[Image above] The 2020 Fort GT Liquid Carbon is encased in sculpted carbon fiber—but that high-end material comes with a high-end price tag. Can new strategies finally make carbon fiber a more affordable material? Credit: Ford
At the end of May, NASA astronauts Bob Behnken and Doug Hurley reached the International Space Station after a short yet stylish 19-hour journey. Powered by the SpaceX Falcon 9 rocket, their escape from Earth’s atmosphere was historic in that it marked the first time a private company launched humans into orbit.
Behnken and Hurley will stay in orbit for up to four months, helping complete work and research aboard the International Space Station.
If only they were a little earlier, perhaps part of the astronauts’ research could have involved Lamborghini’s carbon fiber composites, which were launched last November for six months of testing under extreme temperatures and radiation exposure.
Perhaps surprisingly, those experiments were part of an agreement between Lamborghini and the Houston Methodist Research Institute to research biocompatibility of composite materials for medical devices—although Lamborghini certainly has interests in carbon fiber materials for automotive applications as well.
In fact, carbon fiber has long found application, excitement, and promise in the automobile industry. The material’s high strength and stiffness yet low weight make it the perfect substitute for lightweighting efforts to improve vehicle fuel efficiency—a task where many other ceramic and glass materials also find application.
Beyond practicality, however, carbon fiber is an attractive option in the automotive world for its looks as well—take a glance at the 2020 Ford GT Carbon Liquid and you’ll see what I mean.
Yet the problem that continues to plague carbon fiber is a familiar one with many materials—high cost. Although that gleaming 2020 Fort GT Carbon Liquid is a sight to behold, its price tag of $750,000 is not so pretty.
The price of carbon fiber has come down considerably since it first became commercially available, but carbon fiber still costs 10-times the price of steel, making it difficult to rationalize the price difference for automobiles except in racing vehicles or high-end models like the Ford GT.
According to new research, however, a little dash of graphene may be the perfect recipe to finally make carbon fiber more affordable, potentially paving the way to more widespread application of this promising material.
A team of researchers from The Pennsylvania State University, the University of Virginia, and Oak Ridge National Laboratory, in collaboration with industry partners Solvay and Oshkosh, showed that adding just a small amount graphene to carbon fiber precursor materials can significantly reinforce the strength of the fibers by catalyzing high structural alignment, providing potential avenues to lower carbon fiber’s cost.
“Currently most carbon fibers are produced from a polymer known as polyacrylonitrile, or PAN, and it is pretty costly,” Małgorzata Kowalik, researcher in Penn State’s Department of Mechanical Engineering, says in a Penn State press release. “The price of PAN makes up about 50% of the production cost of carbon fibers.”
PAN requires a lot of high-temperature processing to generate fibers with sufficient strength and stiffness, and all this processing equates to an expensive end material.
The press release continues: “PAN is used to create 90% of carbon fibers found in the market today, but its production requires an enormous amount of energy. First, PAN fibers have to be heated to 200–300 degrees Celsius to oxidize them. Next, they must be heated to 1,200–1,600 degrees Celsius to transform the atoms into carbon. Finally, they have to be heated to 2,100 degrees Celsius so that the molecules are aligned properly. Without this series of steps, the resulting material would lack its needed strength and stiffness.”
Though less expensive carbon alternatives have been explored, they have not yet been able to generate the high-quality carbon fibers that PAN produces.
But according to the new research, doping PAN fibers with a small amount of graphene, just 0.075 wt %, produces carbon fibers with a tensile strength of 1916 MPa and Young’s modulus of 233 GPa—225% higher strength and 184% higher Young’s modulus compared to similar fibers without added graphene.
The researchers show in their open-access paper that this enhanced mechanical strength traces back to graphene’s ability to reduce the size of pores in fibers spun from PAN, which they speculate is because flat graphene nanosheets help guide PAN molecules as they solidify into fibers, reducing large voids that structurally weaken the fibers.
When processed, these better-aligned PAN molecules result in stronger, reinforced carbon fibers.
Atomistic and molecular dynamics simulations showed this reinforcement is attributed to several factors. “The simulation results show that the addition of graphene introduces favorable edge chemistry, promotes carbon content, enhances polymer chain alignment, and increases crystallinity,” the researchers write in the paper.
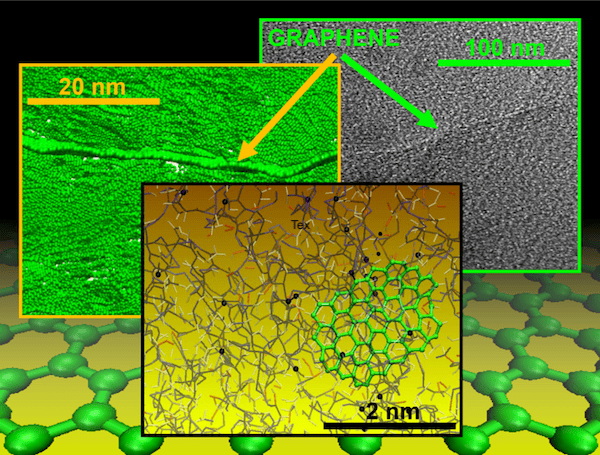
Computer simulations show that adding graphene to the carbon fiber production process greatly strengthens the material. Credit: Margaret Kowalik and Adri Van Duin; Penn State
Ultimately, the findings could translate into strategies that require less processing to generate sufficiently strong carbon fibers, which would reduce cost. Another possibility is that less expensive precursor materials could be used as carbon sources that still can generate adequately strong carbon fibers with graphene’s assistance.
Who knows—maybe future model years of that gleaming Fort GT Carbon Liquid might even be (more) affordable.
The open-access paper, published in Science Advances, is “Graphene reinforced carbon fibers” (DOI: 10.1126/sciadv.aaz4191).
Author
April Gocha
CTT Categories
- Nanomaterials