[Image above] An angle grinder attacks a new ceramic–metal composite—but who will win the battle? Credit: Stefan Szyniszewski, YouTube
If you are a material, who is your enemy?
Of course, identifying the enemy depends on the material, and it also depends on your definition or perception of what an enemy is—whether that’s something that causes you physical harm, tarnishes your reputation, or refuses to recognize your value.
While I suppose materials might have a plethora of potential enemies, if I was a material, my most hated enemy just might be a rotating cutting tool.
Harnessing the destructive potential of force and rotation, cutting tools like saws, drills, and angle grinders can obliterate the superlative properties that materials work so hard to perfect. And even when materials are designed to work against the power of these tools, the materials still often fail.
So what if instead we designed materials to work with the power of cutting tools rather than against them? While that may sound counterintuitive, it is just what an international group of researchers has done—and their preliminary tests show the ceramic–metal composite material they designed resists damage beyond shallow surface cuts.
The researchers, from Durham University, University of Surrey, and University of Stirling in the U.K. and Fraunhofer Institute and Leibniz University Hannover in Germany, developed a ceramic–metal composite that, despite being just 15% as dense as steel, is nearly uncuttable. By harnessing the power of vibration, the material directs tools’ destructive energy back upon themselves, wearing the tools down before they can inflict serious damage on the material.
The researchers named the material Proteus after scientist and philosopher Francis Bacon’s idea, articulated in his book Sylva sylvarum, that matter is never destroyed but instead transformed into alternate forms.
The strong yet light composite could offer new hope for a more secure material for doors, locks, and much more.
The material—a flexible aluminum core embedded with alumina spheres—owes its strength to a hierarchical structure that is inspired by nature. Specifically, it mimics the structure of nacre and many other naturally occurring materials that are stronger as a whole material than as their individual units.
For instance, nacre has a hierarchical structure of stacked crystal calcium carbonate platelets that are mortared together with inorganic materials. Together, this multilevel structural organization makes nacre much stronger as a whole than would be predicted based on its individual material components.
So, using nature as inspiration, the researchers designed the ceramic–metal composite with similar system-level interactions, providing strength that exceeds the mechanical properties of the material’s individual components of a cellular aluminum core and embedded alumina spheres.
To make the cellular aluminum core, the team mixed aluminum powder with a titanium foaming agent and then cold-compacted and extruded the material into rods. Then, they cut these rods into smaller pieces and stacked them together with 13-mm-diameter alumina spheres in a steel box.
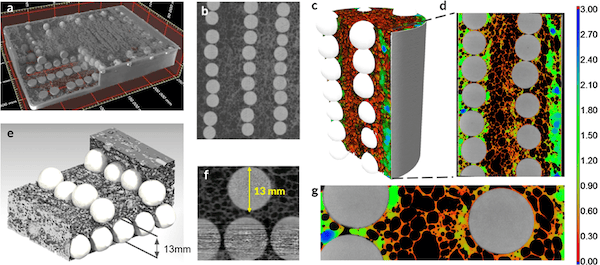
Hierarchical structure of the proposed metallic-ceramic metamaterial. (a) Sandwich panel sample (245 mm × 172 mm × 40 mm), (b) ceramic spheres are organized in lines, (c) cylindrical specimens (60 mm diameter × 150 mm) had a vertical organization of ceramic spheres, (d) cross-section of the cylinder with colors corresponding to the wall thickness of cellular aluminum, (e) ceramic spheres are not in contact with one another but are separated by aluminum cells, (f) foam cells are an order of magnitude smaller than ceramic spheres, (g) thickness of aluminum cell walls varied mostly from 0.2 to 0.4 mm. Credit: Szyniszewski et al., Scientific Reports (CC BY 4.0)
Heating the combination to 760ºC in a furnace melded the individual components together to create Proteus—a cellular aluminum core with 73% porosity, studded with embedded ceramic spheres and bordered by steel alloy faceplates.
Putting this material to the test against potential enemies of an angle grinder (equipped with sapphire-finished cutting discs) and a drill, the researchers showed the composite resists most damage beyond surface cuts, performing better than rolled homogeneous armor. See for yourself in the video below.
