[Image above] Illustration of a Mars transit habitat and nuclear propulsion system that could one day take astronauts to Mars. Credits: NASA
With the Artemis I mission finally launching into space, the goal to once again send people to the moon took its first step toward realization. But many material innovations are still needed to turn these objectives into reality. Ceramic and glass materials are sure to play a role, as detailed in the new December 2022 issue of the ACerS Bulletin.
The cover story overviews the many applications of ceramics and glass in space exploration and travel, from launch and return to all the travel, data collection, and learning in between. It also hints at nascent applications that will likely appear on future missions.
Next-generation propulsion technologies is one area where ceramics are expected to play an important role. To achieve manned missions to Mars and other faraway planets, spacecraft will need to maximize fuel usage. While there are numerous ways to approach this goal, nuclear thermal propulsion (NTP) is one technology actively on NASA’s radar.
Nuclear propulsion derives from two atomic processes, fission and fusion. NTP generally implies fission, i.e., a reaction where the nucleus of an atom splits into two or more smaller nuclei.
To achieve fission propulsion, a “hot rock” of uranium atoms releases high-energy neutrons to create heat. This heat is used to heat up hydrogen propellant, which is then expelled through a nozzle to produce thrust.
NTP provides high thrust and twice the propellant efficiency of conventional chemical rockets. However, the extreme conditions within the reactor—elevated temperatures up to 2850 K (~4,700°F or ~2,600°C), high-energy ionizing radiation, and flowing hydrogen propellant—requires NTP reactors to be fabricated from materials that can withstand these conditions.
Ceramic–metal (cermet) composites are among the candidate materials for NTP reactors. These composites consist of ceramic fuel particles, such as uranium dioxide or uranium mononitride, embedded in a metal matrix, which is typically tungsten due to its high melting point and excellent compatibility with hot hydrogen.
To model accurate reactor and fuel performance, researchers must have access to material property databases containing experimentally validated property models. But such databases are incomplete or missing for many NTP cermets. Even where the models can qualitatively predict effective properties, experimental data is lacking for operation at temperatures above 2000 K (~3,100°F or 1,700°C).
In a recent study, researchers from Missouri University of Science and Technology and NASA Marshall Space Flight Center, including ACerS Fellows Bill Fahrenholtz and Greg Hilmas, characterized the high-temperature thermal properties of molybdenum tungsten–hafnium nitride (MoW-HfN) cermet at elevated temperatures.
Hafnium nitride is a nonradioactive surrogate material for uranium mononitride. The two nitrides are chemically and structurally similar, and so allows experiments to be conducted without the release of high-energy ionizing radiation.
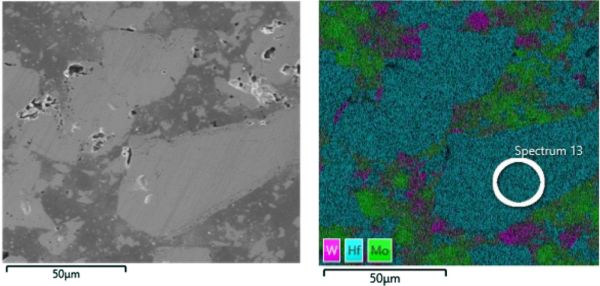
Scanning electron microscopy micrograph (left) and energy-dispersive spectrometer map (right) of MoW-HfN specimen. Hafnium nitride (blue) particles were confirmed to be surrounded by molybdenum (green) and tungsten (pink) matrix. Credit: Mudd et al., Journal of the American Ceramic Society
The researchers used the laser flash method, differential scanning calorimetry, and push rod dilatometry to measure the thermal diffusivity, specific heat capacity, and coefficient of thermal expansion (CTE) of MoW-HfN, respectively. They used these values to calculate the cermet’s thermal conductivity.
Based on the experiments, diffusivity values ranged from about 0.18 cm2/s at 200°C to 0.15 cm2/s at 1,800°C. The CTE was measured up to 1,600°C, giving values between 6.0 and 9.0 μm/m.
Measurement of the specific heat capacity was limited to temperatures less than 600°C, but it was validated by the rule-of-mixtures (ROM) model. So, when calculating the cermet’s thermal conductivity for temperatures above 600°C, the values are considered semiempirical because the ROM model was used to extrapolate the specific heat capacity.
Following the experiments, the researchers compared these various property values to ones calculated by different property models to determine which model(s) best represents the system.
As noted above, the ROM model did a good job calculating the specific heat capacity. Meanwhile, the Bruggemann model, which is based on the idea that a composite can be constructed incrementally by making small changes to the material, showed reasonable quantitative agreement with the calculated thermal conductivity.
However, none of the property models considered in this work could satisfactorily predict the CTE for HfN-MoW.
“Therefore, additional high-temperature thermal property data should be gathered for HfN and the MoW binder (both heterogeneous and solid solution),” the researchers state.
In the future, the researchers write that characterization of MoW-UN cermets prepared using a similar processing route should be performed and thermal properties should be compared to those of MoW-HfN.
The paper, published in Journal of the American Ceramic Society, is “Thermal properties of HfN-MoW surrogate cermet fuel for nuclear thermal propulsion” (DOI: 10.1111/jace.18870).
Author
Lisa McDonald
CTT Categories
- Aeronautics & Space
- Material Innovations