[Image above] Credit: ACerS
At the virtual industry exposition Ceramics Expo Connect last week, the majority of discussions focused on emerging and future applications of ceramic materials, including in sustainable energy technologies and aerospace. But what about current trends in the ceramic manufacturing industry? What applications and processes are mainstays of the industry right now?
Those questions were the focus of the first-ever Ceramic Manufacturing Solutions Conference, which took place on September 29. Originally scheduled to take place alongside Ceramics Expo in the spring, CMSC was rescheduled as a virtual event for the week after Ceramics Expo Connect in light of the ongoing pandemic.
“I would like to express my deepest appreciation to ACerS staff for their fantastic job navigating these turbulent times,” ACerS president Tatsuki Ohji says.
Sixty-nine registrants from 13 countries, including 10 students, registered to attend the one-day event, which was organized into three main sessions: Testing, Quality, and Health & Safety; Ceramic Processing; and Raw Materials.
Don Bray of SINTX Technologies, who co-organized the event, observed, “The talks were very informative, and the speakers did a great job covering some complex topics. As a member of the ACerS Manufacturing Division, focusing on solutions to difficult challenges of ceramic processing is really important for our industry.”
The day kicked off with a keynote presentation by Doug Freitag, technical director for government affairs at the United States Advanced Ceramics Association (USACA). Since the founding of USACA in 1985, Freitag says the advanced ceramics industry has made significant progress in numerous applications.
Currently, the USACA is focused on helping to advance the fields of aerospace and ballistic protection, among others, and Freitag spent time describing the history and current status of research on transparent ceramic armor and ceramic fiber reinforced ceramic matrix composites for gas turbines.
Following Freitag’s presentation, ACerS director of meetings and marketing Andrea Ross presented Allied Mineral Products vice president of research & development Dana Goski and manager of special projects Matthew Lambert with this year’s John E. Marquis Memorial Award, in recognition of their paper “Engineering resilience with precast monolithic refractory articles.”
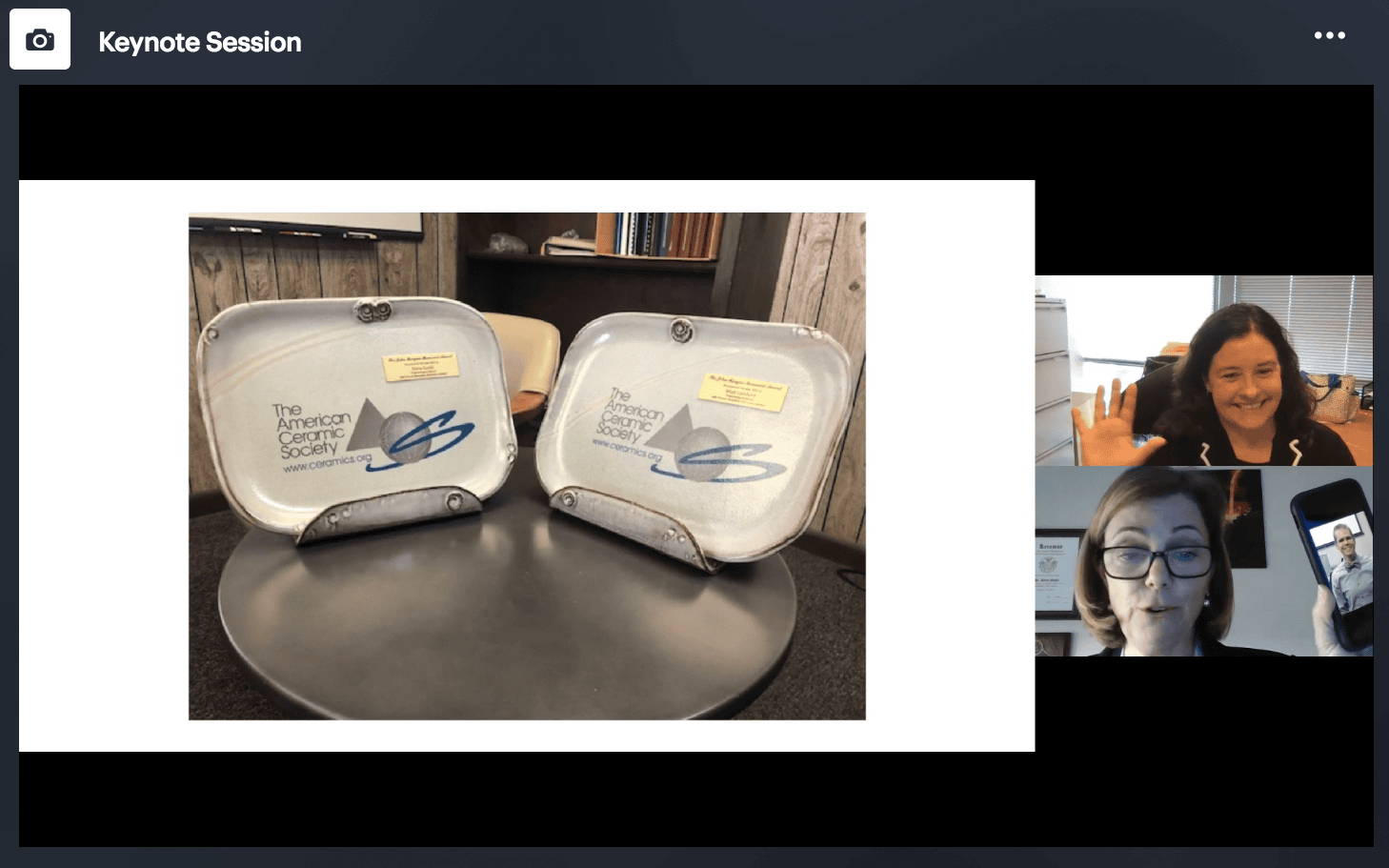
During the three main sessions, several topics were discussed in regard to each theme, including the following with a few key points.
- Occupational Safety and Health Administration (OSHA) citations and ASTM test methods for powder characterization under Testing, Quality, and Health & Safety.
