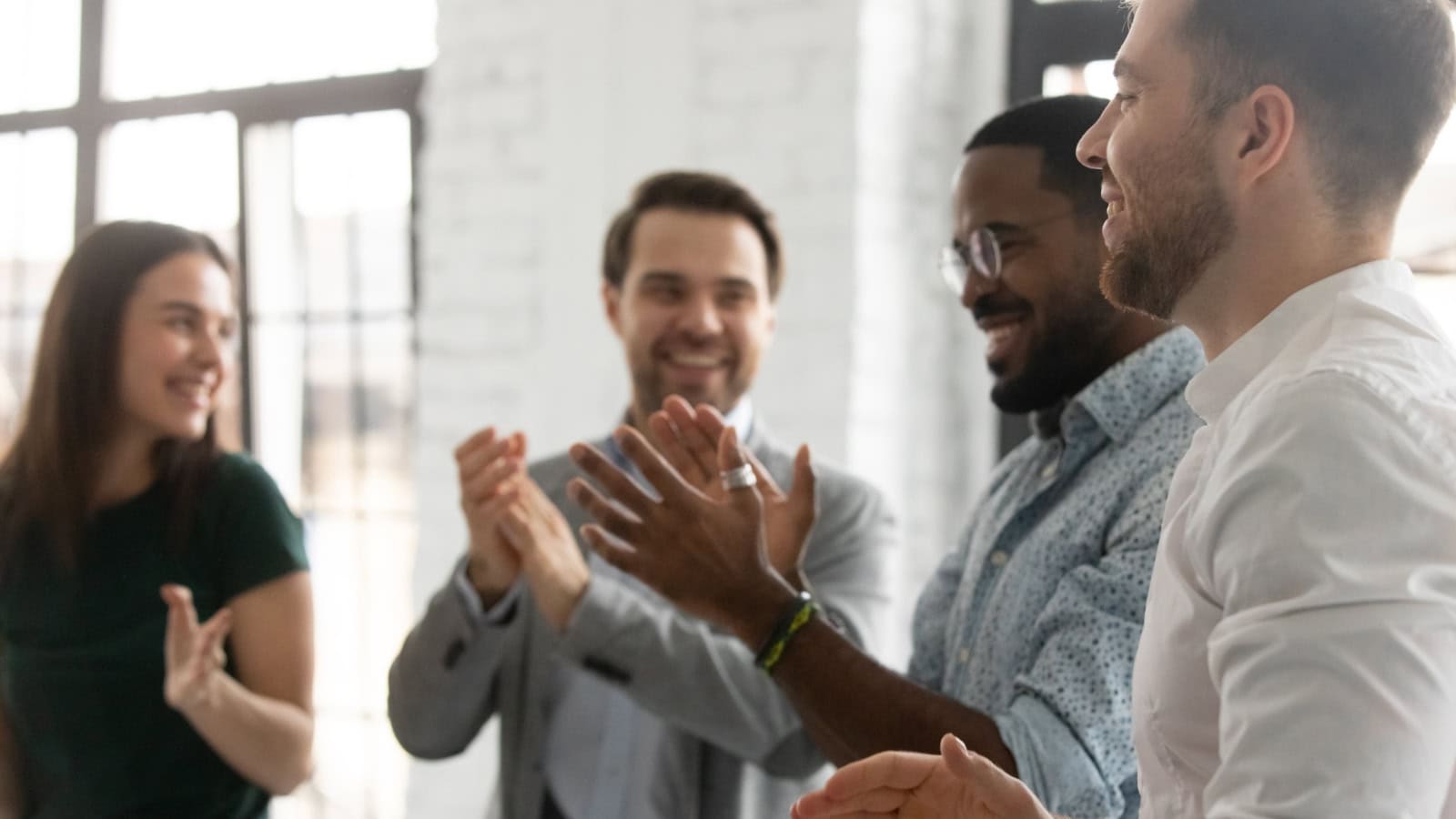
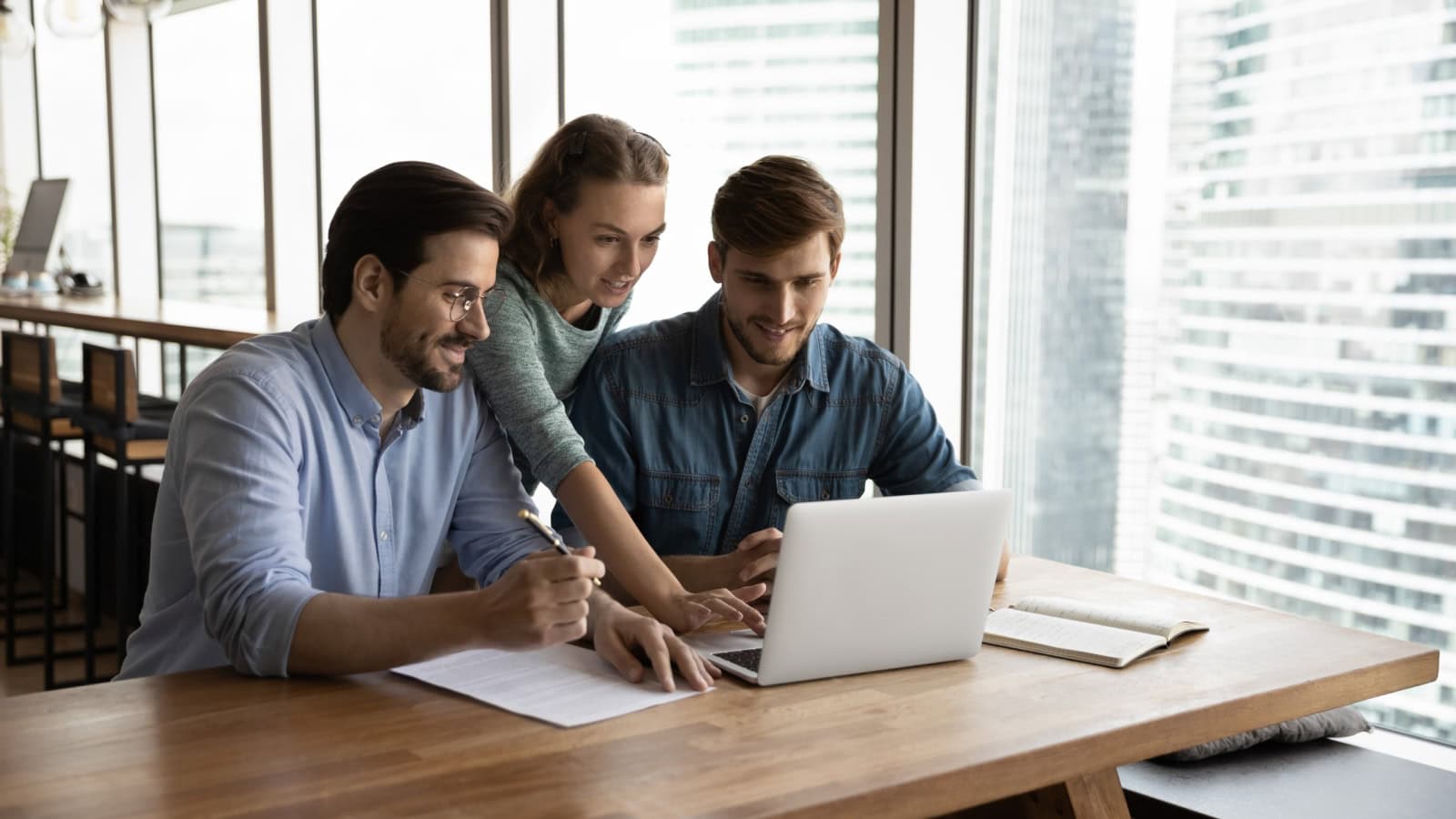
Volunteer with ACerS
Want to support the next generation of ceramic and glass materials scientists? Or how about pursue one of the many micro-or-macro-volunteer positions available at ACerS.