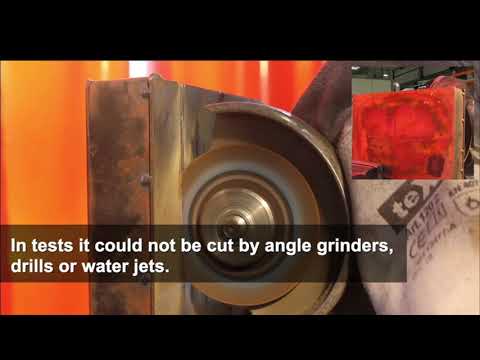
Credit: Stefan Szyniszewski, YouTube
Although they only compose 14% of the volume of the cellular metallic core, the ceramic spheres are a critical component of Proteus’s strength. So you might expect the researchers used the densest, hardest alumina spheres they could find. But again, the team took an usual approach—they instead used alumina spheres with suboptimal densification, which allowed the team to design the composite material with a secret weapon up its sleeve.
When a cutting tool slices into Proteus and encounters an alumina sphere, it breaks apart into fine particulate matter—creating a “sandpaper-like, vibrating interface with the cutting disc,” the researchers write in the paper describing their findings. The abrasive action of the alumina particulates quickly wears down cutting surfaces, preventing the tool from penetrating further into the composite. In addition, the small alumina particles better resist penetration “due to the increase of their system level resistance under high strain rates,” the researchers note.
In other words, the material is willing to sacrifice a few alumina spheres to protect its overall integrity, allowing it to last much longer in the face of an enemy attack.
But an abrasive surface isn’t all the composite has in its arsenal to thwart its destructive attackers.
The natural frequency of the material also works against cutting tools—as the tool spins, it generates vibrational frequencies that interact with those of the spheres, essentially amplifying vibrations at the interface and further wearing down the tool before it can make significant progress into the material.
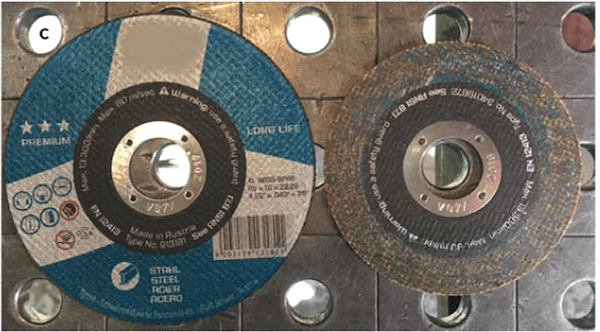
Proteus significantly wears down the cutting disc of an angle grinder within one minute. Credit: Szyniszewski et al., Scientific Reports (CC BY 4.0)
Combined, these features give Proteus a one-two-three punch—a highly abrasive interface, heat generated at the interface due to that friction, and vibrations—that work together against the cutting tool, destroying it before it can destroy the material.
In addition, the researchers speculate in the paper that localized heating could enable a phase change in alumina, densifying it to further resist cutting.
Although the team is still investigating the full mechanism and full potential of Proteus, they believe “The configuration of our new architected material can be tailored to a broad range of applications.”
For example, the material could be used for security applications, like doors, safes, barriers, and locks. But the technology could also possibly be used to make cut-resistant clothing and protective gear, such as the soles of shoes or forearm guards, because the composition and configuration of the metal–ceramic composite is adjustable, something the team is only starting to explore for its potential.
“One can tune foam porosity, alter base materials, adjust the size of spheres, and their packing pattern,” they note in the paper. “We can also modify the thickness of the sandwich panels, the diameter of the cylinders, the thickness of faceplates and manufacture curvilinear geometries effectively. The demonstrated components can be welded and bonded with other materials to form larger structural systems.”
You can hear lead author Stefan Szyniszewski, assistant professor at Durham University, talk more about the design approach to Proteus here.
The open-access paper, published in Scientific Reports, is “Non-cuttable material created through local resonance and strain rate effects” (DOI: 10.1038/s41598-020-65976-0).
Author
April Gocha
CTT Categories
- Material Innovations