- J. Doug Jeter (Harrop Industries) covered the top ten reasons for OSHA citations. He says, “You are doing your job well when no [safety] incidents occur.”
- Tony Thornton (Micromeritics) presented a thorough survey of powder characterization tools and ASTM standards. The key takeaway was that manufacturing quality begins with well characterized powders.
- Failure modes & effects analysis (FMEA), additive manufacturing considerations, silicon nitride production, and specific volume diagrams under Ceramic Processing.
- Bill Walker (Federal Mogul) showed how manufacturers use FMEA methodology to systematically identify and eliminate all possible failure modes in manufacturing products.
- Cathleen Hoel’s (GE Research) presentation on additive manufacturing outlined some exciting opportunities but included a reality check. She says AM may be the right forming process when (1) there are significant design benefits, (2) the part cannot be made with traditional tooling, and (3) it is not prohibitively expensive. She encouraged engineers and designers to think creatively about component structure but cautioned, “Complexity is not free; it is accessible.”
- David O’Brien (SINTX) discussed the stringent manufacturing and quality testing inherent with their silicon nitride spinal implant business—and the importance of creating a culture of quality among their staff.
- Bill Carty (Alfred University) addressed the issue of uniformity in plastic forming processes such as extrusion, tape casting, and castable slumping, and showed how to use specific volume diagrams to optimize water content.
- Electric arc fusion of mullite ceramics and the role of alumina in various applications under Raw Materials.
- Matt Creedon (Washington Mills) gave the audience a new appreciation for the engineering that goes into manufacturing fused alumina and mullite products in 10-ton batches.
- Mark Snyder (Almatis) talked about the fast-growing semiconductor market for alumina, mostly for semiconductor processing equipment and thermal interface materials. The importance of raw material purity and characterization came up again.
A networking session after the main sessions concluded the conference.
“Working in the manufacturing environment, the CMSC event exceeded expectations; the speakers and the content of their talks were both excellent. I’m excited for this event to continue,” says co-organizer Keith DeCarlo of Blasch Precision Ceramics.
ACerS will host its 122nd Annual Business Meeting virtually on Monday, Oct. 5, from 10–11 a.m. ET. The Society continues to expand its opportunities for online learning as well, which you can learn more about here.
Author
Lisa McDonald
Spotlight Categories
- Meeting Highlights
Divisions
- Manufacturing